Automated Casting Finishing Production Line
- Home
- Recent Projects
- Automated Casting Finishing Production Line
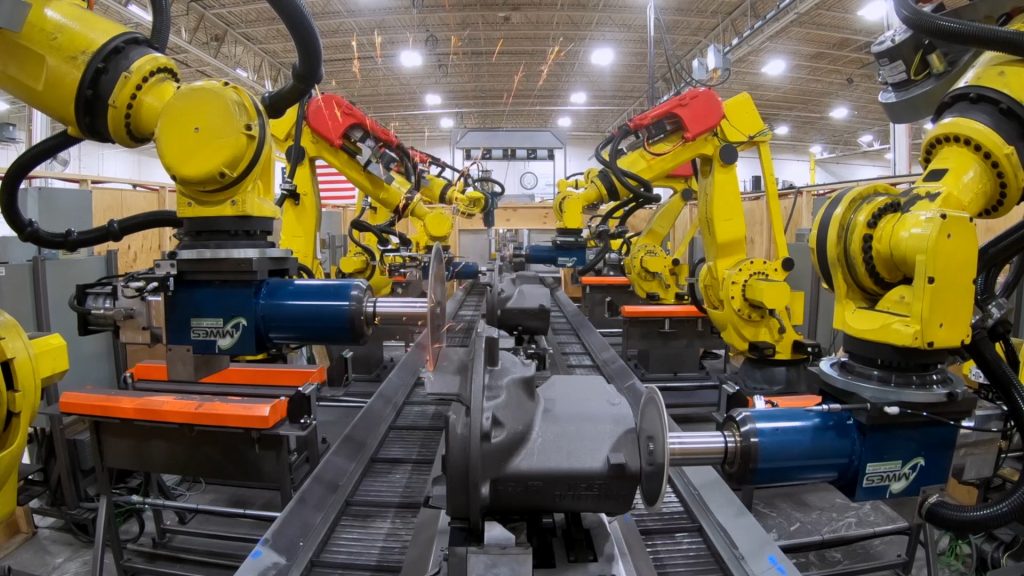
Project summary
MWES designed and built a system that would allow a single operator to control the entire steel casting finishing production line.
The Challenge
As a large foundry located in an area where unemployment is at an all-time low and where the population is low to begin with, the firm was feeling the realities of the workforce situation. Moving to a larger population center was certainly out of the question. Automation had to be the answer.
The goal of the project was to take as many as 30 different versions of a line of castings directly from the customer-supplied casting shaker through each of the grinding and cutting processes needed to turn a casting into a production ready part. Utilizing robotic automation frees this firm from the burden of having enough workers to keep the throughput moving forward on a labor-intensive assembly line.
The Solution
To achieve this, MWES designed a production line with 18 Fanuc industrial robots and a unique part clamping system that could accommodate all of the unique casting variations with one type of tooling. The finishing line utilizes seven robotic finishing stations, each with one of the various tools responsible for a specific part of the production line. At the end of the line, a robot will place the castings on a conveyor where operators will inspect and touch up the castings.
Once complete, the castings are then loaded onto skids that are then retrieved by a forklift for transfer to the next part of the operation. Skid de-stackers are also used to conveniently present single skids to the operators from a stack. Also, scrap conveyors are mounted on each side of the pallet conveyor to collect material that is removed during the finishing process. These two conveyors will take the material to a third conveyor that will dump the scrap into a bin.
The system receives the part via a casting infeed conveyor, where the part is then reoriented by the operator to a specified, consistent orientation to allow for the infeed scanner to locate the part. The part will travel under a scanner that will identify the part orientation to allow the robot to pick the part off the conveyor and place it into the system. The information from the infeed scanner will be sent to the robot which will then remove the part from the conveyor and place it on a fixture that is mounted on one of the pallet conveyor pallets. A buffer conveyor is used when necessary to assist when a line change is needed during a part changeover or a gap occurs in the delivery of the parts. The part is loaded into station #1 which has the first available empty fixture which has been recirculated through the system and transferred back to station #1. A robot with vision will be used to find the orientation of the part on the fixture, and that information is passed to each station for the robot path offset.
Once the part has left the camera station, it passes through the next three stations. Each of those three stations has two robots and is tooled with cutoff and grinding wheels. Using those tools, the robots remove the areas of large flash from the part. Once complete, the part then proceeds to the next two stations. At these two stations, the part is received by two smaller robots which are tooled with smaller detailing tools. Using a chisel and pencil grinders the robots work concurrently to remove the remaining areas of smaller flash.
After completing those stations, the part is moved to a station where a material handling robot orientates the part to allow for access to the remaining areas which may have flash and internal debris that was not removed in the prior operations. A robot with vision is used to find the orientation of the part on the fixture after the part has been reoriented. At the next station, the part passes through another round of large flash removal from two robots tooled with a large cutoff wheel and grinding wheels. The two robots work concurrently to remove the remaining areas of the large flash. The next two stations perform a second round of chisel and pencil grinding from two smaller robots. The two robots work concurrently to remove the remaining areas of the smaller flash.
At the final station, a robot picks up the part and places it on an outfeed conveyor. The operators will be able to do touch up and inspections on the part while on this conveyor. Once this is completed, the operators will use a gantry crane to load the part onto a skid located on the conveyor. At the exit conveyor, a forklift is then used to remove the skid. The part process will automatically be returned back to the start of the production line and a new skid is dispensed from the empty skid destacker onto the conveyor line.
Impact to the Customer
The automated production line MWES built for this customer allowed them to automate a production line that would normally require a great deal of labor and time to complete. This system afforded the customer greatly improved throughout by having an average cycle time of 36 seconds per part and requiring only a minimal amount of labor to operate.
Midwest Engineered Systems has a wide range of experience in building robotically automated production line systems. If you’re looking to improve your production line throughput, we have the knowledge and experience to make the project a success.
Contact us to learn how Midwest Engineered Systems can automate even your most complex and challenging operations today!
Innovation Through Automation
Client Details
A large foundry that specializes in steel castings.