Flexible Automation Systems
- Home
- Industrial Automation Capabilities
- Assembly Automation
- Flexible Automation Systems
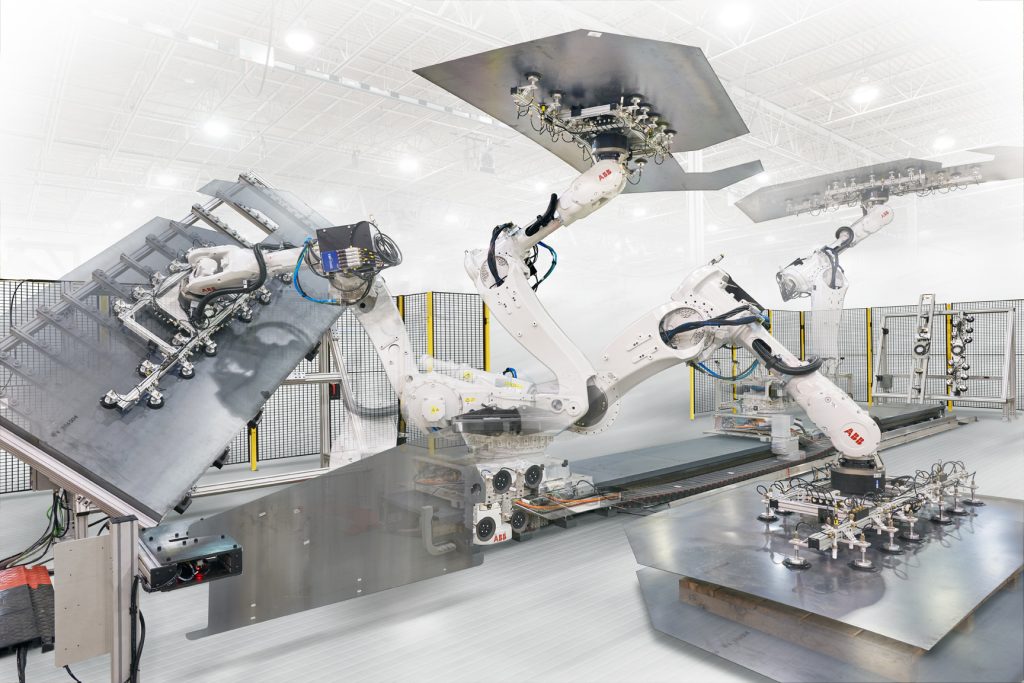
Get Process Adaptability with Flexible Automation
Flexible automation systems are highly adaptable systems with sophisticated machine input and controls. Commands are created and entered by the operators using computer code or through other Human Machine Interfaces (HMIs). These computer instructions are high-level, starting low-level changes automatically and identifying various automation processes and their system locations. In flexible automation systems, multiple machine tools can be connected to a sophisticated material handling system typically through robotic automation. Each aspect of the production and material-handling system is controlled by a central computer system.
In the flexible automation system process, computers controlled by human operators issue instructions to machine tools. These computer-generated instructions begin the processes of loading and unloading the machine tools that are necessary for performing the processes necessary to manufacture the desired parts. After the production automation system finishes its final manufacturing stage, the resulting products are moved to the next machine in the sequence automatically.
Flexible automation systems are capable of processing multiple product types at the same time. During any production run, each of the system’s machines could potentially be processing a different product or part type. As system requirements and demands change, the flexible automation system has the adaptability to handle them. This factory automation system can manage changes to production schedules, demand patterns and product mix changes. So long as a newly introduced product style fits within the kinds of products that a flexible automation system is configured to process, new part versions could easily be introduced into the production system.
Flexible automation systems traditionally have the following components:
- Part processing machines – Computer numerical control (CNC) machine tools are used to carry out some portion of the machining processes. Inspection stations and other automated workstations may be used in conjunction with these processing machines.
- Machine tending robots – Utilizing a robot to tend a machine such as a press, roller or part assembly operations. Robots can perform large jobs that are too difficult for human workers to handle.
- Material handling systems – Conveyor systems or other systems that can move parts in production to any machine in the flexible automation system. Robotic automation is typically used to load and unload production machines from these material handling systems.
- Central computer control systems – Communicates part routing information and timing to machines in the material-handling system as well as coordinating each part processing machines’ operations.
- Manual labor & operators – The flexible style of automation system has an inherently high level of automation in its processes. However, people are still necessary for several important steps in the system. They are necessary for the overall management of the system, the repair and maintenance of the production equipment, the tool change procedures and sometimes for the loading and unloading of parts.
Flexible automation systems are the ideal system for batch processes and shops that have low-to-medium production level needs and high product variety needs. Systems that will likely have changes in demand and have production needs less than high volume will be a great fit for flexible automation systems.
Contact Midwest Engineered Systems to learn how we can analyze your current production systems and develop a flexible automation system that increases productivity and efficiency!
Building the future of manufacturing, together
World-class Automation