AS/RS Buffer Systems
- Home
- Industrial Automation Capabilities
- Material Handling Automation
- AS/RS Buffer Systems

The MWES AS/RS is the future of automated distribution for 100k sq.Ft. facilities & distribution centers
The MWES Automatic Storage and Retrieval System (AS/RS) buffer system provides efficiencies for the demands of a production environment. The benefits go beyond just being a storage system, it also becomes a highly efficient hub for managing a manufacturing process.
AS/RS buffer systems can operate independently or in conjunction with other automation systems, allowing the entire process to be fully automated. A typical system has some or all of the following features:
- AS/RS Buffer System – Strategically stores pallets in an automated racking system with the use of an automated shuttle
- Layer Picking Automation – Pick entire layers from an inbound pallet and transfer them to another pallet or conveyor
- Integration of AGVs/AMRs – Autonomously transport pallets or materials around the facility and into and out of the AS/RS system
- Pallet Quality Inspection Systems – Automated system that scans for defects in a pallet
- Data Handling and Sorting Software – Software that intelligently assigns and catalogs materials inside the AS/RS system
AGVs/AMRs can autonomously communicate with the AS/RS system when delivering material to the infeed conveyor. A layer-picking robot can pick materials off inbound pallets and redistribute them to other pallets. The pallet inspection system scans the pallet looking for defects such as protruding nails, cracks, and missing or broken boards. The data handling software strategically directs the materials to specified locations inside the AS/RS. Together these automation systems can save valuable manufacturing time, and reduce warehouse loss and production errors.
What the AS/RS Can Do For Your Process
The MWES AS/RS Buffer system allows for the collation and management of asynchronous production processes. Inventory rooms can produce product-specific kitting on a schedule that’s more conducive to their efficiency and load them into the AS/RS system when done.
These kits can be retrieved with the rest of the components needed for a specific production run. Allowing the AS/RS system to manage these kits’ locations and when they’re called, can reduce routing confusion on the floor when building products that have high part commonalities.
Our production-focused storage systems are designed from the start to fit into legacy production facilities. With its scale and operation, our AS/RS system can change how you think about not just warehousing, but production processes – and increase your throughput along the way.
The AS/RS system can be set up for operating on multiple in-and-out materials, not just consumable items. This makes it quite useful for storing fixtures and tooling for jobs in the same place as the materials and WIP needed to complete the production process.
Work in progress can be re-admitted to the system and re-combined with different tooling and fixtures necessary for the next step in the production process. The combined group would then be ready for the next process. Having virtually every aspect necessary to complete a job in the same location and easily retrievable, allows even greater efficiencies beyond saving floor space.
AS/RS for the Production Environment
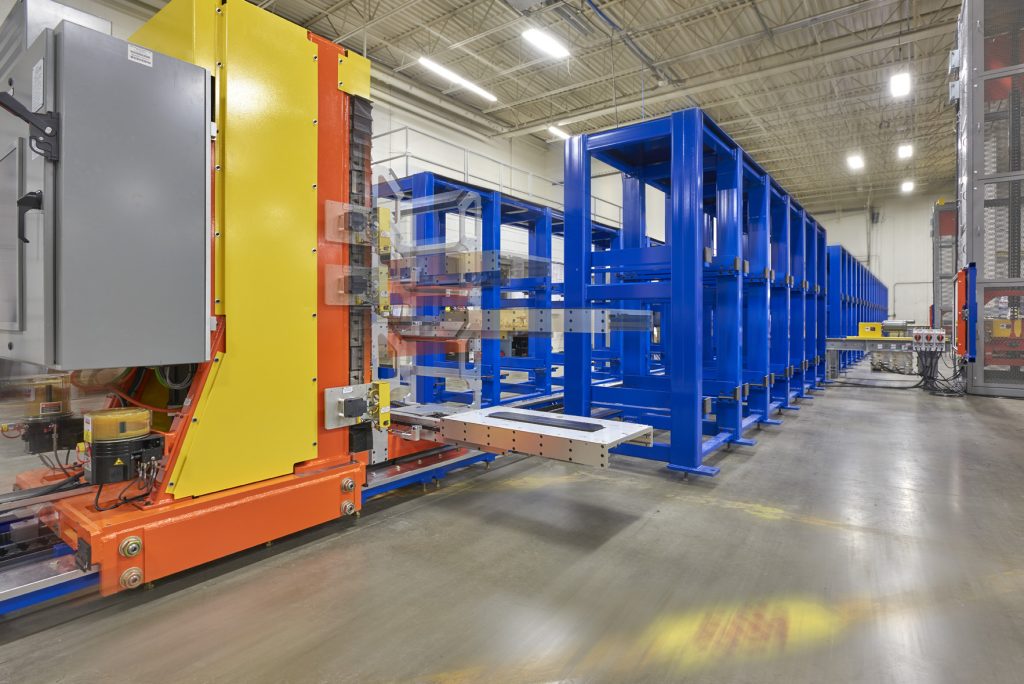
For the longest time, the benefits of AS/RS buffer systems have been in the sole domain of large warehousing applications, but there’s a significant benefit to be had using AS/RS systems in production environments if they could be designed with manufacturing needs in mind. MWES has done just that!
