Cut & Punch Automation Machine
- Home
- Recent Projects
- Cut & Punch Automation Machine
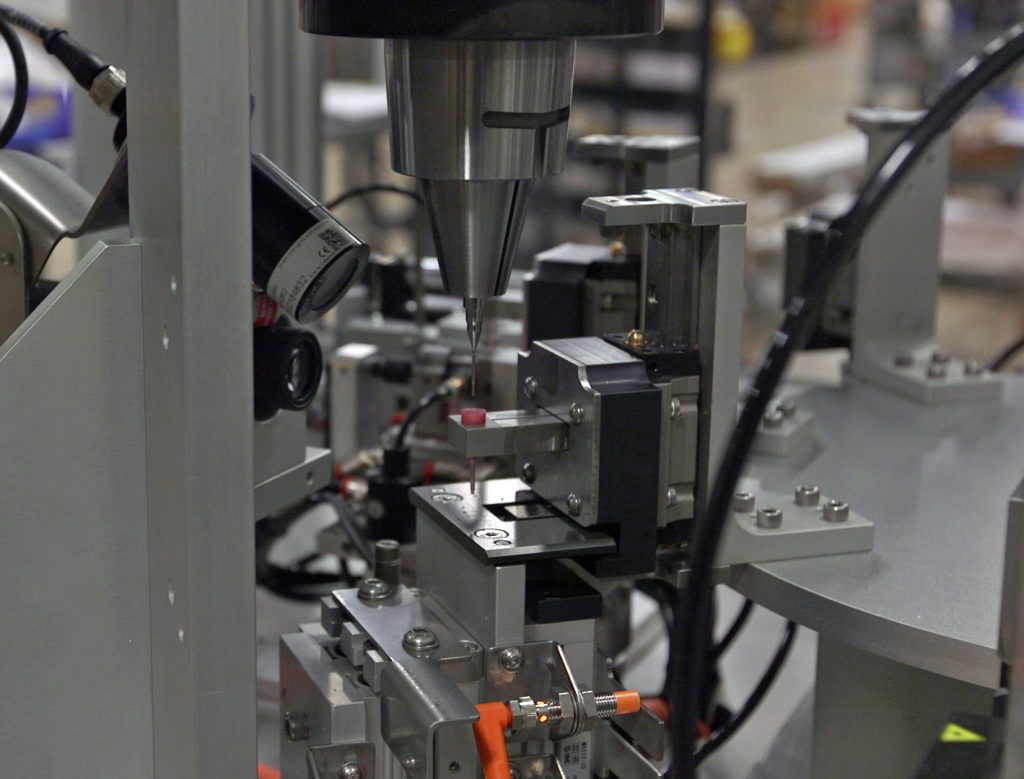
Project summary
MWES provided this healthcare firm with a high-volume, next-generation medical infusion sleeve cut and punch automation machine.
The Challenge
Working with small intricate parts in a high-volume manufacturing line is a challenge for a manual labor workforce. Speed and accuracy are critical in mass-producing components for the healthcare industry. For that reason, a firm working in the healthcare industry enlisted MWES to provide a next-generation automated machine that could cut and punch infusion sleeves.
The Solution
The automated machine that MWES provided our customer uses the same proven technologies for part feeding, cutting, nip pull and punching of the product but does it in a more efficient arrangement. MWES’ concept will be to utilize an indexing dial and a bowl feeder to minimize the amount of fixturing and for a relatively compact design.
At the first station, the parts are fed by a bowl feeder, and a part is picked and placed into the dial. A part is placed onto a servo-driven mandrel and rotated. A pneumatic actuated razor blade cutting system engages the part while it is spinning and scores the part. The part is placed back into the dial fixture and indexes to the next station. A pneumatic actuated nip removes the cut piece from the part and is air-assisted into a containment bin. A pneumatic actuated punch puts a hole in the part and the slug is air-assisted into a containment bin.
The part is placed onto a servo-driven mandrel and rotated as a vision camera system performs inspections of the hole size, tip-to-hole, length and fish eye. The part is placed back into the dial fixture and indexes to the next station. If the vision station fails the part, the part is dropped into a reject bin otherwise the good part is dropped into a good parts bin. This process is repeated for every part.
Impact to the Customer
The machine MWES integrated for our customer utilizes the same process steps as their current hardware, but the cycle time of the new automation machine is around 3.3 seconds or less from part to part or 18 parts per minute.
Midwest Engineered Systems has a wide range of experience in building custom machines for healthcare applications. If you’re looking to improve your assembly automation throughput, we have the knowledge and experience to make the project a success.
Contact us to learn how Midwest Engineered Systems can automate even your most complex and challenging operations today!
Innovation Through Automation
Client Details
A global manufacturer and distributor of materials and services for healthcare applications.