Bag Making Machine with Gantry Roll Loading
- Home
- Recent Projects
- Bag Making Machine with Gantry Roll Loading
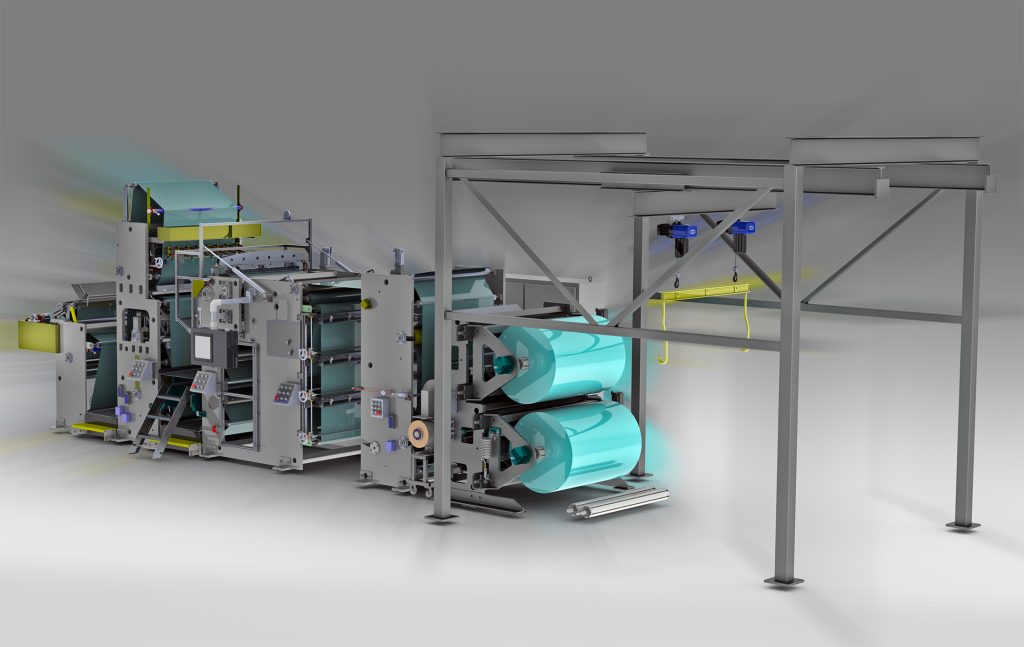
Project summary
MWES provided a firm with an automated web handling machine with a gantry roll loading fixture that would produce polyethylene bags in various sizes.
The Challenge
One of the biggest challenges with operating a large web handling system is working with 56-inch wide rolls that can weigh upwards of 2500 lbs. At those weights, it becomes unrealistic for the system operator to manually lift the rolls onto the unwind station. The system would unwind two rolls and guide them together to ultimately produce 1-6 mil plastic film bags of differing lengths. Because of MWES’ over 30 years of experience in building web handling solutions and our prior experience with this customer’s process, we were approached to provide a solution to this challenge.
The Solution
MWES provided our customer with a roll handling solution by pairing the web handling machine with an overhead gantry equipped with a motorized spreader bar. Utilizing a gantry allows the system operator the easily and with minimal effort to mount two full rolls of film onto the unwinding stand. Through the web handling process, the rolls are glued, perforated, and sliced and ultimately the final product is neatly deposited into containers.
Once two rolls of film are mounted in the unwind station, the web system unwinds them, guides them together and registers the web print together. The web then passes through a nip assembly, over a load cell roll and then into a linear web stop unit and passes vertically down through a punch tooling area and then back through the linear web stop unit.
After the rotary perforation units, the web is fed into the Zinger, SVT or Hot Knife section of the module. Based on the product being made, the web path is altered to slit and seal the web into bag sections and then through the zinger roll. The web is nipped against a driven back-up roll and the zinger roll flicks open the bags.
The web then passes in front of the inspection blower box with an inspection system light curtain. The perforated and sealed bags are drawn through a pull roll with a tension loop and into the wig wag arm using a tendency-driven roll and layer-placed in the final shipping boxes.
Impact to the Customer
The final machine MWES integrated for our customer gave them a production rate of 42 to 120 bags per minute (BPM) based on the overall length of each manufactured bag. Each produced bag ranges in length from 12 to 48-inches.
Midwest Engineered Systems has a wide range of experience in integrating machines for web handling applications. If you’re looking to improve your paper, film and foil manufacturing throughput, we have the knowledge and experience to make the project a success.
Contact us to learn how Midwest Engineered Systems can automate even your most complex and challenging operations today!
Innovation Through Automation
Client Details
A leading manufacturer of plastic shipping and packaging products, based in Wisconsin.