Our production-focused storage systems are designed from the start to fit into legacy production facilities. With its scale and operation, our AS/RS system can change how you think about not just warehousing but production processes – and increase your throughput along the way.
Store tooling & jigs more efficiently
No more hunting around the shop – or worse searching the stockyard – for occasionally used tooling. MWES’s automated storage and retrieval system can organize seldom-used but necessary jigs and fixtures in a system that makes it quick to locate and access when needed while freeing up valuable floor space when not. Square footage is highly sought after but rarely is the cubic footage of a shop considered fully. Our system is designed to go high and maximize the utility of your facility’s ceiling heights and store things in a high-density format that stacks inventory vertically, maximizing floor space. All this equates to more efficient production changeovers as fixtures are stored in a known and easy-to-retrieve area rather than relying on operator notes and memories. It also makes sure the jigs and tooling are placed away from the potential for damage by any manner of incidents, reducing potential lost time and cost incurred from fixing potential issues.
Maximize Your Floor Space
Store up rather than out. Our system is designed to be built within existing buildings. With its ability to store things easily up to 30ft in the air, the potential to double or triple the current storage capacity without having to add on or store off-site is certainly within reach. Many of today’s shop floors are high-density, making it difficult to get forklifts into places where tooling or materials are stored without getting uncomfortably close to critical production machinery. Add humans at the wheel, and the operation can become even more hair-raising to floor management. With our purpose-designed retrieval system, accessing materials stored at higher levels doesn’t require maneuvering large forklifts for challenging picks or relying on human operators to perform these functions. The system’s compact size also reduces through-way congestion, as it doesn’t rely on maneuvering large masses like fork truck bodies to pick from the highest locations. Instead, it uses its compact shuttle system to store and retrieve materials. That extra floor space made available with the AS/RS system opens up opportunities for expanding production space or streamlining workflows with more area for positioning equipment.
Manage Your Production's Work-in-Progress
Reduce changeover time and increase production schedule efficiencies with efficient storage and retrieval abilities. Some production steps take longer than others. That disparity may manifest from shorter turn times on one machine while parts stack up waiting for longer processes on other machines. MWES’s production AS/RS system can act as a production buffer by easily storing and retrieving WIP stock. This temporary storage ability opens up higher-speed production machines for other jobs while slower processes work through backlogs, as well as keeping production areas cluttered and unorganized. Being able to easily buffer stalled projects into the MWES storage system opens up floor space and machine time and also reduces confusion. Using an AS/RS buffer system also frees resources to operate on other jobs without being bogged down by waiting for back-ordered materials, increasing overall production efficiency.
Clear out the receiving department & stage upcoming jobs
Sometimes materials for future jobs get stuck in Receiving or get lost or damaged. An AS/RS system can organize these materials in a manner that makes them quick and easy to retrieve in an organized fashion when the work begins. With the system’s ability to store vertically, incoming materials can be cataloged and stored in the AS/RS racking out of the way until needed. A production-supporting automated storage and retrieval buffer system could also be used to prepare incoming jobs by staging components and tooling before work can begin. Having this organizational ability lends itself to more easily scheduling when both materials and tooling are delivered to the floor and when things should be returned. An automated AS/RS buffer system also can help keep track of jobs that have all of their materials ready and that do not. These abilities make it easier for job schedulers and buyers by providing needed knowledge and flexibility that leads to greater production efficiency.
Automated Enhanced Workflow with Performance
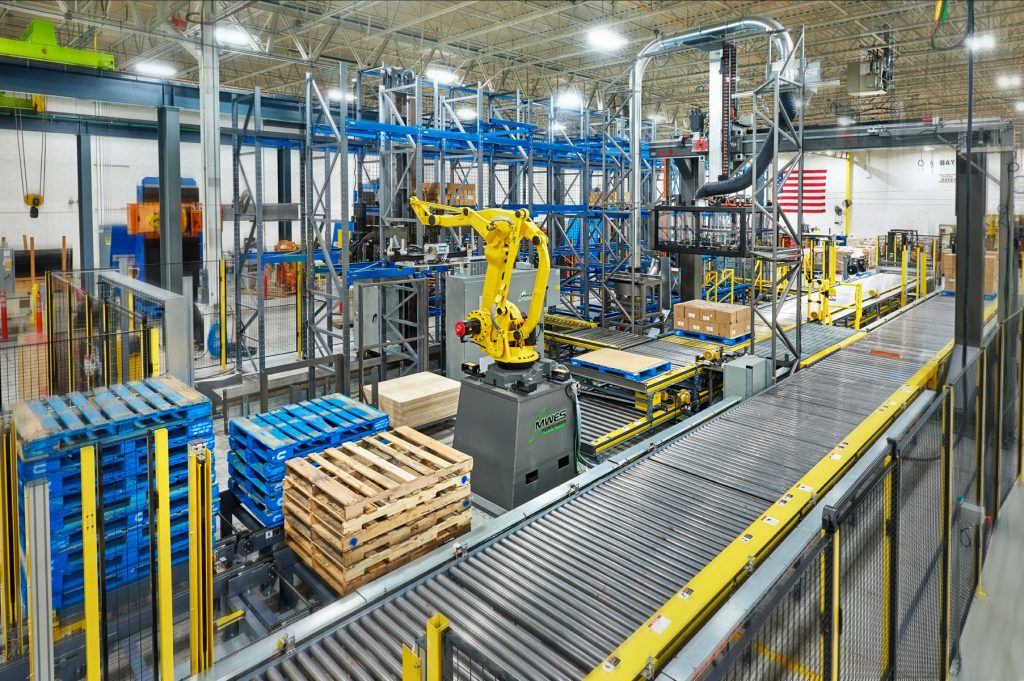
The benefits of the MWES AS/RS buffer system do not stop with what happens on the production floor. Material arrival and removal data can be harvested for production performance analysis. It allows a production manager the ability to see beyond individual machine performance and understand the logistics that feed into a machine or process performance. This accountability can be monitored to determine production efficiencies and identify bottlenecks hidden between processes.
