Cutlery Automated Packaging System
- Home
- Recent Projects
- Cutlery Automated Packaging System
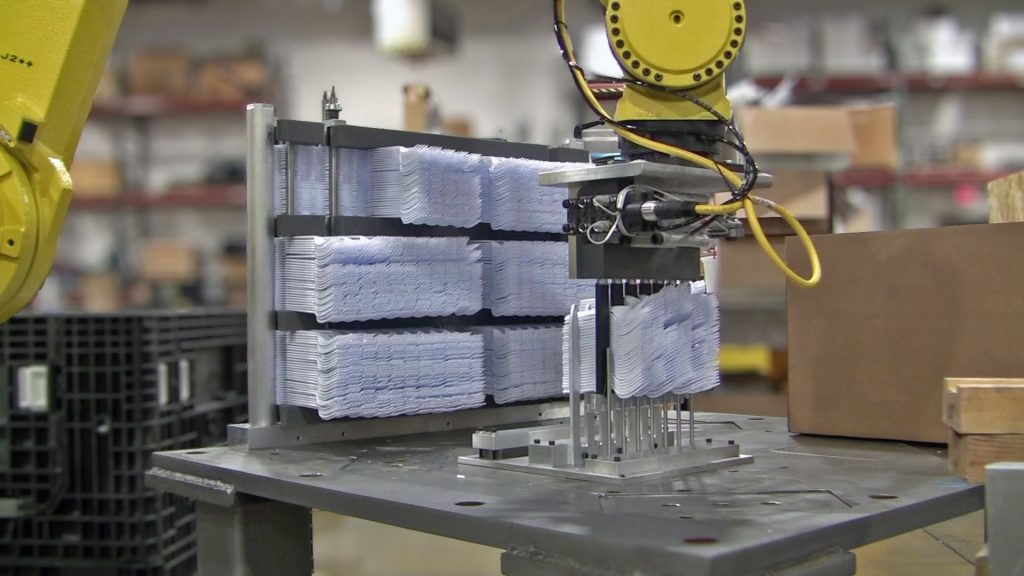
Project summary
MWES integrated an automated robotic handling and packaging system for plastic cutlery.
The Challenge
Handling hundreds of small injection molded plastic parts cleanly and efficiently is a difficult prospect for a manual labor operation. Typically when mass-produced injection molded parts are delivered they are attached to a spruce/tree as part of the molding process. Breaking the parts off from the tree is instrumental in the finishing process and when dealing with large quantities the removal needs to be performed in an organized fashion.
The Solution
The cutlery automated packaging system MWES provided out customer removes plastic forks or spoons from the dunnage and breaks the utensils from the spruce. Once free the system gets them into known stack quantities, transfers them to a centralized case packing system where they are case packed, and finally transferred out of the automated system to an operator for next step processing.
The parts arrive via a dunnage container on an infeed conveyor. A robot then picks a row of stacked parts out of the container and places them into the break-off nests. Another robot will then begin the break-off process using its end effector in quantities of 5-6 rows and a stack of 30 parts at a time. The robot then places the stacks into the tooling on the carrier pallet that is positioned in the load area. Once full the carrier exits the load area and a new empty carrier transfers into position. The dunnage robot removes the spacer bars and the empty spruce and places them in a scrap bin.
The full carriers move to one of two fill and leveling stations. Each row will measured with a laser distance sensor or other means to determine the height of the row which will indicate if the row has the correct number of parts. If the row happens to be short of parts, the robot picks parts from the overflow stack corrector carrier and places the shortage on the stack. Once the correct stack number has been verified and corrected for height, the carrier will transfer to the box pattern arrangement station.
A case is assembled to hold 600 pieces and 20 rows of 30 are pushed into the case. The case is then closed and sealed. The packed case then transfers out of the cell for the operator to unload.
Impact to the Customer
The automated packaging system MWES provided to our customer can handle 800 parts per minute. Utilizing robotics for this process, afforded this firm an efficient and fast packing process for hundreds of small components.
Midwest Engineered Systems has a wide range of experience in building material handling automation systems. If you’re looking to improve your material handling automation throughput, we have the knowledge and experience to make the project a success.
Contact us to learn how Midwest Engineered Systems can automate even your most complex and challenging operations today!
Innovation Through Automation
Client Details
One of the world’s largest manufacturers and distributors of paper products based in Atlanta, Georgia.