Robotic Flame Treater System
- Home
- Recent Projects
- Robotic Flame Treater System
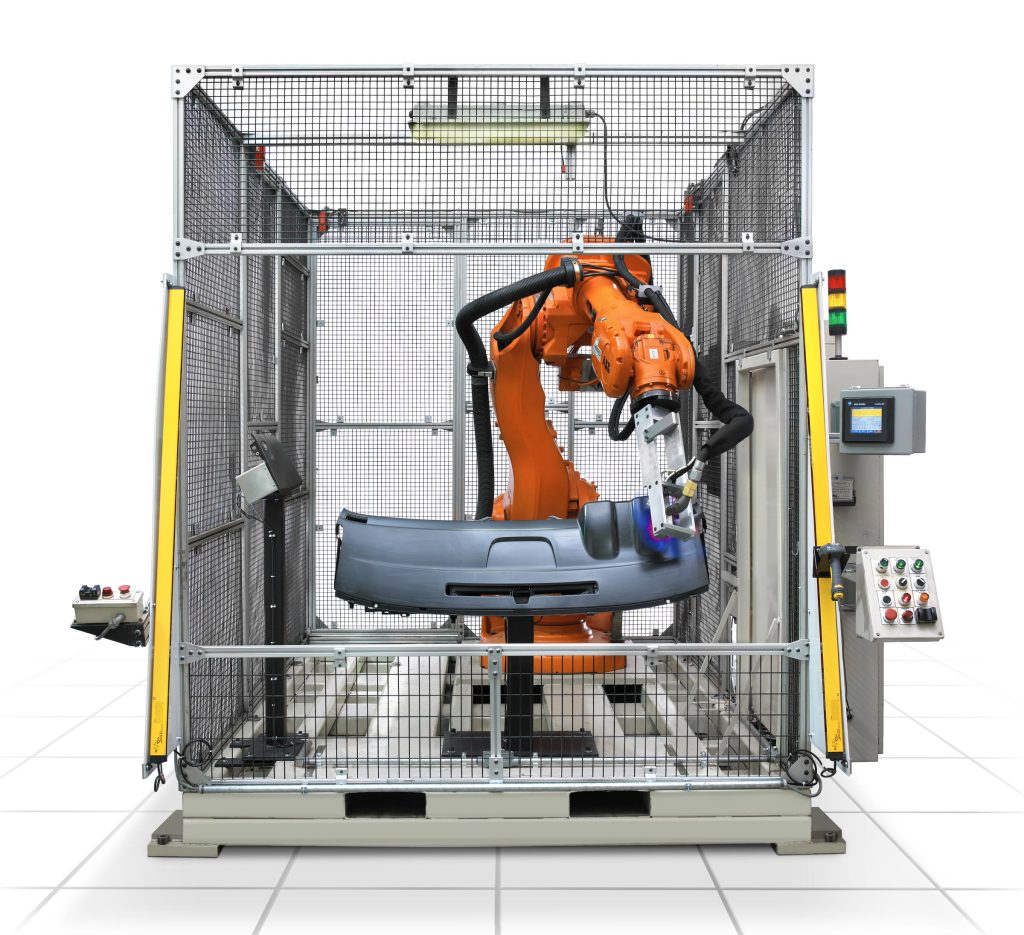
Project summary
MWES reprogrammed and converted an existing robot cell into one that performs flame-treating operations on automobile parts.
The Challenge
Designing and building a robotic automation system from scratch is a very expensive investment for any size business. However, in some circumstances, simply reconfiguring an existing robot automation cell to perform a different operation can be the most economical solution. Recently, a parts provider for a leading automaker contracted Midwest Engineered Systems to reintegrate an existing robot work cell, that performed riveting operations, into a robotic flame-treating system for a sports car base frame and glove box. The flame-treating cycle time for the entire process had to be less than one minute.
The Solution
MWES reprogrammed and switched out several components from the old robot rivet cell, and converted it into a flame-treating system for the base frame and glove box. The entire flame-treating system can be performed by a single operator with minimal training and physical labor. The system uses an ABB IRB-175/2.55 robot with an Enercon Dyne-A-Flame DF400 Flame Treater System EOAT and is controlled by an Allen Bradley SLC 5/04 PLC.
The flame-treating system begins when the operator manually places the base frame and glove box assemblies into the mounting fixtures in the robot work cell. Before leaving the cell, the operator scans the barcode on the parts being flame treated, to identify that the correct part is being treated. At the Allen Bradley PanelView Plus HMI interface outside the robot cell, the worker can set up and run the machine.
The flame system automatically ignites and the robot flame treats the base frame and the glove box while circling the fixture. Once the flame treatment is complete, the system allows the worker back into the robot cell to manually remove the parts from the fixtures and place them in an inspection station.
Impact to the Customer
The robotic work cell that MWES reconfigured for this firm, saved them a substantial amount of money by reusing their existing components. The flame-treating system ultimately gave them a cycle time of 42 seconds, to flame-treat the base frame and glove box together.
Midwest Engineered Systems has a wide range of experience in building robotically automated work cells. If you’re looking to improve your manufacturing throughput, we have the knowledge and experience to make the project a success.
Contact us to learn how Midwest Engineered Systems can automate even your most complex and challenging operations today!
Innovation Through Automation
Client Details
A leading parts supplier for a large automotive manufacturer.