Multi-Process Welding
- Home
- Industrial Automation Capabilities
- Robotic Welding Systems
- Multi-Process Welding
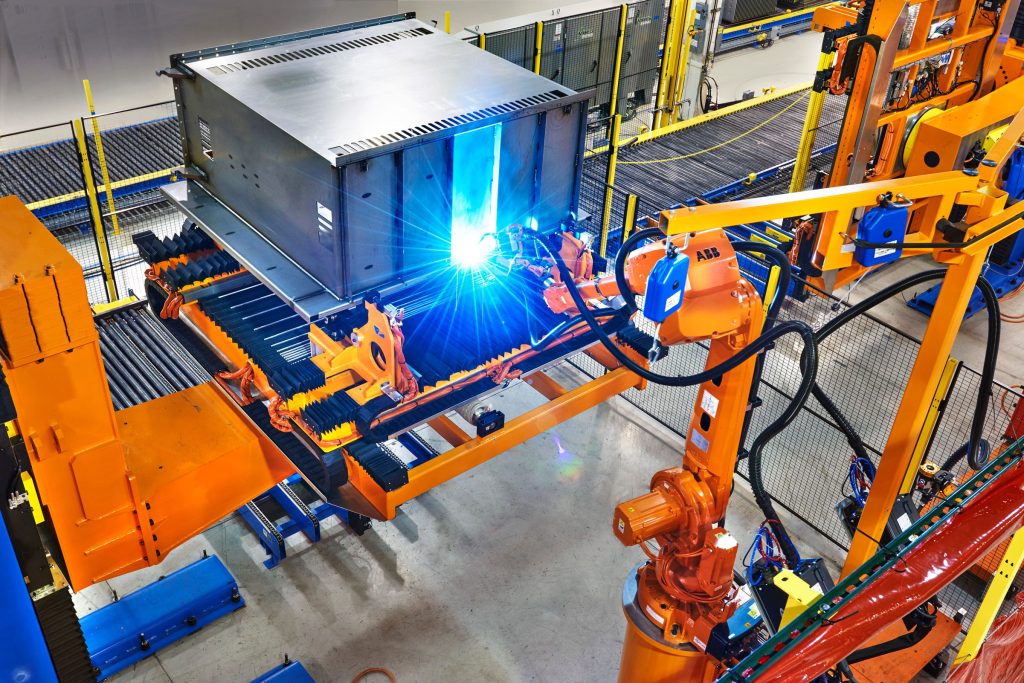
What is Multi-process Welding
Multi-process welding systems are advanced solutions that combine multiple welding processes into a single unit, offering versatility and efficiency for a wide range of welding tasks. These systems can seamlessly switch between processes such as MIG (Metal Inert Gas), TIG (Tungsten Inert Gas), and Stick welding, catering to different materials and thicknesses. MWES builds custom automation systems that can be combined with multi-process welding which allows for the mixture of ferrous and non-ferrous joining applications using the same equipment with automated tooling change-overs from one process to another. Multi-process automated welding systems maximize speed, output, accuracy, and a space-saving solution to confined work spaces.
Typically automated arc weld systems are split up into different process capabilities for different applications. Many robotic weld systems are designed to carry out more than one process concerning TIG and MIG welding, but meeting this condition doesn’t necessarily make those automated systems multi-process. While these combinations are possible and have their advantages, such as reduced workload, they tend to cause reductions in total output, arc stability, or other problems for at least one of the processes. A true multi-process system can execute all TIG and MIG weld processes with virtually no loss in performance standards between them.
Standard vs. Multi-Process Systems
With standard integrated weld systems, the welding automation machinery is designed to specialize in just one weld process. They tend to have certain features and functions that allow them to perform their particular process with great efficiency and user-friendliness. High-frequency ignition is a staple of today’s TIG weld systems. MIG weld systems operate using multiple different settings, allowing for a wide range of adaptability in terms of weld arcs and weld seam dimensions.
By contrast, a robotic multi-process system’s focus is on flexibility. The idea is that no matter what needs to be welded and no matter what automated processes need to be used, a multi-process system is well-equipped to handle the job. Multi-process tools are very adaptable and come in small sizes, making the overall systems much more portable than standard process ones. One necessary consequence of all of this flexibility is that compromises have to be accepted for certain features. For instance, an additional feature such as a high-frequency ignition ultimately increases the weight of the welding device and therefore lowers its overall portability.
By integrating various welding processes, multi-process welders facilitate uninterrupted workflow and maintain high-quality standards across different welding techniques. Whether it’s for a custom fabrication project or routine repairs, these systems provide the adaptability and performance required to meet the demands of modern welding operations. While multi-process welding is only a small portion of our welding integration capabilities, we can design any system to meet your needs from automating manual processes or upgrading current robotic systems. Contact us today and speak with one of our applications engineers to see how robotic automation can improve your process.
Building the future of manufacturing, together
World-class Automation