Cheese Stick Slicing & Stacking Conveyor System
- Home
- Recent Projects
- Cheese Stick Slicing & Stacking Conveyor System
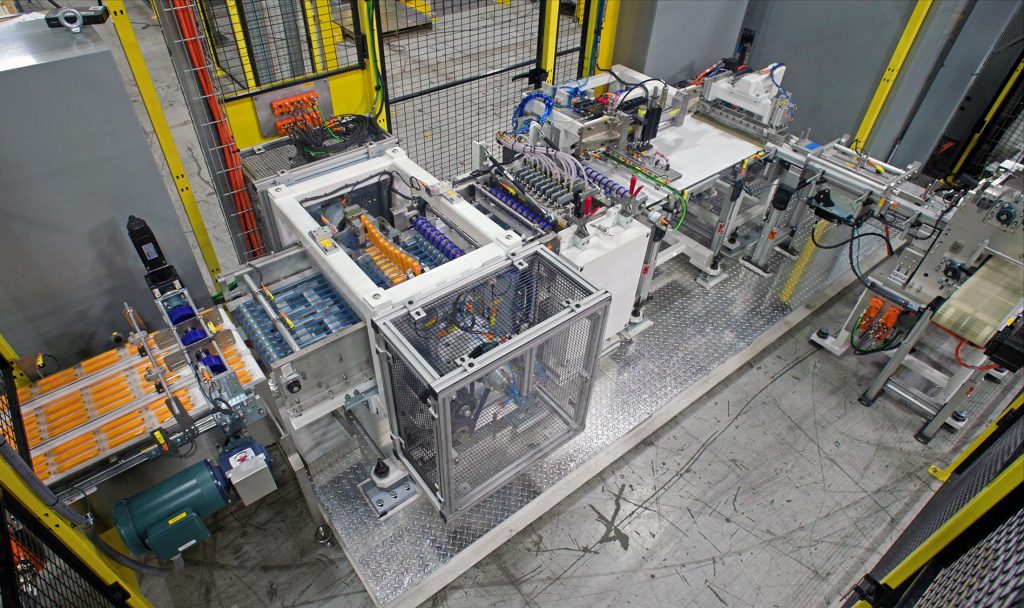
Project summary
MWES designed and built a cheese bagging system that would convey sheets of cheese sticks through a slitter and stack them before bagging.
The Challenge
To keep a food handling process contaminant-free and as USDA and FDA-compliant as possible, eliminating the human factor from the manufacturing process is crucial. Human workers add uncertainty to the quality of the production that automation does not suffer from. For those reasons, a national cheese producer contracted MWES to design and build a system that would include two inbound conveyors transporting thermoformed sheets of cheese sticks and then X-ray, slit and stack the sheets before transferring them to an outfeed conveyor. The system had to handle multiple configurations of sheets of cheese sticks per the final product: packs of 6, 12, 16 and 24 sticks.
The Solution
MWES provided our customer with an automated conveyor system that would merge two inbound conveyors transporting thermoformed sheets of 12 cheese sticks. The cheese sticks are delivered to the conveyors from two separate thermoformed machines. The sheets of cheese sticks pass under an X-ray scanner before moving to the vertical merger conveyor. On the merged conveyor the cheese sticks pass through a stick slitting and stacking system. Lastly, the stacked sheets transfer down the outfeed accumulator conveyor to the final bagging system.
The two infeed conveyors receive the cheese sheets from two thermoforming machines. Both conveyors pass the sheets under an X-ray scanner to detect contaminants and the quality of the product. One of the conveyors includes a helical incline that leads to the vertical merge conveyor at which point both conveyors merge into a singular conveyance line.
The sheets of cheese sticks approach the flipping conveyor with the blister side down and a flipping clamp rises into position between every other sheet of cheese sticks in a gap created by the speed increase. Every other sheet of cheese sticks conveys into the flipping clamp and the clamp flips over 180 degrees. From the flipping conveyor, the sheets of cheese sticks pass through the perforator, which will perforate between the cheese sticks that remain grouped.
Once perforated, the cheese stick sheets pass through the slitter and are separated into smaller sheets of three or four sticks. From the slitter, the smaller sheets of cheese sticks transfer onto a split belt singulation conveyor. The sheets of cheese sticks with blister side down are picked by three or four pick-and-place devices and then placed onto the blister side-up sheets, forming an interleaved layer.
Lastly, a laning conveyor centers the layers of cheese sticks and passes them to the single-lane stacker where the stacker accumulates the proper number of cheese stick layers vertically building a load. After the cheese stick loads have been built they are dropped onto a flighted conveyor that conveys the loads of cheese sticks to a downstream bagging system.
Impact to the Customer
The automated cheese stick slitting and stacking conveyor system that MWES integrated allowed our customer to have a cycle time of around 1 second per load and a production rate of up to 45 to 180 loads per minute based on the cheese stick quantity configurations. The system is compliant with all the food safety regulations of the USDA, FDA and WDA.
Midwest Engineered Systems has extensive experience in building food handling conveyor systems. If you want to improve your food and material handling throughput, we have the knowledge and experience to make the project successful.
Contact us to learn about how Midwest Engineered Systems can automate even your most complex and challenging operations today!
Innovation Through Automation
Client Details
A national cheese products producer based in Plymouth, WI.