Robotic Case Packing & Palletizing Automation System
- Home
- Recent Projects
- Robotic Case Packing & Palletizing Automation System
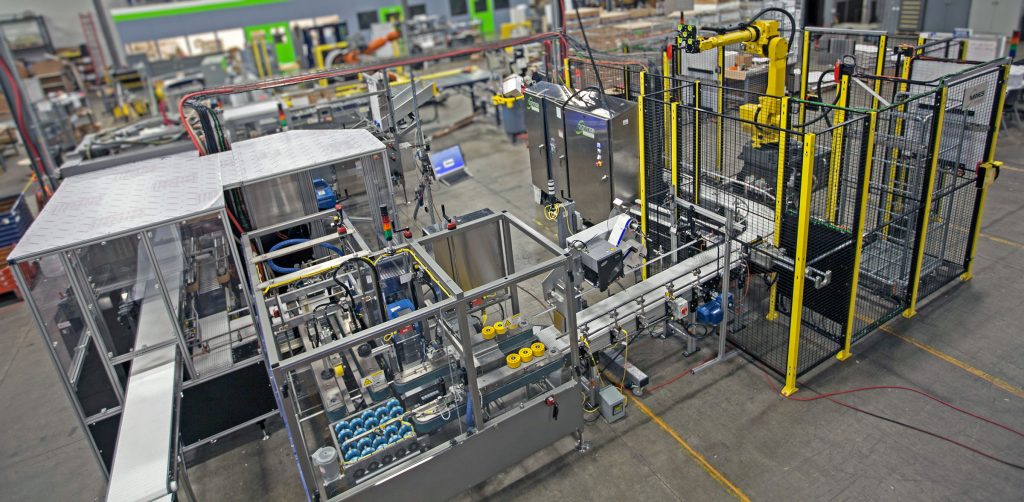
Project summary
MWES provided a biosolutions firm with a robotic automation cell for case packing and palletizing bags of frozen culture.
The Challenge
Keeping case packing throughput steady with manual labor is a challenging prospect. Forming the cases, filling the cases with the correct quantities, sealing and labeling the cases, and finally stacking the cases neatly on a pallet or trolley opens the door for a great deal of variance when human workers are performing all the operations. To perform all of those operations this firm contracted MWES to completely automate that entire process.
The Solution
MWES provided our customer with a robotically automated system that utilizes a 4-axis delta robot, an automatic case former with inline flange sealer, a case labeling station, a case weight check station and an industrial 6-axis palletizing robot with a vacuum cup EOAT. The various production stages are connected via multiple USDA-rated conveyors. The operator utilizes the RSView HMI to select a production recipe and the recipe data is transferred in a one-way fashion from the Recipe Manager Database.
The process begins at the HMI where the operator selects a production recipe and loads a trolley into the trolley handling bay. The system starts and the case-forming machine takes flattened case blanks, folds the bottom flaps and glues them into place. The case forming conveyor transfers the formed cases onto the case packing conveyor. The formed cases pass through a sensor that tracks the case’s placement on the conveyor. The bags are rotated 90 degrees and enter the case packing machine in a staggered fashion on a separate conveyor. The case packing robot tracks the placement of the bags on the infeed conveyor. Once the bag enters the bag picking area the robot picks a bag one at a time and places it inside the corresponding case.
After a case has been filled, it indexes to the automatic weight checking station for a final weight check to ensure product accuracy. If the case’s weight aligns with the weight requirements the case is transferred to the case closing and sealing station. The adhesive is applied to the case flaps and the flaps are then folded down. If the case fails the weight check, the flaps are folded down without adhesive so that it is easier for the case to be manually reworked by the system operator and transferred to the reject station. The sealed cases are transferred to the labelling station where required product information is placed on the case.
Once the labeled cases are complete they are indexed to the palleting robot. The robot picks individual cases and stacks them on a wheeled trolley. Once the trolley is full, the operator removes the trolley from the loading station and places an empty trolley in its place.
Impact to the Customer
The automation system MWES provided our customer gave them a fully automated packing and palletizing system that produces highly accurate results and is safe for the operator. The system handles different bag weights and bag sizes, along with three varieties of case sizes. The automation system has a bag picking rate of 16-40 bags a minute, with the rate based on individual bag weight. Additionally, the palletizing robot operates continuously at a rate of 2.5 to 6 cases per minute when loading the trolleys. The entire material handling automation system can be handled by a single operator.
Midwest Engineered Systems has a wide range of experience building custom systems for case packing and palletizing operations. If you want to improve your material handling throughput, we have the knowledge and experience to make the project successful.
Contact us to learn how Midwest Engineered Systems can automate even your most complex and challenging operations today!
Innovation Through Automation
Client Details
A leading biosolutions producer based in Denmark.