Consumer Electronics Robotic Assembly System
- Home
- Recent Projects
- Consumer Electronics Robotic Assembly System
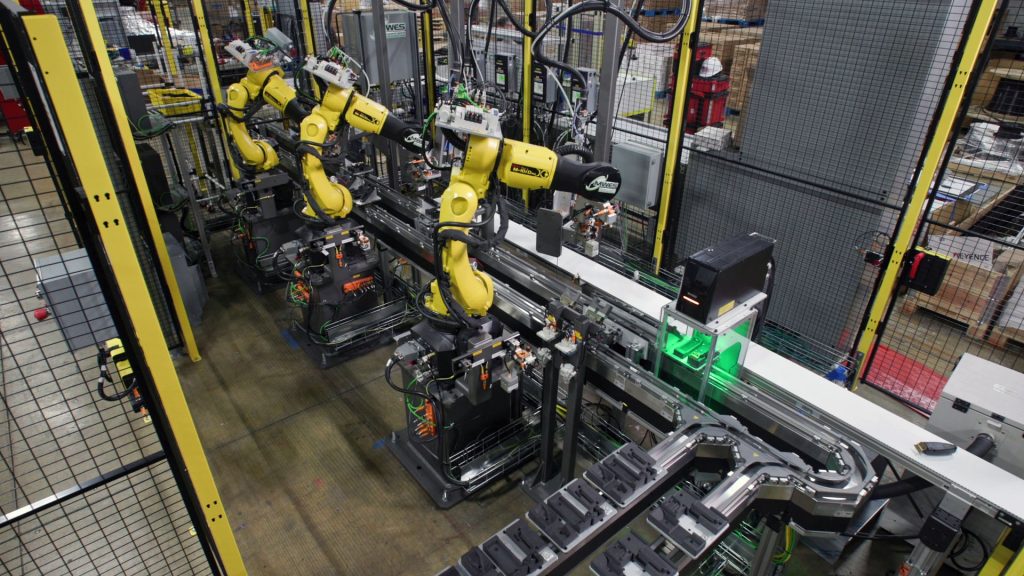
Project summary
MWES designed and integrated a robot assembly system for mass assembling electronic consumer-level hair trimmers.
The Challenge
Depending on the manual labor force for an assembly line poses a great risk in today’s world. With looming labor shortages to inconsistent work quality, more and more businesses are moving to robotic automation. For that reason, a company that specializes in manufacturing personal grooming products came to Midwest Engineered Systems looking to robotically automate the assembly of a range of different electric hair trimmer models.
The Solution
MWES designed and built a robotic automation system that utilized three robot stations and a conveyor to move the parts. Once the parts are assembled, they pass through an automated laser marking station that etches each part with the necessary information. The automation system requires three operators to manage; one operator to load the parts and two more at the end of the line for testing and packaging.
Before the start of the assembly, an operator scans the barcodes of the bins to verify that the correct components are being assembled. That operator then loads the plastic lower and upper housings, sled assembly, and blade assembly into the proper nest on the fixture. A vision camera will then verify the motor assembly is in the correct orientation before conveying it into the system.
At the first robot station, the robot feeds a fastener and screws it into the blade assembly twice. Next, the robot picks up the sled assembly and places it into the upper housing. It then picks up the lower housing and places it on top of the sled and upper housing. The assembled fixture then moves to the press station where the part is pressed together firmly. At the second robot station, a clamp holds the assembly while a screw gun mounted on the robot arm feeds a fastener and screws it into the assembly in four pre-defined locations.
The assembly moves to the final robot station, where the completed assembly is picked up by the robot and placed on the exit conveyor. As the part conveys, it passes through the laser marking station where it receives the required etchings. After the part has been marked, it moves to the packing station where two operators test and pack the product. If an assembly reject error is thrown within the automation process, the fixture returns to the first operator indicating the rejection on the HMI.
Impact to the Customer
The robotic automation system that MWES built for our customer could handle the assembly of three different models of trimmers. The production rate of this system was between 109 to 153 parts per hour, with the overall hourly performance based on the complexity of the different models.
Midwest Engineered Systems has a wide range of experience in building automation systems for consumer products manufacturing. If you’re looking to improve your assembly automation throughput, we have the knowledge and experience to make the project a success.
Contact us to learn how Midwest Engineered Systems can automate even your most complex and challenging operations today!
Innovation Through Automation
Client Details
A manufacturer of personal grooming products based in Wisconsin.