Automated Assembly & Testing Production Line
- Home
- Recent Projects
- Automated Assembly & Testing Production Line
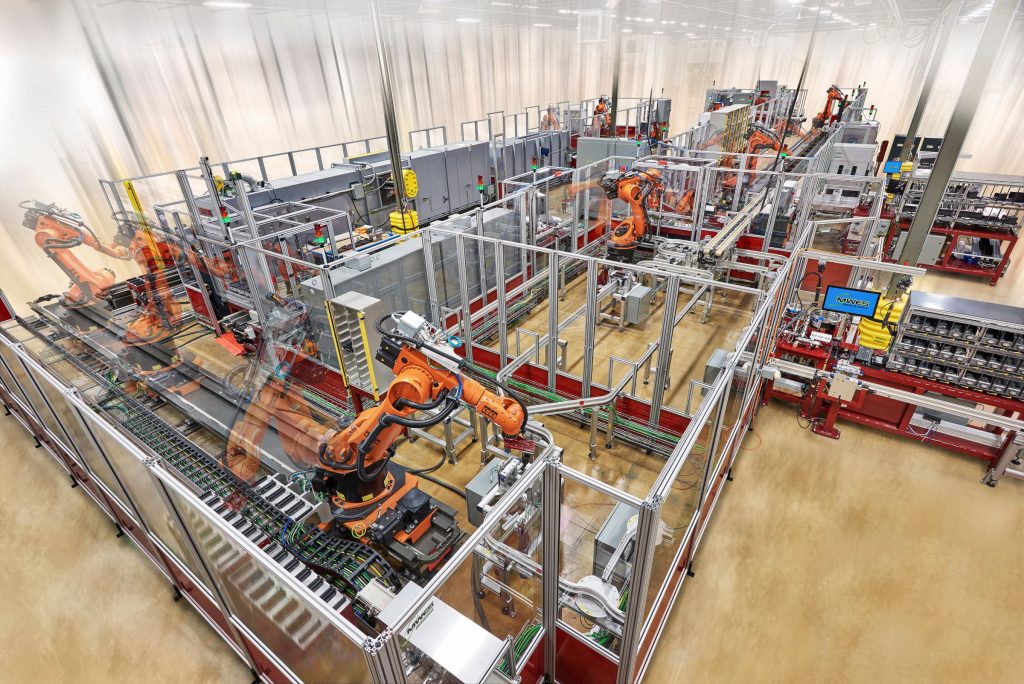
Project summary
MWES provided this firm with a robotically automated assembly and testing line for producing one and two stage electro-hydraulic servo valves (EHSV).
The Challenge
Producing parts for the aerospace industry is a delicate and complex process with no room for error. Perfection in the manufacturing process is paramount. For those reasons, a manufacturer of aerospace engines and turbines contracted MWES to develop an automated assembly line to produce servo valves.
The Solution
The main assembly system consists of three sections: armature subassembly, torque motor subassembly, and valve body final assembly. At each of these assembly stations, testing is performed on the completion of each subassembly. The assembly line is automated with five floor-mounted industrial robots and four track-mounted robots. The line also utilizes three electrical discharge machining (EDM) machines, an automated storage and retrieval system (AS/RS), a laser welding machine and a large industrial electrically heated conveyor oven.
Armature Subassembly & Test Cell
In the armature subassembly and test process, armature subassemblies are built, tested and sent to storage for use in the torque motor build assembly process. The subassembly and process is comprised of eight operations:
- Assembly press station
- Laser weld station (first four welds)
- Assembly of the feedback spring insertion station
- Laser weld station (last four welds)
- Weld test station
- EDM and blow-off station
- Laser marker barcode station
- AS/RS storage and reject station
The cell’s main robot is responsible for moving the armature assembly pallet into and out of the armature assembly operations while a smaller, bench-mounted robot, is responsible for performing the material handling functions that are part of the operations. The main robot is also responsible for placing the armature assembly pallet with the armature subassembly onto the outfeed conveyor and for picking empty armature pallets from the infeed conveyor and placing them at the assembly press station.
After leaving the armature subassembly cell, the subassembly is transferred via a conveyor to the track-mounted robot in the EDM station. Once the subassembly has been processed at the EDM station, the robot moves the subassembly to the laser marking barcode station. At this point, the subassembly is identified as either valid or rejected. Valid parts are placed into the AS/RS for storage and future use and rejected parts are routed to a reject conveyor for analysis by the operator.
