Engine Component Robotic Assembly System
- Home
- Recent Projects
- Engine Component Robotic Assembly System
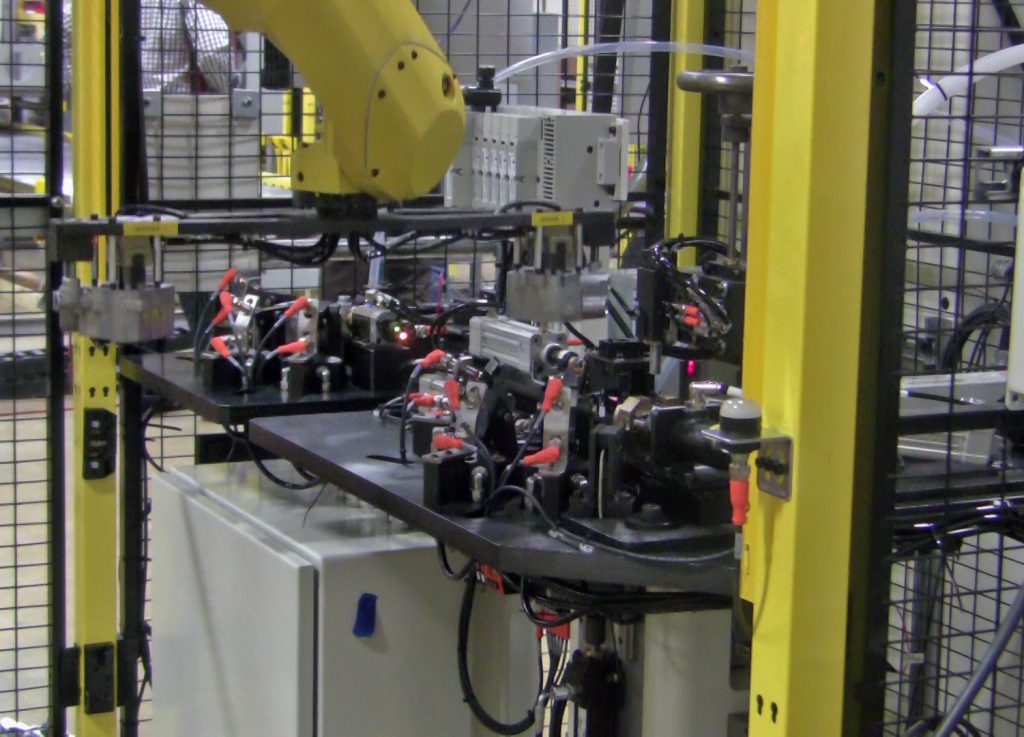
Project summary
MWES provided this firm with a robot work cell that assembles cam support plates and oil pump housings for motorcycle engines.
The Challenge
Assembling parts on an assembly line is an arduous task for a manual labor force. It’s repetitive, low-skill work and it isn’t easy to find enough workers to keep the throughput consistent. This firm approached MWES to assist it in transitioning from a manual assembly operation to one run with robots. The automation had to perform numerous operations quickly and had to integrate into an existing conveyor line.
The Solution
MWES provided our customer with two robotic automation work cells: one cell would handle the cam support plate assembly and the other cell would handle the oil pump housing assembly. Both cells are each equipped with a single industrial robot and integrate into an existing pallet conveyor which delivers and removes the assembled parts from the cells. The two cells require minimal operator interaction during the assembly process and are otherwise fully automated.
Cam Support Plate Assembly Station
At the cam support plate assembly station, the operator loads the ball feeders and dowl feeders with their respective parts and then initiates the assembly cycle. The robot first picks the cam plate from the pallet on the conveyor and passes the part through the air and chip blow-off stations to remove any residue on the part. The robot then moves to the regrip station and loads the cam plate into the dowel insertion fixture. Once the part is ready, the robot picks the completed part from the fixture and checks for the presence of the dowel utilizing a proximity switch.
The robot transfers the part to the assembly fixture where one dowel and eight balls are loaded and pressed into the cam plate to the proper depth. The cam plate is then flow tested for blockage and an impact quality mark is placed on good parts. Lastly, the robot picks the completed part and places it back on the pallet while rejected parts are unloaded into the reject chute.
Oil Pump Housing Assembly Station
At the oil pump housing assembly station, the operator loads the part feeders with various parts and then initiates the assembly cycle. The robot first picks the oil pump housing from the pallet on the conveyor and passes the part through the air blow-off station to remove any residue on the part. Next, the robot loads the oil pump housing into the fixture and loads and presses the ball to a designated depth in the fixture. The robot switches the assembly to a different fixture and the plunger, spring, and roll pin are loaded into the oil pump housing. Lastly, an impact quality mark is placed on good parts and the robot picks the completed part and places it back on the pallet while rejected parts are unloaded into the reject chute.
Impact to the Customer
The final system MWES delivered afforded our customer a cycle time for both robot cells of around 50 seconds for each assembly. This level of throughput could not be matched with a manual labor workforce when a single operator and a robot can perform all the required operations.
Midwest Engineered Systems has a wide range of experience in building automated robot assembly systems for the automotive industry. If you’re looking to improve your assembly throughput, we have the knowledge and experience to make the project a success.
Contact us to learn about how Midwest Engineered Systems can automate even your most complex and challenging operations today!
Innovation Through Automation
Client Details
An American motorcycle company from Milwaukee, WI.