Track Seal Inspection & Assembly Automation
- Home
- Recent Projects
- Track Seal Inspection & Assembly Automation
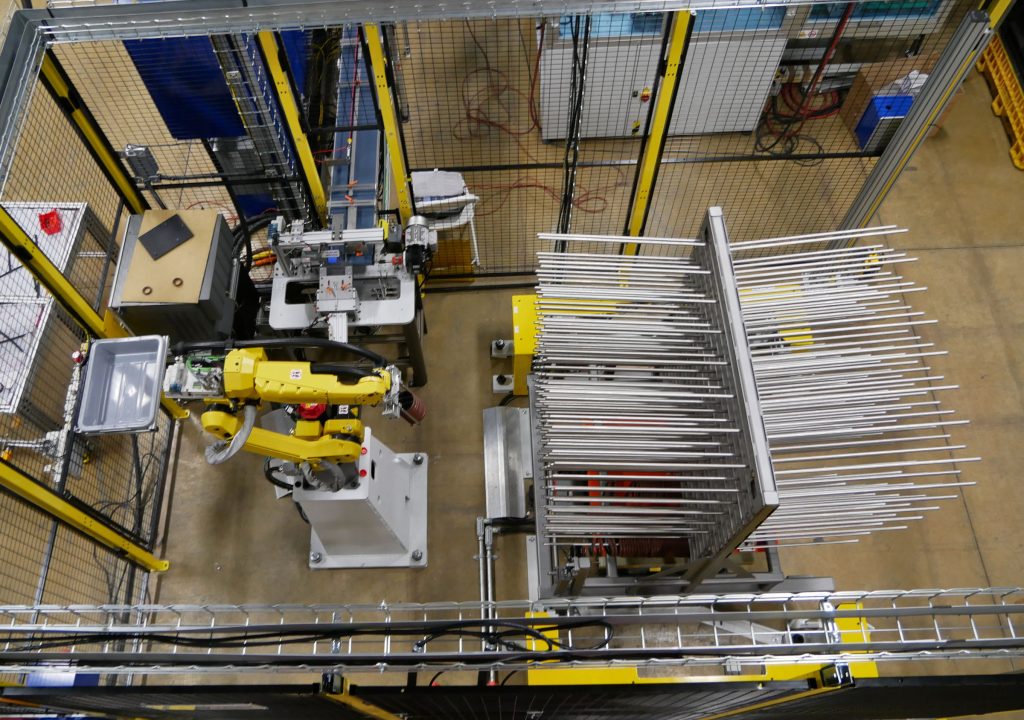
Project summary
MWES provided this firm with a robotic automation assembly system for inspecting, assembling and packing polycarbonate track seal cans and lips.
The Challenge
Acquiring enough manual labor in a tight labor market is a challenge that all manufacturers face. For that reason, more and more manufacturers are investing in robotic automation to run their assembly lines. This firm needed to mass-produce track seals quickly and efficiently as part of their consumable parts line.
The Solution
The robotic assembly system MWES provided to our customer allows for minimal operator interaction during the assembly process. The operator loads the rings, cans and lips into their respective hopper, as well as loads the cartons, bags and totes. Lastly, the operator adjusts the conveyors and tracks to accommodate the seal size before selecting the assembly on the HMI.
The automation system consists of a pair of bulk hoppers, one for the can and lip and the other for the load ring. The bulk feeders feed parts from bulk totes into their respective bowl feeders. Each bowl feeder cingulates and orients the parts so that they are ready for the first inspection machines. The dial table presents each part under a series of cameras and laser measurement sensors that inspect each part for the desired quality characteristics. The transparent dial table allows the parts to be inspected from the top and the bottom without needing to flip the part. Rejected parts are directed to a sequestered container to keep them from being mixed back in with good products. Upon exiting the first inspection machines, the parts are transferred onto another conveyor system.
Upon exiting the bowl feeder, the parts are conveyed to the inspection machines where they are transferred onto a transparent rotating dial table. The four-station rotary dial machine with interchangeable tooling plates for different size seals. The first station loads the load ring onto a post, the second station loads the can and lip, the third station presses the can and lip into the load ring and the fourth station unloads the assembly from the dial. The seal assembly then passes through a height inspection station that will verify the assembled height of the seal. Rejected assemblies are directed to a sequestered container to keep them from being mixed back in with good assemblies.
Once the parts have exited the assembly machine the track seal assemblies are transferred to a stacking fixture that will stack the seals in quantities of ten. The robot unloads the fixture and places the seals on a rack for post-curing of the seals. The six racks are double-sided to allow for 144 spindles on each side. Each spindle holds 50 seal assemblies and one cart holds 14,400 seal assemblies. A docking station positions the carts for automatic loading by the robot. Once one side is fully loaded, the docking station rotates the cart 180 degrees to load the second side.
Impact to the Customer
The robotic automation system MWES provides our customer can inspect and assemble 50 parts per minute and can produce 28,800 parts in 24 hours. Product changeovers require 2-3 workers and take approximately 15 minutes to complete. This level of performance is unrivaled when compared to a strictly manual labor operation.
Midwest Engineered Systems has a wide range of experience integrating robotic assembly automation systems. If you’re looking to improve your assembly throughput, we have the knowledge and experience to make the project a success.
Contact us to learn about how Midwest Engineered Systems can automate even your most complex and challenging operations today.
Innovation Through Automation
Client Details
A global leader in industrial equipment manufacturing.