Adding remote signaling capabilities, manufacturing stages can not only alert the system when a process is nearing completion, but they can also request the materials for the next job – all without leaving the cell. The AS/RS system can retrieve materials and tools as the completed work is returned to storage and return to stock the recently arrived finished parts without needing human help. This ability helps keep production efficiency high by streamlining the logistics and reducing potential downtime waiting for parts.
Taking advantage of all these aspects makes the MWES AS/RS buffer system much more of a trusted workflow manager that has the potential to better see the entire manufacturing process as a singular system, not just a collection of unconnected machines and resources. The system’s benefits provide the opportunity for a forward-thinking production facility to move to the next level of efficiency and productivity.
The Key Features of the AS/RS Buffer System
Floor space is a hot commodity in today’s production settings. It also can be one of the biggest determinants of how productive a facility can be. The movement of materials and the storage of components and fixtures can be a puzzle that easily soaks up that valuable square footage if not solved properly.
But getting more control over your materials and inventory doesn’t have to be difficult. MWES has worked hard to develop a system that’s as easy to install and upgrade as it is to operate. Below, we’ve broken out some of the more innovative aspects of the system.
Ease of Operation
MWES storage systems can be operated from a touch panel on the shop floor. With a minimum of training, the easy-to-use screen design allows workers to quickly call for materials or tooling by touching through the interface. Through the same panel, workers can also add new items to the inventory and connect the materials to current or new jobs.
Safe to Use
Our system uses OSHA-approved light curtain technology to stop potentially dangerous situations from happening. When a worker begins to move close enough to the machine, it automatically slows its operation. If the worker continues to breach the area, the machine will immediately stop its operation and turn on warning lights. The system will not move until the workers have removed themselves to a safe distance from the system. This helps ensure the workforce stays safe throughout its operation, even when they haven’t been specifically trained on the hardware.
Production Environment Friendly
Sometimes there just isn’t enough room inside production facilities to store materials, tooling, or work in progress. Conventional automated storage and retrieval systems would require the acquisition of another building to house the system – one purpose-built just for the storage system. The requirements tend to drive the integration of AS/RS systems to sums that make it prohibitive for many firms whose automated storage needs aren’t as tied to high storage volumes or pick speed.
Storage capacity can be added as needs arise
Want to start with a two-shelf system but would like the option to add another level later on? Started with 20 linear feet of shelving but now needs to double that capacity. Thinking of putting a second system in the outbuilding but want both systems to integrate? All of these options are what the MWES AS/RS system was designed to provide right from the start. The MWES production AS/RS system was developed to make it easy to increase its capabilities – within pre-existing production facilities. Not only is it easy to start with a smaller system to prove its benefits, but it allows expansion without tearing the system out to put a new one in.
No specialized containers or pallets required
Most large automated storage and retrieval systems work from custom-sized cartons and bins to make the system work. Not only is there investment in the structure and the kinetics of the system, but there’s also quite a bit of investment that goes into these specialized containers. Not so with the MWES AS/RS system. We’ve built our system to operate on standard pallets used throughout the world to ship and move products and materials. If it works with your current forklift, it should work with our storage system. And for large items, they may not even need to be placed on a pallet.
The Components of the AS/RS Buffer System
The AS/RS system comprises four major components: the pallet racking, the shuttle, the infeed/outfeed and the control system. The AS/RS Buffer System is designed to fit within existing production facilities using a modular, scalable approach that not only allows installation flexibility, it also provides the ability to be easily expanded in the future.
The Pallet Racking
The Infeed & Outfeed
The Shuttle
The Control System
If your business is looking to free up floor space in your facility then look no further than an AS/RS buffer system. MWES has extensive experience integrating automation systems including Automatic Storage and Retrieval Systems. Contact us today and speak with one of our application engineers and see how we can help your process.
Building the future of manufacturing, together
World-class Automation