Spring Assembly Machine
- Home
- Recent Projects
- Spring Assembly Machine
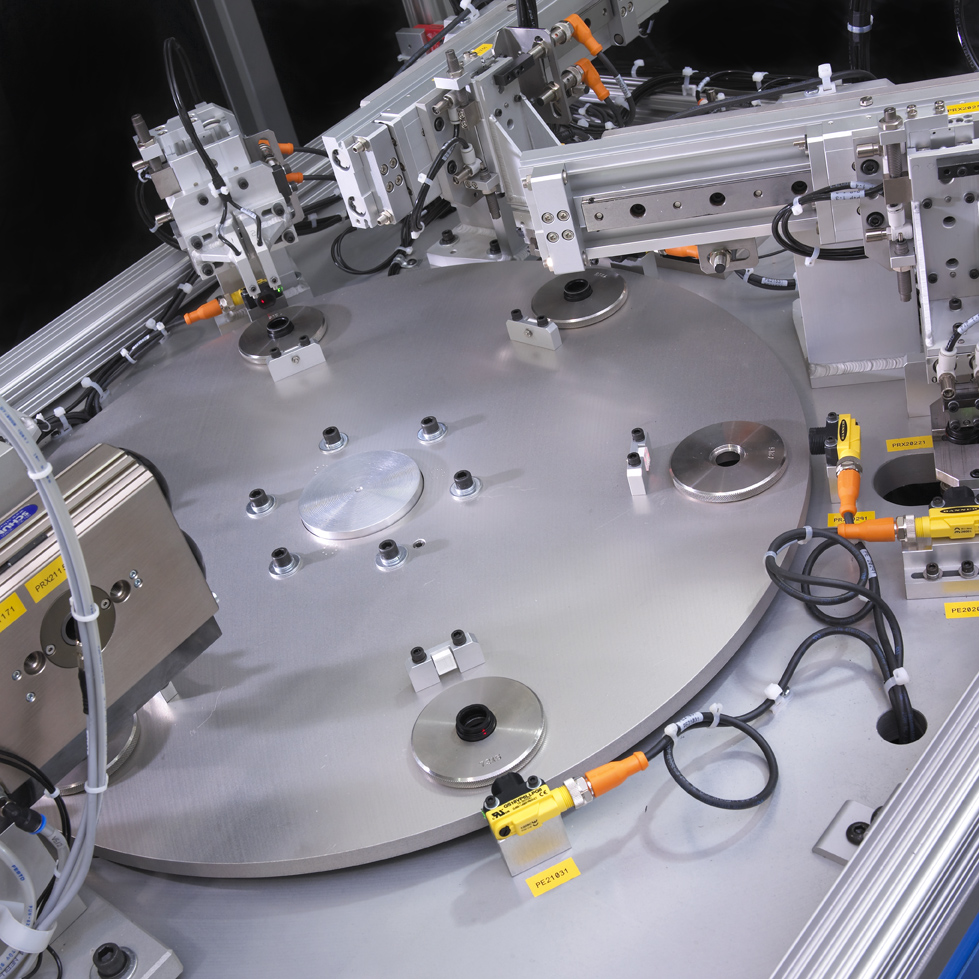
Project summary
MWES built this firm an automation machine for assembling springs onto a rubber input seal.
The Challenge
Intricate part assembly can be a tricky operation when performed manually. Human workers do not have the consistency of performing continuous repetitive motions on an assembly line. For that reason, this rubber compounds manufacturer came to MWES looking to fully automate their process of assembling a spring onto a rubber input seal.
The Solution
MWES provided this firm with a machine that uses a 15-inch cast aluminum vibratory bowl feeder system for the input seal loading and a Camco 601RDM six-station dial with a 24-inch aluminum top plate for the assembly process. The dial plate contains six-part fixtures that are designed with a tooling quick change to accommodate the assembly of different parts. The automatic seal assembly system includes a 10-inch cast aluminum vibratory bowl feeder system. To assure the quality of the spring installation, the machine utilizes a conductivity sensor, as well as proximity sensors for spring presence verification. Once the assembly is complete, the unloading system uses a pneumatic “pick and place” system to unload the completed parts from the fixture on the dial and into the proper bins.
The operation of the spring assembly machine begins when a rubber input seal is fed into a “dead nest” from the vibratory bowl feeding system. Then “pick and place” system picks up the rubber seal and places it onto the fixture located on the dial plate at the load station. The rubber input seal indexes to the metal insert detection station, where a proximity sensor detects the installation quality of the rubber input seal. Once the input seal is approved, the assembly dial indexes to the spring assembly station where the springs feed out from the vibratory bowl into the spring drag mechanism. The mandrel comes down over the spring from where the spring becomes affixed to the mandrel.
The assembled part then indexes to the spring inspection station where the spring assembly is inspected for the proper installation of the spring by a pneumatically operated continuity contact sensor. Once the assembled part passes inspection, the dial indexes to the spring presence station where two proximity sensors are utilized to check for the spring’s presence. Lastly, the assembly part indexes to the unload station where the assembled part is either placed in the “good parts” bin or the “bad parts” bin.
Impact to the Customer
The spring assembly machine that MWES provided our customer achieved an assembly rate of 1200 parts an hour. This machine gave the customer the peace of mind that they had consistent spring production throughput, all the while keeping the build quality to a high standard.
Midwest Engineered Systems has a wide range of experience in building part assembly machines. If you’re looking to improve your assembly throughput, we have the knowledge and experience to make the project a success.
Contact us to learn how Midwest Engineered Systems can automate even your most complex and challenging operations today!
Innovation Through Automation
Client Details
A small components manufacturer based in Wisconsin.