Robotic Palletizing & Depalletizing
- Home
- Industrial Automation Capabilities
- Material Handling Automation
- Robotic Palletizing & Depalletizing
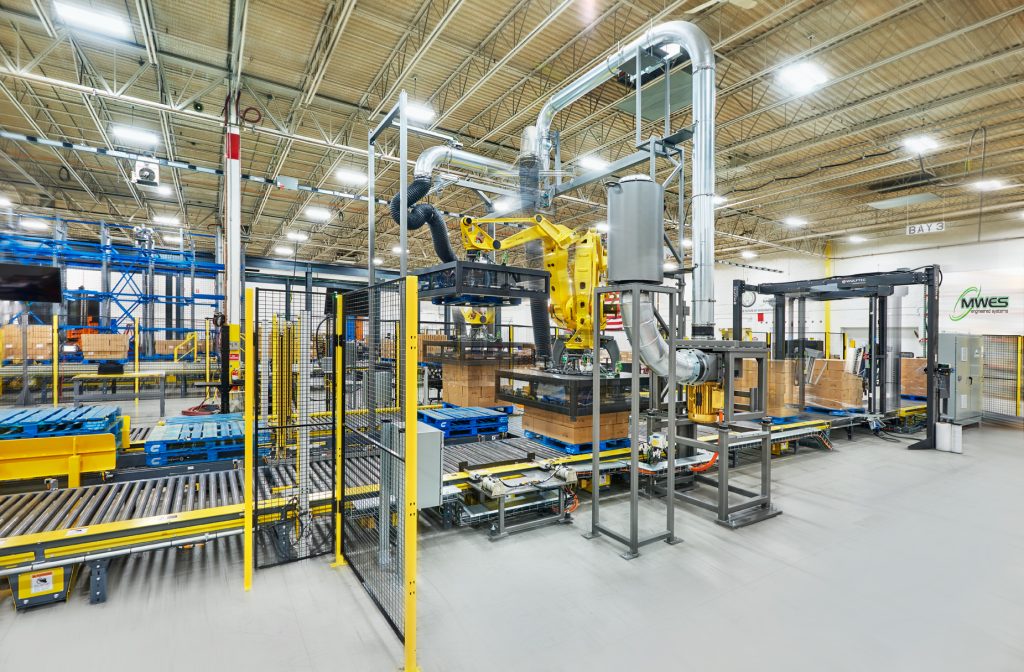
Keep Throughput Consistent with Robotic Palletizing & Depalletizing Solutions
MWES specializes in integrating custom and standard palletizing and depalletizing systems. We utilize highly efficient, multi-zoned vacuum grippers and advanced servo-mechanical grippers to handle various products and capacities. We can configure the automation specifically for your unique plant layout and production needs.
Automated palletizing involves robots loading corrugated cartons or other industrial objects onto a pallet according to specific directives. Automated depalletizing is the corresponding process of unloading a palletized object off the pallet in the opposite pattern. Automated palletizing solutions improve organizational efficiency and profitability. As robots do not need rest or breaks, they offer more flexible options and can continue production for much longer periods with minimal periodic maintenance.
Why Switch to Robotic Palletizing Systems?
While robotic palletizers are not a new concept, they are a proven technology used by facilities around the globe and bring several benefits for the firms that use them. At Midwest Engineered Systems, we’ve produced automated palletizing solutions for a variety of industries, both custom and our standard robotic palletizing systems. Regardless of a firm’s final product, we’ve discovered robotic palletizing offers a common set of gains for every industry.
Palletizing With Consistency and Quality
A large part of the robotic palletizer’s capability is in its programming – and goes well beyond just stacking boxes. Well-built robotic systems are tuned to the exacting specifications of the products being moved. The tooling that holds the packaging is set to control the item to its planned destination with the correct amount of force to ensure no drops as well as to make sure to avert damage to the packaging.
These robotic systems can also be programmed to perform a variety of palletizing patterns which can be assigned to certain products or certain customers and changed on the fly. More complex systems can even be programmed to stack different product SKUs on the same pallet.
Once dialed in, robotic palletizing systems can perform these processes tirelessly, every shift, giving the firm a reliable set of performance metrics to more adequately forecast future operations.
Reliable Speed While Getting Workers Out of Danger
Today’s robotic palletizers can usually meet – and sometimes exceed – the speed manual palletizers can achieve and they can do it consistently across all shifts.
Reassigning humans to more meaningful tasks through the adaptation of robotic palletizers provides many benefits to a firm. The two largest of which are the ability to more reliably hit packaging performance metrics and reduce potential injuries and employee burnout on high repetition operations.
For production operations that are highly automated before products arrive to be packaged, extending that automation to the end-of-line operations allows the firm to sidestep bottlenecks that could slow overall production. With automation at the product palletizing stage, a highly automated firm can more easily tune the packaging aspect to meet the demands of production without having to factor in the discontinuities of maintaining a human workforce at high-performance levels.
Speaking of human palletizers, the opportunity for repetitive strain injuries or long-term issues from daily heavy lifting activities is another common driver for adopting robotic palletizer systems. The near-term issues with making sure burnout doesn’t consume valuable workers or produce nagging injuries that slow throughput may pale in comparison to the long-term costs of healthcare issues and even legal claims. With automation, these issues are essentially mitigated.
Drop-in Robotic Palletizing with the MWES Standard Cell: A small footprint & a quick install
MWES’ standard robotic palletizing systems do not require large amounts of space or long periods to get up to production speeds. Our systems are compactly designed to be installed in pre-existing production environments. In some instances, the robotic systems take up less space than the manual processes they’re replacing.
Robotic palletizers are not the highly custom robotic operations of the past. Today’s machines do not require large amounts of space or long periods to get up to production speeds. Many systems are compactly designed to be installed in pre-existing production operations. Many times, these standard drop-in systems take up less space than the manual processes they’re replacing.
The MWES standard system is completely built and tested in our facility with our customer’s real products. This ensures the system will work perfectly when installed at the customer’s plant. It also allows us to dial in the settings and configurations without having to disrupt current production operations, as well as to guarantee performance metrics are met. The customer is invited to our facility to see it run themselves, before readying their facilities for new equipment.
The Types of Robotic Palletizing Processes
There are three main types of robotic palletizing and depalletizing systems each has its benefits and limitations. MWES has extensive experience integrating all three types.
Inline Palletizing
Full Layer Palletizing & Depalletizing
Mixed Case size Palletizing
Midwest Engineered Systems has integrated robotic palletizing systems for a wide berth of industries. From food and beverage to medical products MWES has the experience to make your project a success. Contact us today and speak with one of our application engineers to start the process of improving your palletizing throughput.
Building the future of manufacturing, together
World-class Automation