Clutch Ball & Ramp Assembly Machine
- Home
- Recent Projects
- Clutch Ball & Ramp Assembly Machine
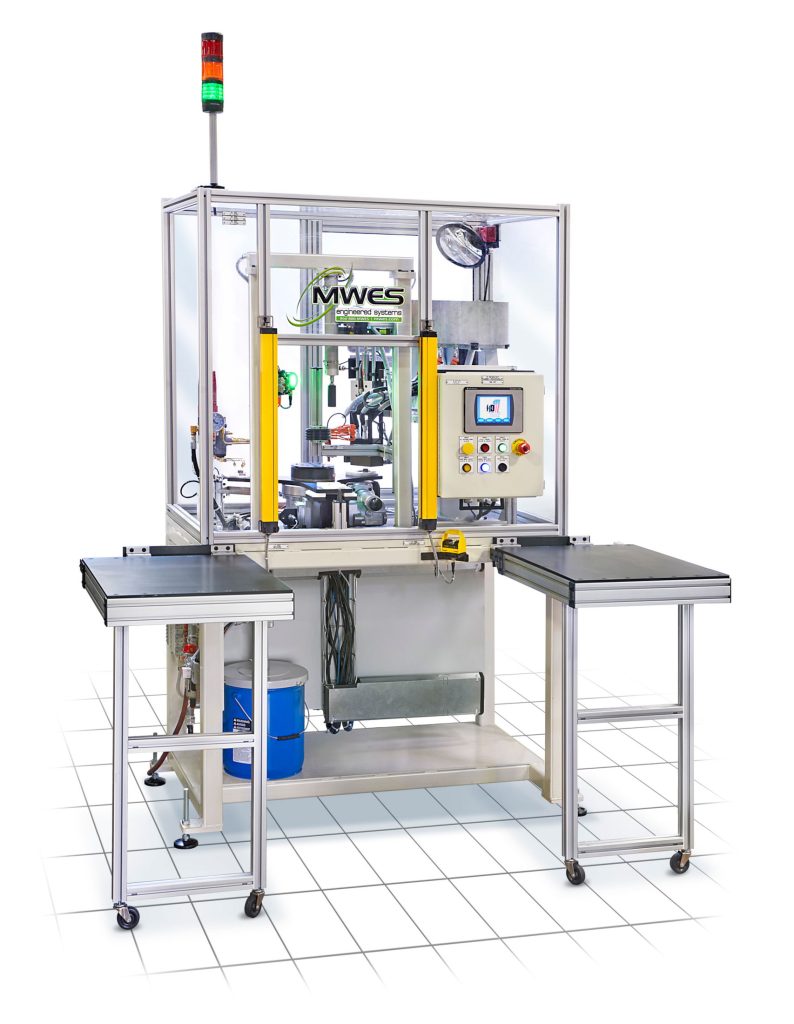
Project summary
MWES provided this firm with a semi-automated assembly machine for building clutch ball and ramps as part of a motorcycle manufacturing line.
The Challenge
To improve their throughput, this firm sought to enhance a clutch ball and ramp assembly operation that was performed exclusively by manual labor. The firm requested an automated machine with a small footprint that could safely assist a worker in producing parts.
The Solution
MWES provided our customer with a semi-automated turn-key clutch ball and ramp assembly machine that requires a single operator. The operator is solely responsible for placing the small parts on the three-position indexing table inside the machine and running its operations through an HMI. The machine is equipped with several safety features, such as a light curtain and a two-hand touch sensor to ensure that the operator’s hands are clear of the equipment when in operation.
First, the operator selects the part being run in the control panel. Next, the automatic ball-bearing feeder activates and begins loading three ball bearings into the multi-position escapement at the end of the feeder. The operator places the lower ramp assembly into the fixture at the load and pressing station, and then presses the cycle start button to advance the fixture to the automatic grease application station.
Once at the grease application station, the lubrication system simultaneously places a shot of grease into each of the three pockets in the lower ramp. During this time the operator loads the next lower ramp into the press fixture. Once the lower ramp is in place at the press station and the grease has been applied the dial table indexes to the ball-bearing insertion station. Once the fixture is in place the three-cylinder rods above the feeder escapement advance, pushing the ball bearings out of the escapement and seating them in their respective pockets on the lower ramp. At the same time, the lower ramp at the grease application station receives grease and the operator loads the next lower ramp into the fixture at the press station. The dial table indexes once the operations at the grease application and ball-bearing insertion stations are complete.
The operator places the top ramp on the assembly, the c-clip expander into the lower ramp, and a c-clip onto the c-clip expander. A part present sensor verifies that the hook on the lower ramp assembly is on the right side. If the part present sensor detects the correct part the c-clip press cylinder will advance pressing the c-clip onto the lower ramp. The operator then removes the completed ball and ramp assembly from the fixture and places a new lower ramp into the empty fixture.
Impact to the Customer
The safe and easy-to-use semi-automated machine MWES provided our customer, afforded them increased throughput without sacrificing jobs or safety.
Midwest Engineered Systems has a wide range of experience in building custom turn-key semi-automated machines. If you’re looking to improve your manufacturing throughput, we have the knowledge and experience to make the project a success.
Contact us to learn about how Midwest Engineered Systems can automate even your most complex and challenging operations today!
Innovation Through Automation
Client Details
An American motorcycle company from Milwaukee, WI.