Automated Packaging Systems
- Home
- Industrial Automation Capabilities
- Assembly Automation
- Automated Packaging Systems
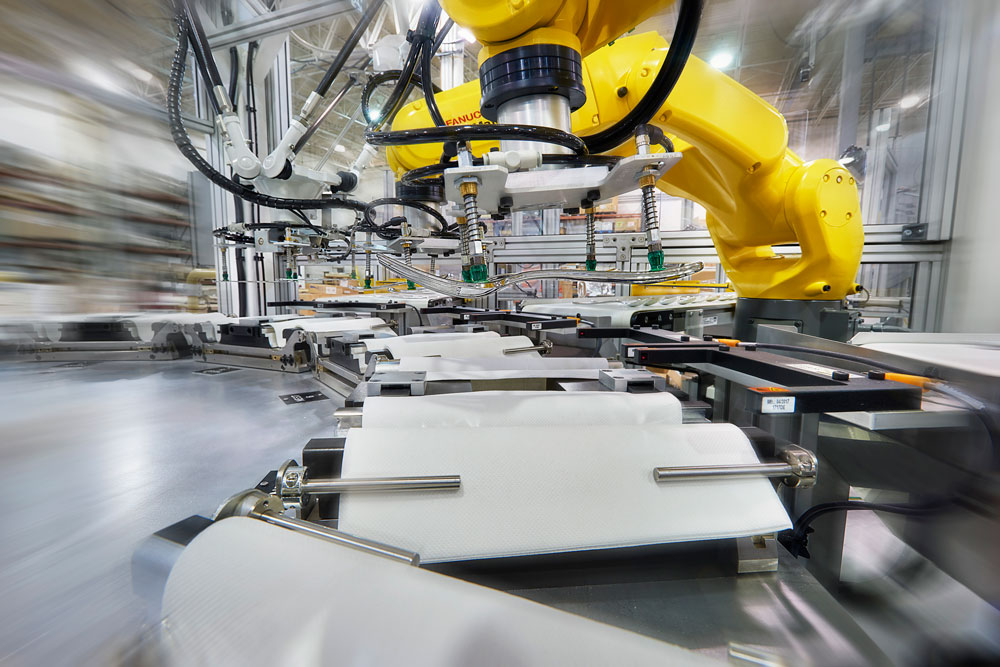
Transition Your Picking & Packaging Process to Robotic Automation
Speed and consistency are key to successful high-volume consumer packaged goods product production. Both of these metrics have everything to do with how difficult it is to find and retain a quality workforce that can keep up with the increasing production speeds that automated food processing machines can achieve.
Automated picking and packaging systems are becoming more popular in various industries, such as food and beverage, pharmaceuticals, fulfillment and logistics. The automation performs tasks such as picking items from shelves or containers, sorting parts into boxes, labeling and marking them, and finally sealing them for distribution. Packaging automation ensures that the packages are constructed, filled and delivered reliably and in line with the businesses standards.
Advantages of Automated Packaging
There are many advantages that product packaging systems bring to organizations when they integrate automated systems into their shipping operations. Among those benefits are:
- Improvements in both operational efficiency and greater labor savings
- Automated packaging systems can optimize the use of a facility’s space and simplify its layout designs
- With regular maintenance and upkeep, robotic automation systems can last for many years providing high reliability
- Well-designed automated product packaging systems can be reconfigured to package a wide assortment of products
- Some robotic automation systems can integrate new tools and processes to extend customized packaging requirements
Automated Packaging Processes
As a robotic systems integrator, MWES has extensive knowledge of engineering and integrating automated packaging systems that suit its customer’s needs. Case filling or de-casing machines can raise productivity and efficiency levels while ensuring the packaged products are handled and shipped consistently with minimal possibilities for error due to automation of the process.
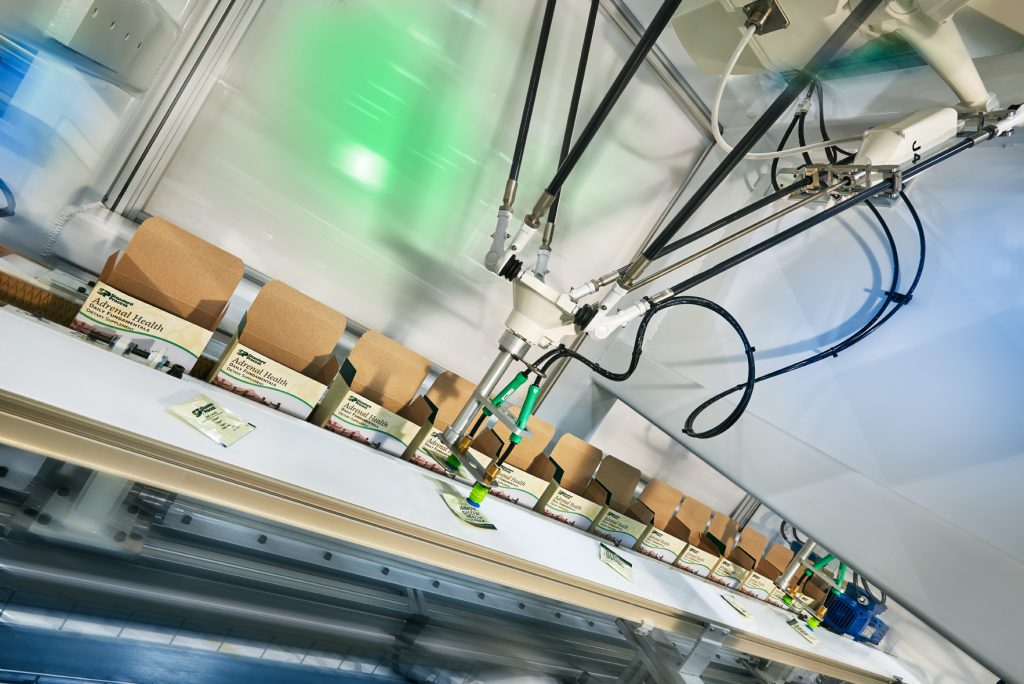
Case Filling Operations
In case packing or case-filling operations, a case-filling machine handles a group of products and packages them together in preparation for future shipping. Just as many products can be sent for delivery to another location, there are many ways of automating case packing products. Some general methods of case packing machines are palletizing, labeling, food processing, wrapping, handling, pharmaceutical processing and inspection machines.
