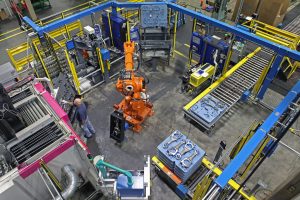
Global manufacturing stands on the brink of a transformative leap – the shift from a volatile manual labor workforce to a fully automated robotic process. This transition brings about increased efficiency, productivity and long-term cost savings. However, it does carry with it a host of risks that need to be carefully managed to ensure a smooth and successful integration. The challenges can be intimidating, but with careful planning and execution, they can be overcome to realize the full potential of automation in production operations.
Steps to a Smooth Transition to Robotics
Employee Engagement and Redeployment
One of the biggest fears for employees is the potential for job losses. As robots become more sophisticated and capable, they can take on tasks that humans once performed. This can lead to the displacement of workers, particularly in industries that are heavily reliant on manual labor. It is important to communicate and provide transparency with employees and stakeholders about the transition to a robotic workforce and the reasons behind it.
Invest in training your workers by equipping them with the skills to operate and maintain new robotic systems. This not only minimizes resistance to change but also enhances job satisfaction and retention. Redeploy talent and identify new roles for displaced workers, such as system operation, maintenance or programming. This helps retain institutional knowledge and fosters a culture of adaptability.
Strategic Planning and Phased Implementation
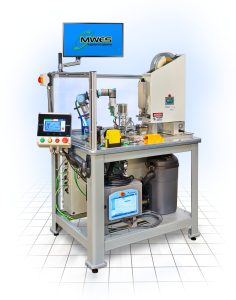
When working with a systems integrator, documenting a comprehensive plan with a detailed roadmap that outlines each step of the transition process is crucial. This plan should include timelines, budget considerations and expected outcomes as well as a risk assessment to identify potential challenges and solutions. Also, adopting a phased approach by gradually integrating automation allows for adjustments and learning at each stage. Start with automating simple, repetitive tasks and scale up as confidence and capability grow. Starting with a small automated work cell or machine can provide insight into the scalability of the process and ensure that the automation solutions can scale with your manufacturing demands.
Operational Continuity and Minimizing Downtime
There is the risk of disruption to the existing manufacturing process. Introducing new robots and automation systems can be a complex and lengthy process to work out with an automation integrator. So, it is important to carefully plan out and implement the transition to minimize disruption to your current production line. Establishing a pilot program to test the automation process in a controlled environment to work out any kinks before full-scale implementation is a way to mitigate this.
Integration with Existing Technology and Procedures
Efficient assembly lines form the backbone of any manufacturing operation. However, traditional labor methods often face limitations such as slower cycle times, high labor costs and human errors. Integrating robotic automation into an existing manufacturing line is a strategic move that can significantly enhance efficiency, quality and productivity. Creating clear documentation and a sequence of operations for the existing operation will help an automation integrator understand the process. An experienced system integrator can seamlessly introduce new automation into the process with software and hardware that can interface with existing systems and operations.
Test and Refine the Automation Process
Before fully implementing robotic automation, it is important that the integrator thoroughly tests the system and makes any necessary refinements to ensure that it functions as intended. This can help in identifying any potential issues or bottlenecks and resolving them before they become problematic on a live production line. Once robotic automation has been implemented, it is important to continuously monitor and evaluate its performance to ensure that it is delivering the expected benefits. This can involve tracking key metrics, gathering feedback from the operators and making adjustments as needed to optimize the automation process.
By addressing these areas, businesses can reduce the risks associated with the transition to robotic automation and set the stage for a future where human ingenuity and robotic precision create a powerhouse of productivity. The journey may be complex, but the destination—a smarter, more efficient and more productive manufacturing environment—is well worth the effort and Midwest Engineered Systems is here to guide you.
Midwest Engineered Systems has three decades of experience building automated robot cells, developing custom solutions and integrating robotics into full production lines. We have provided automation systems to a wide range of industries from consumer goods assembly and handling to automating medical lab processes to industrial heavy equipment manufacturing.
Contact us today and speak with one of our applications engineers to see how MWES can guide your business to a more profitable future.