Robotic Deburring & Polishing System
- Home
- Recent Projects
- Robotic Deburring & Polishing System
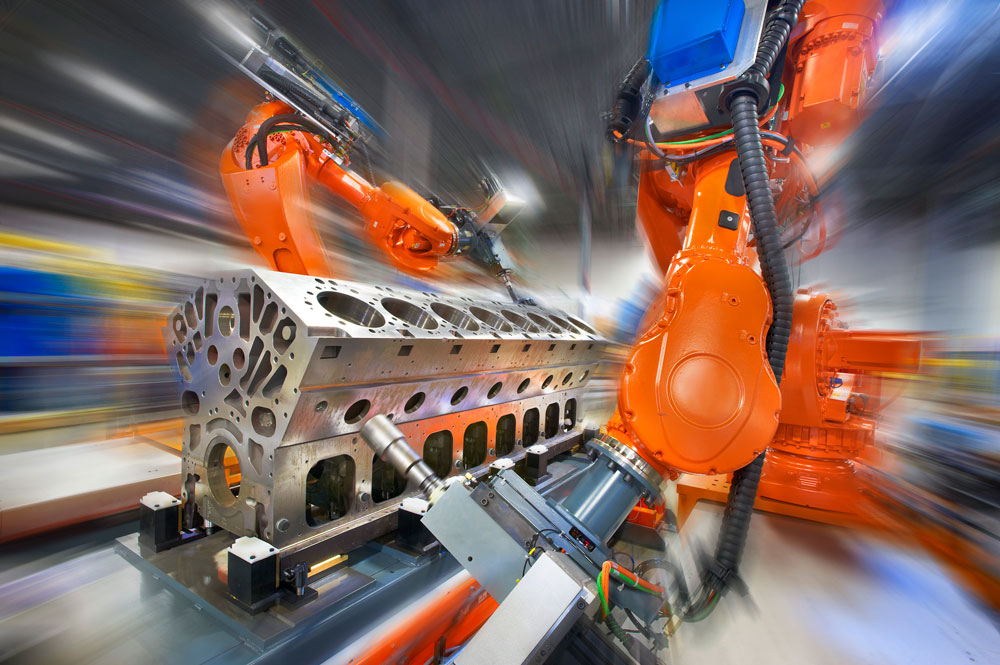
Project summary
MWES provided this firm with two robotically automated deburring systems for the production of large 3500 hp industrial engine blocks.
The Challenge
Performing any kind of post-processing work on large engine blocks requires an immense amount of labor not to mention the hazards. To keep up with production throughput, a manual operation such as that would require scores of workers to perform the work and consistency would be an issue. To improve their production throughput, a large construction equipment manufacturer sought to robotically automate the entire machining process with minimal operator intervention.
The Solution
MWES provided our customer with two automated engine block deburring systems where each system is equipped with two track-mounted robots to deburr and polish specific features of the engine blocks. In addition to the two robots, each system is equipped with automated conveyors, robot tool-changing stations, and deburring and polishing spindles.
After a full evaluation of the project’s challenges and goals, MWES provided the customer with a complete solution, which includes:
- Conveyor Systems – Automated conveyors are used to move the engine blocks into the fully enclosed robot deburring and polishing station, and then forward them to the inspection station.
- Two ABB Robots – Two track-mounted ABB robots work on either side of the engine block part in unison. The robots use touch sense, laser distance finding, and precision fixtures to locate and find the exact location of the part. These offsets are then sent to the robot to frameshift in preparation for deburring.
- High-Torque/Volume Deburring and Polishing Spindles – The 10 hp servo-controlled spindles on the robot provide extreme flexibility with torque and RPM for a large variety of brushes, carbide inserts, and ceramic abrasive tools.
- Tool Changing Station – The tool changing station is equipped with drawers and shelves to store multiple tools required for each of the deburr stations. The drawers were designed for an operator to replace tooling while the system was in operation. RFID tags present information to the robotic system to identify and compensate the tool based on the results of the tool setter. The robots move to this station to load the correct tool into its spindle before the deburring operation begins. The system also verifies break and wear characteristics after each operation before the tool is loaded back into the storage system.
Impact to the Customer
MWES provided our customer with an automation system that successfully increased their production to 14 to 16 finished engine blocks per day. Also, the machining center cycle time committed to deburring has been reduced from 4 hours to 20 minutes. Additionally, worker involvement was reduced from 8 hours of intense involvement down to 2 hours of operation and part inspection. Ultimately, moving to robotic automation increases the part quality and consistency and removes workers from a dangerous work environment.
Midwest Engineered Systems has a wide range of experience in building robot automation. If you’re looking to improve your manufacturing throughput, we have the knowledge and experience to make the project a success.
Contact us to learn about how Midwest Engineered Systems can automate even your most complex and challenging operations today!
Innovation Through Automation
Client Details
The world’s leading manufacturer of construction and mining equipment based in Deerfield, IL.