Flywheel Multi-Station Custom Press
- Home
- Recent Projects
- Flywheel Multi-Station Custom Press
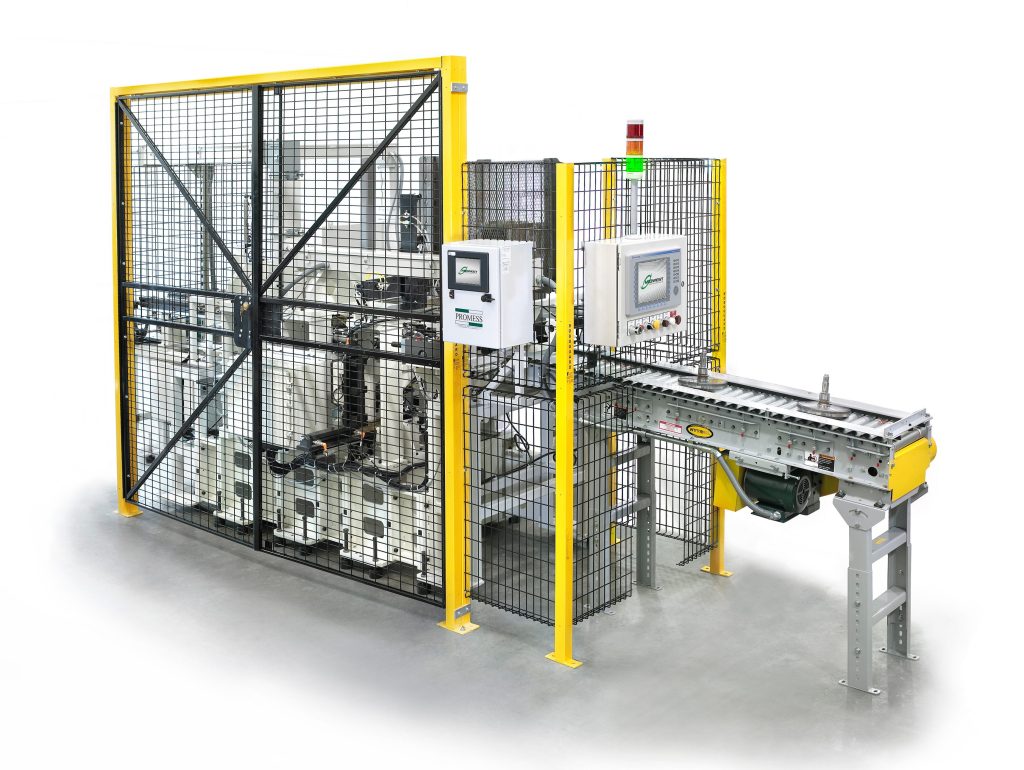
Project summary
MWES provided a firm with a fully automated turn-key multi-station press machine for the assembly of motorcycle flywheels.
The Challenge
With the importance of consistent throughput acquiring enough workers to staff a complex assembly line is a difficult task during labor shortages. Moreover, with the rising costs associated with manual labor, more manufacturers turn to automation as a solution to perform simpler tasks. For those reasons, this firm came to MWES looking to automate the assembly of motorcycle flywheels and was in search of a custom machine that would take in flywheels from a conveyor, orient and install a timing gear along with several other assembly operations.
The Solution
MWES designed a fully automated turn-key four-station press machine that would receive incoming flywheels directly from the parts washer via the infeed conveyor and orient the flywheel with a vision system. The machine would then press the sprocket and the bearing race into place. Lastly, it would insert the Lee plug and ring flip part, before exiting the system on the outfeed conveyor for further processing.
The flywheels enter the system’s staging area via the infeed conveyor from the part washing station. The flywheel indexes into the first station where a vision system locates the top dead center of the flywheel and orients the flywheel by the plunge oil cross-drilled holes. At the second station, the sprocket is pressed into place. Once in place the part indexes to the third station where the bearing race is pressed into the flywheel. At the fourth station, the snap ring and Lee plug arrive via a magazine and bowl feeder. Both parts are inserted into the flywheel while an automated impact hammer secures the Lee plug. Lastly, the completed assembly exits the machine on the outfeed conveyor.
Impact to the Customer
The single-operator turn-key machine MWES built for our customers gave them a fully-automated part pressing operation that is verified using Promess force load monitoring technology. This ultimately gave them consistent throughput and a cycle time of less than 50 seconds per part.
Midwest Engineered Systems has a wide range of experience in building custom turn-key automation systems. If you’re looking to improve your manufacturing throughput, we have the knowledge and experience to make the project a success.
Contact us to learn about how Midwest Engineered Systems can automate even your most complex and challenging operations today!
Innovation Through Automation
Client Details
An American motorcycle company from Milwaukee, WI.