Torque Motor Subassembly & Test Cell
In the torque motor subassembly process, the torque motor subassemblies are built, tested and sent to storage for use in the valve body final assembly process. The subassembly and testing process is comprised of six major operations:
- Manual assembly
- EDM and blow-off station
- Air gap measurement station
- Motor stroke gain station
- Laser marker barcode station
- AS/RS storage and reject station
The torque motor assembly process is a combination of manual labor and robotic automation processes. The track-mounted main cell robot is responsible for picking the correct armature assembly pallet with armature assembly from the AS/RS, or directly from the main cell tray and placing it onto the manual torque motor build station infeed conveyor system.
The operator then performs the necessary assembly functions for the manual assembly operation. The operator places the torque motor assembly pallet with the assembled torque motor onto the output conveyor system where it is transferred into the robotic system. The operator also places the empty armature assembly pallet onto the pallet return conveyor for transfer via one of the main cell robots back to the armature assembly cell. Valid parts are then transferred into the AS/RS for storage and future use. Rejected parts are placed onto the Torque Motor reject conveyor for reject analysis by the operator. Lastly, the robot moves the completed torque motors out of the AS/RS and to the conveyor system at the valve body assembly cell.
Valve Body Final Assembly & Test Cell
In the valve body final Assembly process, the torque motors subassemblies and valve body subassemblies are combined to build electro-hydraulic servo valves. The final assembly and testing process is comprised of eleven main operations:
- Valve build station
- Nozzle setting station
- Nozzle screen and plug assembly station
- Proof pressure testing stations
- Clean and cover station
- First calibration
- Stabilization bake station
- Second calibration
- Final test station
- Laser marking barcode station
- Final electrical checks and pack-out station
The valve body final assembly and testing process is a combination of manual and robotic processes. The operator at the manual valve build bench is responsible for performing the necessary assembly functions for the manual valve assembly operation. Once the operator has completed the assembly operations they place the valve, with the attached valve assembly pallet and the empty torque motor build pallet onto the conveyor system shuttle.
The conveyor then transfers the pallets to the nozzle setting stations. The cell’s main robot is responsible for moving the valve assembly pallet into and out of the valve assembly operation, loading the assembled torque motor with the assembly pallet onto the shuttle for delivery to the manual valve build station, and returning the empty torque motor build pallet to the EDM and Torque Motor Subassembly/Test area.
Once the nozzle set operation is complete, the conveyor transfers the valve assembly pallet to the second cell robot. The track-mounted robot is responsible for moving the valve assembly pallet into and out of the following valve body final assembly processes; screen and plug insertion, proof test, clean and cover, and bake operations. The cell robot is also responsible for sorting empty valve assembly pallets into the correct storage rack location as well as supplying the conveyor system with empty valve assembly pallets upon request.
At the nozzle screen and plug Station, a smaller bench-mounted robot is responsible for loading the necessary components into the two presses that perform the insertion functions. After proof testing is complete, the operator verifies that the proof test was successful. After a successful proof test, and after the valve assembly pallet has been delivered to the clean and cover station, the operator performs the necessary clean and cover functions.
For single-stage valve assemblies, the assemblies are sent back to the cell’s main robot and placed in the stabilization bake oven. For 2-stage valve assemblies, the assemblies are sent to the cell robot for delivery to one of the calibration stations. Upon successful completion, the cell robot transfers the valve assembly to the cell’s main robot for loading into the stabilization bake oven.
Upon completion of the bake process, the cell robot unloads the valve assembly pallets from the oven exit conveyor. The robot then moves the valve body to one of the final test stations. After completion of the final test, the main cell’s robot moves the valve body pallet into and out of the laser marking station. Valid parts are forwarded to the pack-out station. At the pack-out station, the operator is responsible for performing the functions that are part of the valve body assembly operation.
After pack-out is complete, the operator places the empty valve assembly pallet onto a pallet return conveyor for transfer back to the main cell robot. The robot then places the empty pallet onto the conveyor, where a robot picks empty pallets and places them in a storage rack.
Impact to the Customer
The automated servo valve assembly line MWES provided our customer with an enhanced operation that was previously performed by manual labor. Modernizing the assembly line with the inclusion of robots greatly improved this firm’s manufacturing throughput.
Midwest Engineered Systems has a wide range of experience in building full assembly line automation. If you’re looking to improve your assembly line throughput, we have the knowledge and experience to make the project a success.
Contact us to learn about how Midwest Engineered Systems can automate even your most complex and challenging operations today!
Innovation Through Automation
Client Details
A designer, manufacturer and service provider of control systems for aircraft engines, turbines and power generation.