Midwest Engineered Systems solved a palletizing problem for a refrigerated food logistics company. Our customer was using several workers to manually separate cases of products from pallets to fill orders in a refrigerated environment. They were continually plagued by staffing shortages, worker safety, accuracy and inconsistent throughput.
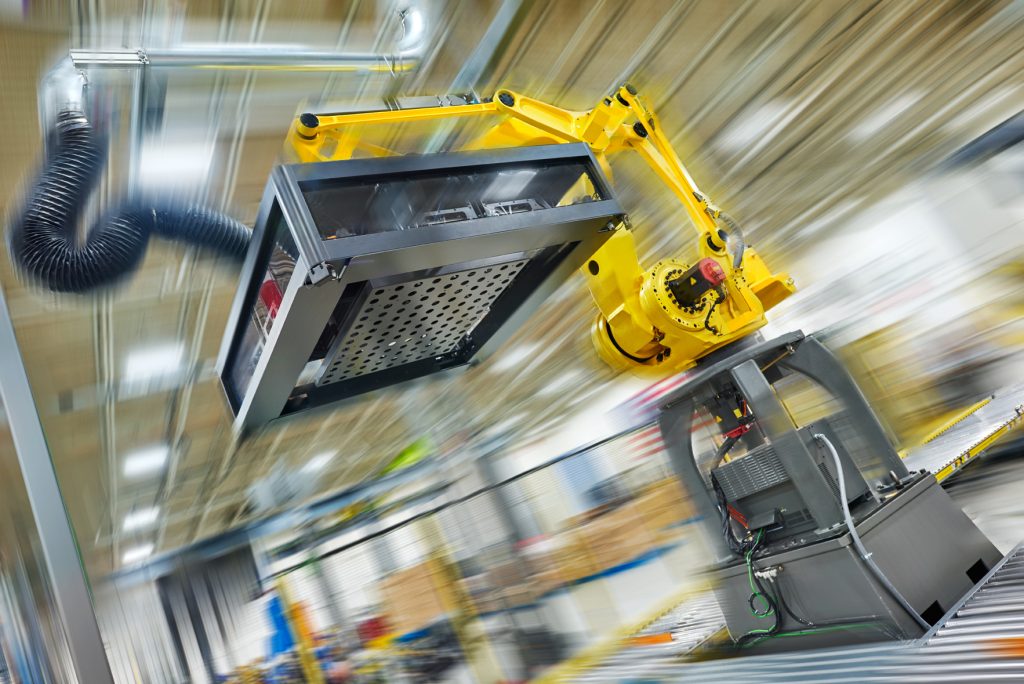
MWES provided a completely automated robotic layer-picking system that utilizes a FANUC M-410iB/700 industrial robot with a custom vacuum end-effector (EOAT) to pick an entire case layer (of 4-16 inches high) from a pallet at a time. Each pick layer contains about 17 boxes that in total can weigh up to 500 lbs. The system receives a batch of raw shipping orders and with a multi-axis vision system separate from the source pallet the layer quantity order lines from the non-layer lines. Next, the system takes the layer quantity orders from the source pallet and builds ready-to-ship order pallets. We use custom software to optimize this process with maximized pallet build quantities.
Additionally, the robotic layer-picking system had to interface with the customer’s Work Management System (WMS) to determine the optimal build sequence to fulfill the orders. The automated layer-picking system then instructs the operator on the best feed sequence for the build and order pallets, decreasing the work required to complete the order. When the order pallet is finished, it is sent to an automatic rotary stretch wrapper station where it is wrapped and labeled. The palletized order is then withdrawn from the system and stored in a staging area until shipped out. Incomplete orders are held in the buffer until the next line item on the source pallet is ready to be chosen.
- Easy to use and easy to maintain
- Requires a single operator to oversee
- Can operate non-stop 24/7
- Pays for itself within a few years
- It doesn’t take up much floor space
- Fencing keeps workspace safe
The robot ran a layer pick cycle time of 30 seconds (120 picks an hour) which brought about substantial improvements for the customer versus manually unloading the pallets. On top of that, moving the pallet unloading operation to robotic automation meant that they had a consistent throughput through the entire process while redirecting the extra labor to other responsibilities.
This custom robot layer-picking system is just one of the 4,000 automation solutions MWES has innovated in the past 30 years for a variety of industries. End-to-end custom automation solutions and robotic integration: MWES has the experience and expertise to design the right solution for your specific needs!
If your current process is similar to the one our customer was struggling with, then contact us today to request a quote!
Read more about MWES’ logistics and warehousing experience:
Robot automation improves efficiency, accuracy, safety and flexibility in all aspects of material handling and fulfillment, such as picking, packing, sorting, palletizing, loading and unloading operations. Robots can reduce labor costs, human errors and operational risks in logistics environments. Robotic integration is rapidly growing in the food handling and logistics industries. It offers many benefits and opportunities for the logistics, material handling and fulfillment industries. By using robot automation, logistics operations can optimize their processes, increase their productivity, and meet the changing demands of customers and markets. Learn more about MWES’ role in logistics and warehousing.