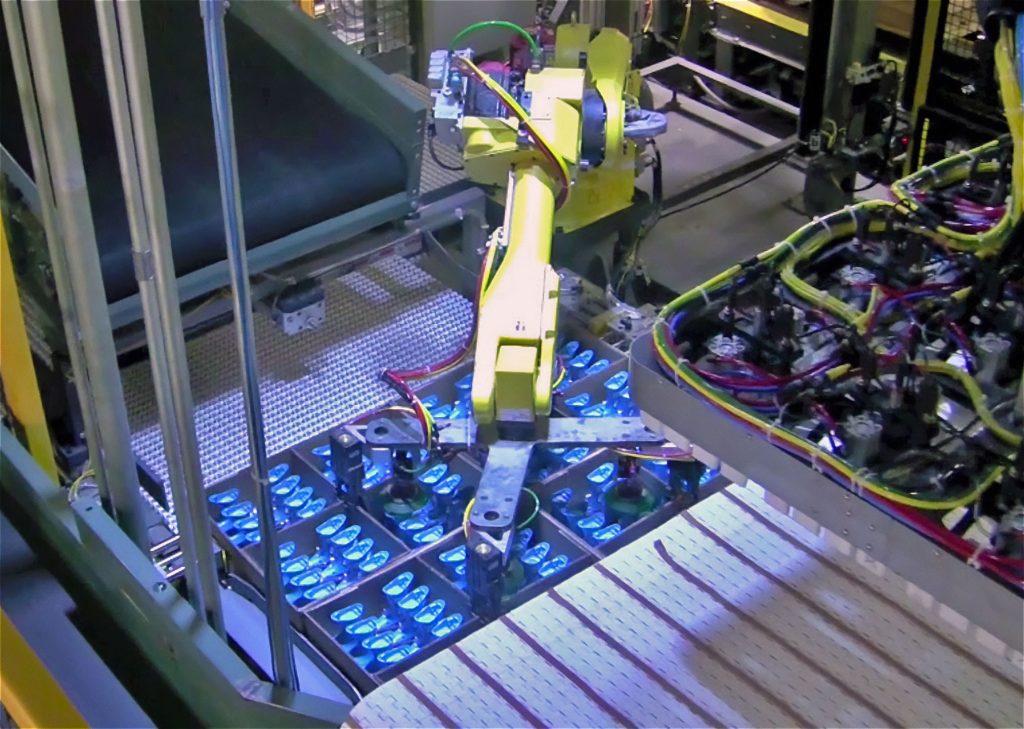
De-casing Operations
De-casers are machines that can open the lids and tops of glass and plastic bottles and other containers, often single-filing the containers to prepare them for reshipping processes. Some robotic automation machines can perform three actions: flap opening of cases, and de-casing, followed by single-filing of bottles. Automated de-casing machines can perform all of these actions consistently and continuously through rapid, entirely mechanical operations.
Some benefits of automated de-casing include the reduction of production costs as well as the elimination of the need for manual labor and associated liability costs. Other benefits include the safe handling of containers and consistent supply rates to filler operations. De-casing machines are especially sought after by manufacturers in the food and beverage industry who have high-volume bottle-handling demands.

Utilize Dynamic Vision Picking with Robotics for Speed & Efficiency
Until now, robotic packaging systems have not been the best choice for filling these needs due to the inconsistent shapes and orientations of bagged food products. That all changes with Midwest Engineered System’s blend of best-in-class robotic dynamic vision systems and high-speed, pick-place robotics. Now, these systems can almost flawlessly pack between 120-160 packages per minute.
Dynamic vision picking can be implemented using conveyor belts and vision systems. Parts pass through scanners and are presented to the robot without human interference. 3D vision systems locate the parts on a moving surface and direct the robot for proper gripping and positioning.
Dynamic vision picking can bring about the following production line improvements:
- Improved Ergonomics
- Reduce costly loss time due to injury or illness
- Less than a 2-year return on investment (ROI)
- Remove workers from the dangerous work environment
- Increase work productivity and quality
If your manual workforce is lagging in throughput, then contact us today. MWES can analyze your existing process and provide a robotic solution that can best suit your needs.
Building the future of manufacturing, together
World-class Automation