When it comes to automating food production lines, labor is usually the main driver—and for good reason. The American Bakers Association predicts a shortage of over 53,000 workers in the baking industry by 2030. Organizations like the North American Meat Institute are echoing similar concerns across food sectors. With current immigration policies under scrutiny, many trade associations fear the labor gap is only widening.
But while labor is a critical factor, it’s not the only reason food manufacturers are turning to automation. Rising material costs, SKU proliferation, and growing demand for consistency are forcing companies to rethink their production strategies.
Raw Material Costs Are Rising—and Getting Less Predictable
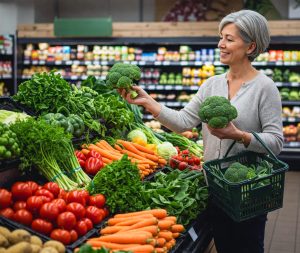
Egg prices are making headlines, but the cost surge extends well beyond breakfast staples. Sugar, corn, and cocoa are all under pressure due to global farming disruptions. Bakery and Snacks recently reported that historic droughts are driving commodity price volatility.
In North America, avian flu outbreaks have led to massive flock culls—affecting both egg prices and poultry supply chains.
And it’s not just climate or animal health creating challenges. In Ghana, illegal gold mining is replacing farmland. Nearly 19,000 hectares of cocoa farms have been lost to mining activities, according to the Ghana Cocoa Board.
Bottom line: Food producers are under intense pressure to reduce waste and get the most out of every pound of raw material. That’s where automation makes a meaningful difference.
SKU Explosion Is Cutting into Production Time
The days of long, uninterrupted production runs are fading fast. With more consumer options and custom packaging demands, food manufacturers are handling more SKUs than ever—often changing over lines multiple times a day.
Simply put, every time you change production, you reduce the amount of product you can ship.
Some manufacturers have added sensors and data collection tools to track downtime and losses. But these are reactive solutions. To stay competitive, you need proactive strategies that reduce line interruptions and improve changeover efficiency.
Scrap Is Costing You More—Here’s Why
Rising material costs mean that every off-spec product or batch of scrap is a bigger hit to your bottom line. Scrap doesn’t just waste ingredients and materials, it also represents lost labor, lost production time, and missed revenue.
Common culprits?
- Inconsistent changeover startups
- Manual portioning or handling mistakes
- Unstable line setups
Real-world examples:
- A dairy powder producer was seeing batch inconsistencies due to manual surges during ingredient loading. These surges compacted the product unevenly, causing moisture variations in the final blend. After automating batching, they reduced rework and improved quality.
- A pet food manufacturer found that workers were loading trays unevenly into dehydrators. The result? Inconsistent drying and excessive product loss. Automation brought consistency—and higher yields.
The Power of Consistency
One of automation’s most underrated benefits is repeatability. With automated systems, there’s no more “dialing in” after every line stop. You get precise portioning, predictable line behavior, and a consistently high-quality product.
The result?
- Less scrap waste
- Fewer quality issues
- Higher profitability per unit
Smart Automation: Doing the Right Thing, the Right Way
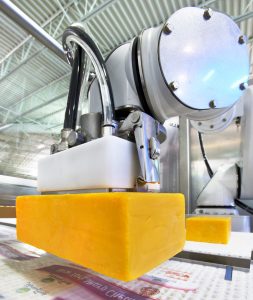
So, what makes a production line truly successful? Two things:
- Getting the right materials to the right place, at the right time, in the right condition
- Doing it with precision and simplicity
Automation helps ensure that ingredients are portioned and combined exactly as required. It also maintains critical variables like temperature—essential for consistency in products like batters, doughs, and meat blends.
Automation also excels at product handling. Many food items are sensitive to how they’re moved—too much pressure or friction can distort or damage them. Properly designed automation systems preserve product integrity as they move between operations, helping improve yields and reduce waste.
It’s Not Just Faster—It’s Smarter
Yes, robots and automation can move faster than people. But they also work more precisely, more consistently, and more predictably.
That consistency reduces your cost per unit—especially when you consider the time lost during manual fine-tuning or post-changeover adjustments.
MWES: Your Food Automation Partner
Of course, automation isn’t a silver bullet. The right system must be thoughtfully designed and tailored to your specific needs.
That’s where the right partner comes in.
At MWES, we specialize in delivering custom automation solutions built around your production goals. We don’t push a specific technology—we help you find the right tools for the results you need. Whether your focus is labor savings, product consistency, or operational efficiency, we’re here to help you grow.
Let’s talk about how automation can move your business forward—beyond labor savings!