Robotic Unpacking & Packaging Disposal Automation
- Home
- Recent Projects
- Robotic Unpacking & Packaging Disposal Automation
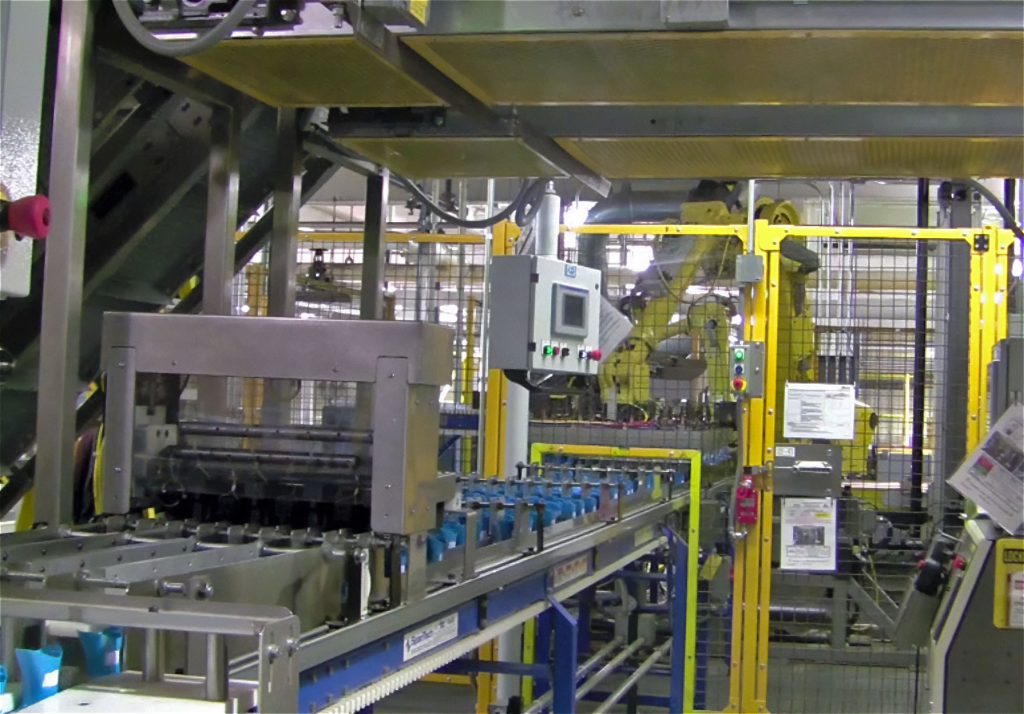
Project summary
MWES provided this consumer products manufacturer with a robotically automated unpacking and handling system for unloading sprayer nozzles and disposing of their packaging.
The Challenge
Unloading a substantial amount of individual parts per layer from a pallet containing multiple layers is a laborious job for any worker. Not only that but the parts have to be neatly placed on a conveyor so they can be transferred to the assembly station. Typically multiple steps are needed to unpack shipped containers of parts and dispose of the cardboard containers they came in. To make this process as quick and easy as possible, this firm sought out MWES to produce an automated solution for this problem. The automation had to handle large trays of parts, with half the parts facing the opposite direction, unload those parts efficiently onto a conveyor and neatly dispose of the packaging material.
The Solution
MWES provided our customer with an automated solution that utilizes two robots, an eight-lane separation conveyor and a corkscrew merging lanes. Both robots are equipped with custom end effectors (EOAT) where one robot handles removing and disposing of the packing material and the other robot picks all 128 parts from a tray and transfers the parts to the outfeed conveyor.
Pallets of trays, 16 layers high, arrive in the system and are removed one layer at a time with an automated layer stripper. The individual trays are transferred on the infeed conveyor to the robot unloading station. There the disposal robot removes the cardboard tray cover and the internal part separators and then flattens both into a pile for recycling. Next, the picking robot lifts all 128 parts at once from the tray bed. Once clear the disposal robot removes the plastic thermal form tray and stacks it on the outfeed conveyor. The plastic trays are indexed out and stacked for future use or recycling.
The robot transfers all the parts from the tray to the outfeed separation conveyor, where it places 16 parts at a time into four of the eight lanes on the conveyor. As it places the groupings of parts, the robot rotates the gripper 180 degrees so that the opposite-facing parts are placed in the conveyor pointed in the correct direction. The parts travel down the conveyor and transfer through a corkscrew staggering system that assists in merging the parts from all eight lanes down to a single lane. On the single file conveyor, the parts travel out of the system for future assembly.
Impact to the Customer
The automation system MWES provided our customer allowed them to run a relatively mundane process quickly and efficiently with only a single supervising operator. The speed and accuracy of this process would not be possible without robotic automation.
Midwest Engineered Systems has a wide range of experience in building robotic unpacking and handling systems. If you’re looking to improve your material handling throughput, we have the knowledge and experience to make the project a success.
Contact us to learn how Midwest Engineered Systems can automate even your most complex and challenging operations today!
Innovation Through Automation
Client Details
A multi-national manufacturer of household cleaning supplies.