Automated 3-piece Pipe Weld Cell
- Home
- Recent Projects
- Automated 3-piece Pipe Weld Cell
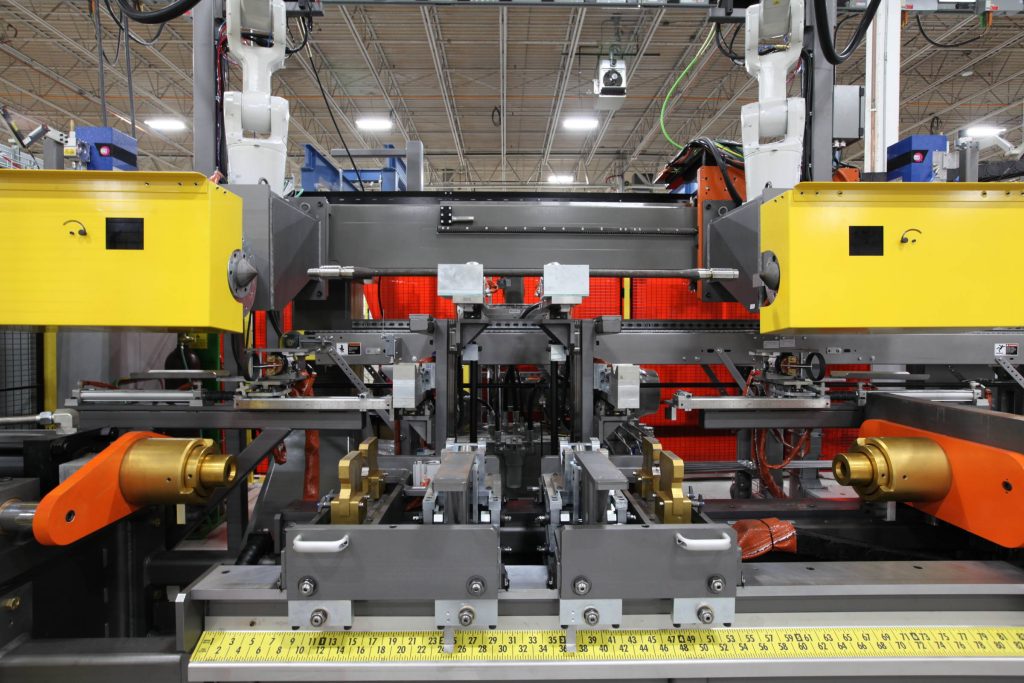
Project summary
MWES provided this firm with an automated 3-piece weld cell that would allow for minimal operator intervention during the manufacturing process.
The Challenge
The need to staff enough skilled welders to accomplish complicated welding tasks has become more difficult in recent years. With few working-aged adults entering the trades, more and more businesses are turning to robotic automation to keep their production up with the demand. This firm approached MWES to pursue robotic pipe welding automation to free them from the uncertainty of consistently having enough skilled welders on their staff and to keep their manufacturing throughput consistent going forward. The system had to accommodate pipes ranging from 1.125 to 4 inches in diameter and lengths from 4 to 20 feet.
The Solution
MWES designed and built a 3-piece pipe weld cell that allows for minimal operator intervention during the manufacturing process. The cell utilizes two robots equipped with Binzel Welding Torch Packages and mounted on a travel track. Additionally, the cell uses a 150,000 lb. custom hydraulic press that presses the threaded ends into each end of the pipe. The operator’s responsibility involves loading production information on the touch screen and performing changeover for the different diameter pipes.
The pipes are loaded into an unscrambler by the operator via a forklift. The operator then inputs the product information into the system and pipes are automatically loaded into the press station. The pipe automatically moves to an induction preheat station where infrared sensors maintain the pipe temperature until the weld station is ready to accept the pipe. Once the weld station is ready, the pipes transfer into the station, and welding robots use a tactile sensor to verify the joint location and welding begins with a specified number of passes on the joint. After the welding is complete, the pipe is automatically moved to a cooling rack and, then once cooled, onto a transfer table to be further processed.
Impact to the Customer
The automated 3-piece pipe weld cell MWES built for this firm allowed them to automate a welding process that would normally require skilled labor and time to complete. This weld cell afforded this firm improved throughput while only requiring minimal labor to operate. Robotically automating a welding process ultimately has a great return on investment (ROI).
Midwest Engineered Systems has a wide range of experience in building robotically automated weld cells. If you’re looking to improve your welding throughput, we have the knowledge and experience to make the project a success.
Contact us to learn about how Midwest Engineered Systems can automate even your most complex and challenging operations today!
Innovation Through Automation
Client Details
An industrial earth moving equipment manufacturer.