Automated Spot Welding Assembly
- Home
- Recent Projects
- Automated Spot Welding Assembly
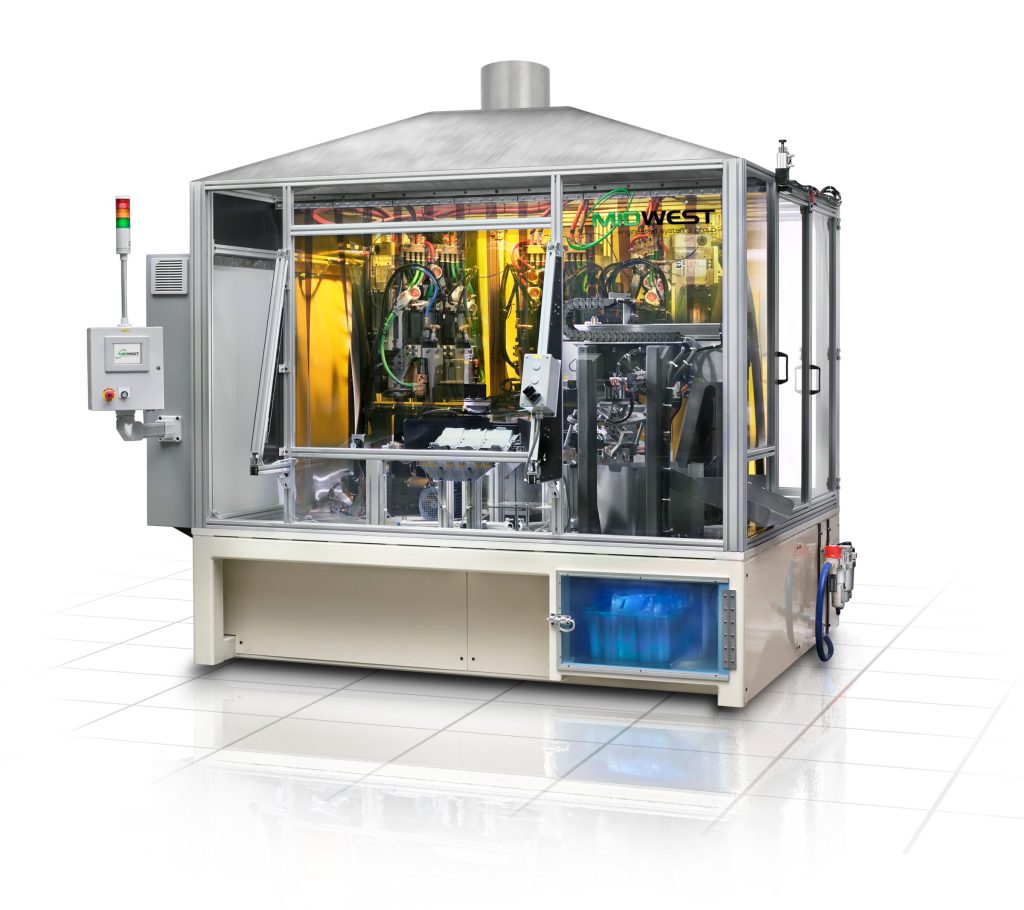
Project summary
MWES built a resistance spot welding automation cell as part of the assembly of automotive oil pan baffles.
The Challenge
Producing consistent spot welds on mass-produced automotive parts with manual labor is a gamble. With a shortage of trained welders and a variance in skill levels, an automated system was the only solution. A firm that produces parts for the automotive industry approached MWES to build an automated machine to spot weld the HFV6 oil pan baffle assembly.
The Solution
To achieve our customer’s goals MWES provided them with a welding assembly cell that included two separate fully-enclosed automation machines. One machine would handle welding three louvers onto a baffle plate, while the second machine would handle welding two diverters onto a baffle plate. Both machines are equipped with a six-station indexing dial and a pair of Milco C-type dual weld guns at three stations. The machines also include pneumatic automatic unload and reject chutes.
Both machines perform their respective operations in a similar sequence. With the louver welding machine, the operator loads the three louvers and the baffle plate onto the fixture at the first station. At the diverter welding machine, the operator loads two diverters and the baffle plate onto the fixture at the first station. Once the parts have been loaded the operator initiates the system via the HMI.
The dial on both machines indexes to the second, then the third and finally the fourth stations. At each of those stations, the dual weld gun automatically applies welds at the predetermined spots on the part. The fifth station is a buffer. At the sixth station, the completed part is pneumatically picked up and unloaded into a parts bin.
Impact to the Customer
The spot welding cell that MWES provided our customer can handle a total volume of parts in excess of 800,000 parts per year. That translates to one part every 10 seconds, which would be unachievable with a manual welding production line.
Midwest Engineered Systems has a wide range of experience in building automation systems for automotive applications. If you’re looking to improve your welding automation throughput, we have the knowledge and experience to make the project a success.
Contact us to learn how Midwest Engineered Systems can automate even your most complex and challenging operations today!
Innovation Through Automation
Client Details
A manufacturer of progressive die metal stampings and subassemblies based in Milwaukee, WI.