Robotic Rotor Bonder Assembly System
- Home
- Recent Projects
- Robotic Rotor Bonder Assembly System
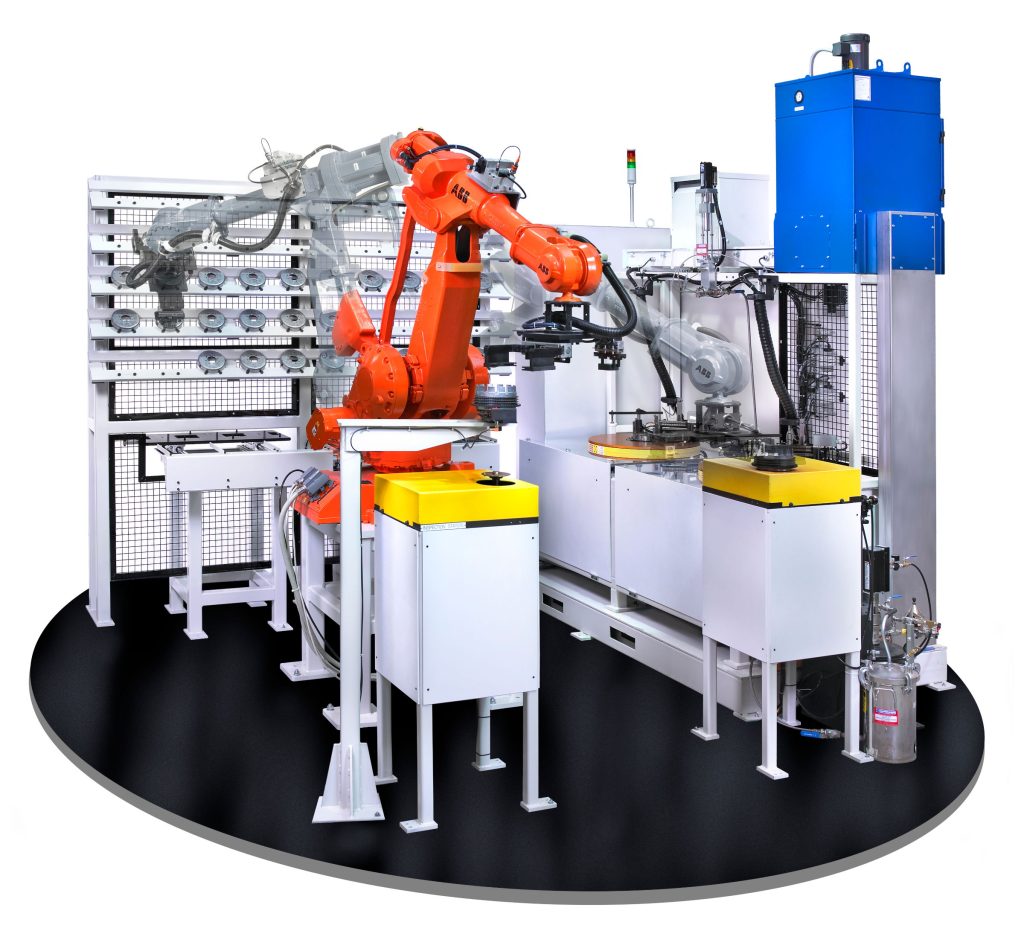
Project summary
MWES provided this firm with a fully automated robotic multi-station motorcycle rotor stator magnet bonding assembly system.
The Challenge
Transitioning an assembly line from one that is run with manual labor to a full robotic line is a process that requires extensive planning to not hinder the current manufacturing throughput. One technique is to integrate a singular robot cell to replace a very specific assembly process that is deemed too repetitive and strenuous for a worker while leaving the remaining assembly line unaltered. To accelerate and redistribute some of its workers, this firm contracted MWES to produce an automated solution that would accept machined rotor shells and stator magnets of multiple types and sizes and apply a two-part epoxy to the rotor shell and stator magnets using a positive displacement dispensing system.
The Solution
MWES provided our customer with a custom fully automated robotic assembly work cell. This automation system features a single tending robot that would transfer the assemblies to the necessary assembly stations. The system is capable of handling multiple types and sizes of rotor shells and stator magnets. The robot loads multiple stator magnets into the magazine and circular servo-controlled and force feedback magnet holding tooling indexes around where each magnet is ejected from the magazine and mounted on the magnet holding tooling.
Once all the magnets are placed, a glue applicator indexes around the entire assembly dispensing the first part of a two-part epoxy onto the surface of the magnets using a positive displacement dispensing system. The robot then picks the pre-epoxyed rotor shell and places it over the magnet mount at which point the stator magnets bond to the rotor shell. Once the assembly is complete the robot transfers the complete part to the part-curing storage rack.
Through the process, assemblies are inspected using a laser line generator and a Cognex Vision System. Additionally, completed parts are placed on a transfer station to be shear-tested and magnetized.
Impact to the Customer
The automation system that MWES provided this customer brought about many improvements. Those improvements consist of rotors being automatically assembled at a rate of one part every 50 seconds or less. Additionally, all magnet pressing is verified using individual axis load cell feedback, with all parts being 100% inspected and verified and bad parts automatically identified.
Midwest Engineered Systems has a wide range of experience in building custom automation systems. If you’re looking to improve your automation throughput, we have the knowledge and experience to make the project a success.
Contact us to learn how Midwest Engineered Systems can automate even your most complex and challenging operations today!
Innovation Through Automation
Client Details
An American motorcycle company from Milwaukee, WI.