Robotic Light-Gauge Truss Welding Cell
- Home
- Recent Projects
- Robotic Light-Gauge Truss Welding Cell
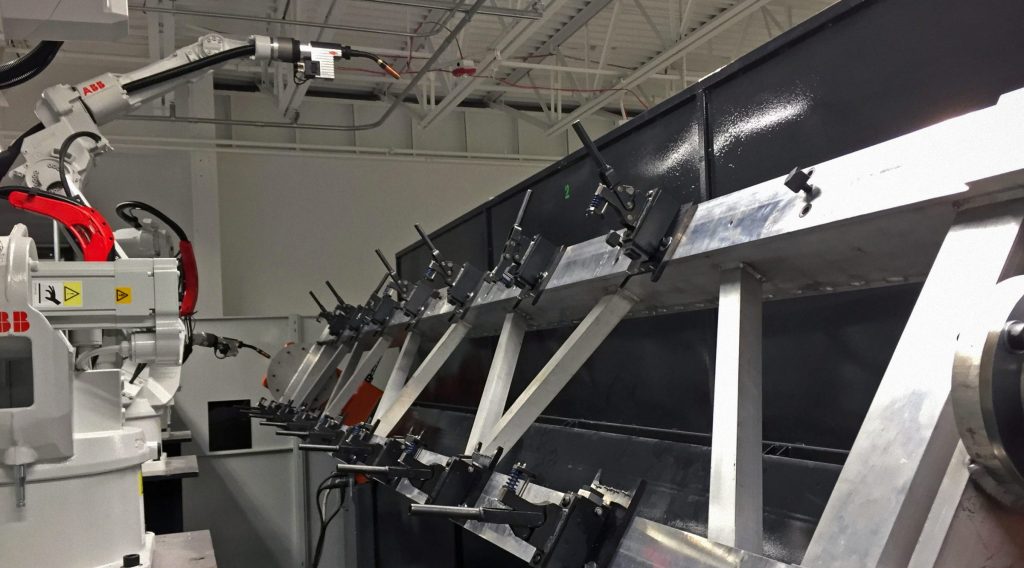
Project summary
MWES provided this structural steel manufacturer with a robotically automated light-gauge galvanized steel truss welding system.
The Challenge
Welding of large structural frames is difficult both ergonomically for the operator and in finding enough qualified welders to keep up with throughput. This structural steel firm needed a system to facilitate rapid growth without needing to hire additional welders and the system had to handle trusses 4 to 16 feet in length. Additionally, the ergonomics of the system was highly important as the tooling and the parts needed precise clamping to weld properly which also restricted the operator’s reach to the desired weld points.
The Solution
MWES provided our customer with a robotic automation cell that utilizes three welding robots and a Ferris wheel positioner with a servo head/tailstock in each station. The system is complete with a safety cell and weld equipment for each robot. The ancillary weld equipment is shared between the robots to keep the overall investment down. The system operator is only responsible for loading and unloading the truss assemblies and clamping them down on the positioner.
The operator scans the barcode for the truss and tooling quadrant to be run at one of the two operator workstations. The workstation stations can be set up to run the same truss assemblies or different models and quantities. The operator loads the proper truss materials in the correct locations and verifies that all manual clamps are engaged. After leaving the station and the loading station is all clear, the operator presses the reset button on the panel this confirms to the robot controller the station is ready for automatic operation.
The Ferris positioner indexes to the robots’ side and the robots begin the assigned welding operation. After the robot starts the execution of the program the operator can enter the workstation in the operator area and unload the previous welded truss assembly. Once the welding is complete on the current truss, the robots wait for the operator-ready signal for the positioner to index back to the operator’s side. During the execution of the weld sequence, the robots perform torch maintenance routines at predetermined intervals.
Impact to the Customer
MWES designed a robotic weld cell that handles structural truss welding with speed and ease. The automation system has a throughput of three operators per shift and can run multiple shifts per day without endangering the system operators. The robotic system produces consistently clean welds that are of 1/32 inch tolerance.
Midwest Engineered Systems has a wide range of experience in integrating welding automation systems. If you’re looking to improve your welding throughput, we have the knowledge and experience to make the project a success.
Contact us to learn about how Midwest Engineered Systems can automate even your most challenging operations today!
Innovation Through Automation
Client Details
A supplier of prefabricated steel framing materials for building construction based in Denver, CO.