In the rapidly evolving digital landscape, data centers are the backbone of global information storage and processing. The construction of these facilities demands precision, efficiency, and scalability. Robotic welding has emerged as a pivotal technology in meeting these demands, offering unparalleled advantages in the assembly of data center infrastructures.
The Role of Robotic Welding in Data Centers
Data centers require robust and precise fabrication of components such as server racks, structural frames, and cooling systems. Robotic welding ensures consistent, high-quality welds, which are crucial for the structural integrity and longevity of these components. By automating the welding process, manufacturers can achieve:
- Increased Production Rates: Robots operate continuously without fatigue, significantly boosting throughput.
- Enhanced Precision: Advanced robotic systems deliver exact welds, reducing errors and rework.
- Cost Efficiency: Automation lowers labor costs and material waste, leading to overall project savings.
Advantages of Implementing Robotic Welding
The integration of robotic welding in data center construction offers several key benefits:
Superior Weld Quality
Robotic systems provide consistent welds with minimal defects, ensuring the reliability of critical data center components. This consistency is vital for maintaining the high standards required in data center operations.
Accelerated Construction Timelines
Automation streamlines the fabrication process, reducing production time and enabling faster project completion. This efficiency is essential in the fast-paced tech industry, where time-to-market can be a competitive advantage.
Improved Workplace Safety
By delegating hazardous welding tasks to robots, the risk of workplace injuries decreases, fostering a safer environment for workers. This shift not only protects employees but also reduces liability and potential downtime due to accidents.
Maximizing ROI with Robotic Welding
Although the upfront cost of robotic welding systems can be substantial, the long-term financial benefits far outweigh the investment. By minimizing labor expenses, reducing downtime, cutting material waste, and accelerating production, manufacturers achieve a lower cost per part over time. For steel frame manufacturers, this strong return on investment makes robotic welding a smart and profitable automation solution.
Try our ROI calculator to see the savings.
MWES: Pioneering Robotic Welding Solutions
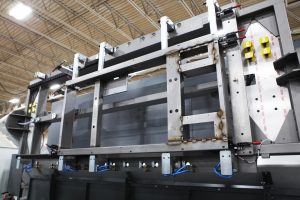
At Midwest Engineered Systems (MWES), we specialize in delivering state-of-the-art robotic welding solutions tailored for data center construction. Our expertise encompasses:
- Custom Automation Systems: Designing and implementing robotic welding setups that meet specific project requirements.
- Integration Services: Seamlessly incorporating robotic systems into existing production lines with minimal disruption.
- Ongoing Support: Providing maintenance and training to ensure optimal system performance.
Discover how MWES can enhance your data center construction projects by visiting our Robotic Welding Services page.
Conclusion
The adoption of robotic welding in data center construction is not merely a trend but a strategic move towards achieving higher efficiency, quality, and safety. As the demand for data centers escalates, embracing automation technologies like robotic welding will be instrumental in meeting industry needs.
To learn more about integrating robotic welding into your construction processes, contact MWES today.