Flexibility & Production Speed with Robotic Vision
- Home
- Recent Projects
- Flexibility & Production Speed with Robotic Vision
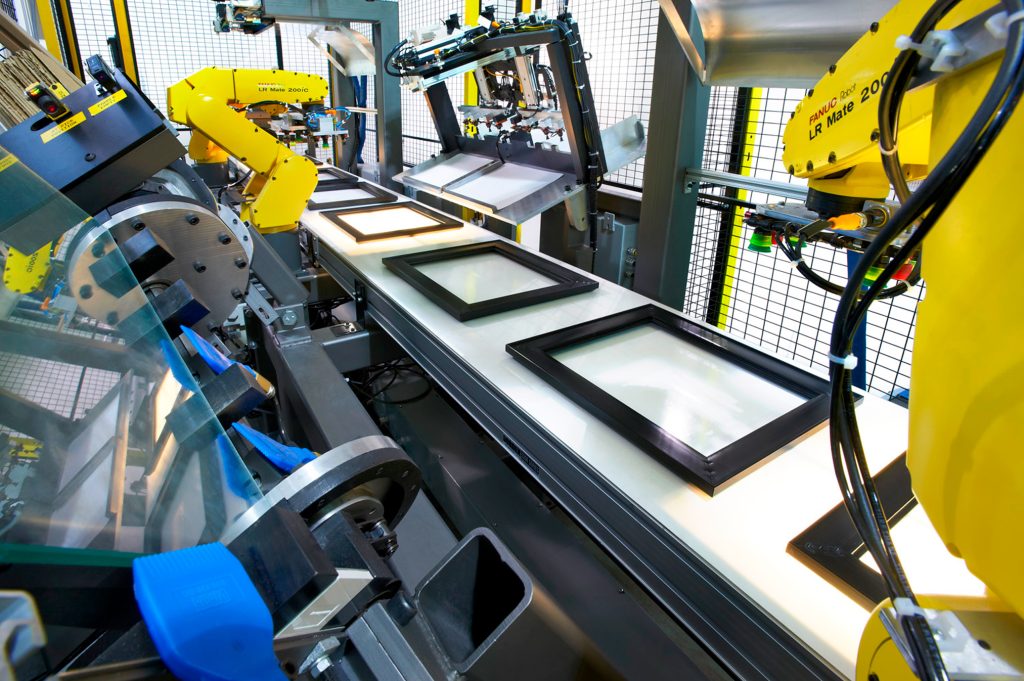
Project summary
MWES provided a consumer goods manufacturer with a robotic automation system for assembling picture frames.
The Challenge
A leading manufacturer of picture frames required more flexible manufacturing capability than their current high-volume systems could provide. A completely new automation system was needed to reach down into the markets where more store-specific styles were needed to satisfy the unique customer tastes these markets catered to.
One aspect that had prevented the manufacturer from reaching into those markets is their current production automation systems. These systems were designed to produce only a certain style of product but at very high volumes. To hit these massive quantities, the existing systems used hard tooling that required extensive changeovers to transition from manufacturing one product style to another. The time and costs to make these changeovers all but made it too costly to explore the quantities of products the new markets desired.
A more flexible system was needed that could be changed much more quickly to address the greater variety of styles these new customers were looking for without losing time and money due to changeover downtimes. Midwest Engineered Systems took up this challenge and built a system that was pliable to the needs of the manufacturer’s customers while providing the throughput necessary to be profitable.
The Solution
After analyzing the process, MWES developed a high-tech, reliable four-robot system that could perform all of the tasks necessary in the assembly of these picture frames while offering the lowest amount of change over time between product types.
Consisting of four assembly stations with infeed and outfeed support, the manufacturing process starts with verification that a frame is available at the correct infeed location. Once verification is complete, the in-feed robot picks the frame from one of two in-feed conveyors and places the frame on the assembly automation conveyor system.
The first assembly station in the process is where the picture frame glass is inserted. The station’s dedicated FANUC robotic arm pics a glass plate from stock and moves it to the dynamic glue system. The robotic arm uses integrated machine vision to apply the correct amount of glue on the glass and in the prescribed locations. Once the glue is applied, the robot places the glass into the frame assembly before the assembly moves to the mat, paper and flute insertion station.
According to each style of the product being produced, the robot will select and place the proper mat, paper and flute to be placed into the frame assembly. The robot system also relies on machine vision to precisely locate these materials inside the frame without the need for specialized tooling.
The next step in the process is preparing and placing the back panel onto the frame assembly. The dedicated FANUC industrial robotic arm picks the appropriate frame back and moves it through a progression of movements under the glue head system to apply the correct amount of glue at the specific locations necessary to ensure proper adhesion and a good finish. Once again, machine vision is employed to guarantee proper alignment of the back to the frame assembly.
The last step is a pressing operation to ensure the glues adhere properly using a pneumatic press. After pressing has finished, the completed frame assembly indexes off of the assembly conveyor and onto the customer-supplied outfeed conveyor.
Impact to the Customer
The MWES-designed production automation system can produce 900 frames in two hours – including the time necessary to change the machine over from the prior product style. The system achieves this speed from a variety of factors including the ability to be reloaded with components without having to slow or stop the automation and the adaptability of machine vision in the production system. That vision ability is also one of the enablers allowing the system to change over to similar products quicker than using purpose-built tooling and jigs. It also allows for the automation system to operate on seven different sizes of picture frames.
Relying on machine vision instead of product-specific tooling to align and perform the picture frame assembly operations has allowed MWES to achieve the goal of having a high-speed production system without the downside of time-consuming changeovers. This ability has directly enabled the customer to see the production efficiencies and throughput needed to be competitive in new markets and at smaller production runs
Midwest Engineered Systems has a wide range of experience in building robotic assembly line systems. If you’re looking to improve your assembly line throughput, we have the knowledge and experience to make the project a success.
Contact us to learn how Midwest Engineered Systems can automate even your most complex and challenging operations today!
Innovation Through Automation
Client Details
A designer and manufacturer of home decor products based in Waunakee, WI.