Collaborative Robots Revolutionizing Food Manufacturing
Collaborative robots (cobots) are transforming the food industry by offering innovative solutions to labor shortages, production flexibility, and safety challenges. As the fastest-growing segment of industrial robotics, cobots are designed to work alongside humans, boosting efficiency while maintaining safe and productive workflows.
At Midwest Engineered Systems (MWES), we specialize in integrating collaborative robots into food processing and packaging operations, delivering custom automation solutions tailored to your needs.
Benefits of Collaborative Robots in Food Manufacturing
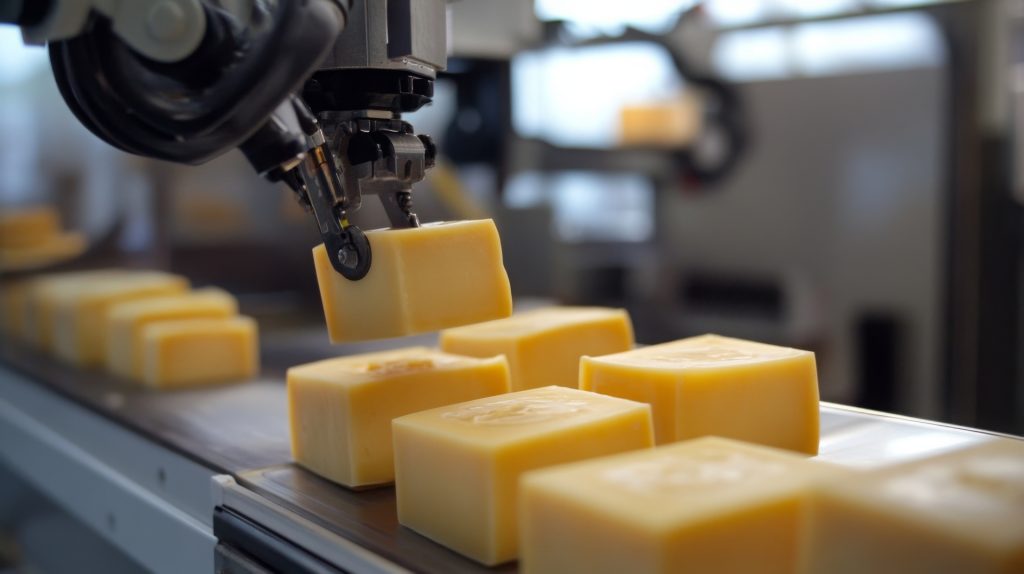
Flexible and Compact Design
Cobots eliminate the need for bulky guarding and can operate in compact spaces, making them ideal for food plants with limited floor space.
- Portability: Cobots can easily be moved across production lines to maximize ROI and adapt to changing demands.
- Food Safety Advantage: Without physical guards, there are fewer hidden spaces for pathogens to grow, simplifying cleaning and sanitation processes.
Simplified Programming and Operation
With intuitive tablet interfaces and hand-guided programming, cobots are user-friendly and require minimal training.
- Operators can quickly set up tasks by guiding the robotic arm and programming waypoints on the interface.
- This ease of use reduces downtime and accelerates deployment.
Considerations for Cobot Integration in Food Manufacturing
The advantages of collaboration do come with some strings attached. Because cobots are designed to work near humans they must be limited to ensure that the technology stays safe. In general, cobots operate at slower speeds, have less reach, and are limited in the amount of weight they can handle compared to traditional robots. While simple movements are easy to program with the standard user interface, more complex applications may require specialized programming from third parties.
Just because the robotic arm can work safely in a collaborative environment does not mean that it can be deployed in every application. The end-of-arm tool needs to be safe – free of pinch points or actions that can injure a person. Using a cobot for meat trimming, cutting blocks of cheese, or portioning cakes can injure personnel despite the sensors built into the robotic arms.
Balancing Safety, Payload, and Reach
- Speed and Payload Limits: Cobots typically operate slower and carry lighter payloads compared to traditional robots. Heavier loads or extended reach may further reduce speed.
- Dynamic Safety Features: Adding area scanners and sensors can enhance safety by dynamically adjusting speed, but this may increase the cost and operating footprint of the system.
The weight of the product and the range of motion for the arm are factors when considering cobot performance. Often, to handle heavier loads or operate close to the reach limits of the arm the speed of the arm must be reduced. So, it is fairly common that even though a cobot may be rated to handle a certain payload at a certain reach, it may not be able to do so at full speed.
Application-Specific Safety Measures
Cobots must have safe end-of-arm tooling (EOAT). Applications like meat trimming or portioning foods with sharp tools may require additional safety measures, as even the most advanced sensors cannot eliminate all risks.
Sanitation Challenges in Food Production
In the food industry, cleaning and sanitation are critical. Many standard collaborative robots are not built to withstand wet environments or exposure to harsh cleaning agents.
- Material Considerations: Standard cobots with aluminum and plastic components may degrade over time with repeated cleaning.
- Food-Grade Cobots: Purpose-built food-grade cobots feature enclosed designs, internal cable routing, and water-resistant materials for high-pressure washdowns and chemical resistance.
Pro Tip: Share your food safety and sanitization protocols with the equipment provider to ensure the selected cobot meets your cleaning and durability requirements.
Is a Collaborative Robot Right for Your Facility?
Cobots can significantly enhance efficiency, productivity, and safety in food manufacturing when deployed correctly. However, their success depends on aligning the technology with your specific operational requirements.
- Work with Experts: Partner with experienced integrators like MWES to ensure your cobot system is designed for your unique needs.
- Tailored Solutions: At MWES, we prioritize providing the right automation solution, whether that’s a collaborative robot or another form of advanced automation.
Like all forms of technology and automation, collaborative robots can be deployed wisely or poorly. When considering if the technology is right for you make sure you work with integrators who have the experience, knowledge, and resources to support a system that works best for what you need.
Talk to MWES About Cobot Solutions
MWES offers tailored automation solutions for food manufacturers, including collaborative robots and other advanced systems. Our goal is to deliver innovative, effective tools that help your business thrive in a competitive market.
Contact us today to explore how cobots can optimize your operations, improve efficiency, and adapt to the ever-changing demands of the food industry.