In the dynamic world of logistics and supply chain management, inventory strategies play a pivotal role in ensuring businesses can meet customer demand without incurring unnecessary costs. Traditionally, businesses have relied on a Just-In-Time (JIT) production strategy. However, more companies are increasingly shifting from a JIT strategy to a Just-In-Case (JIC) approach. This transition is driven by the need for greater supply chain resilience in the face of unpredictable market conditions and disruptions. A strategy that minimizes inventory and relies on timely delivery of components, has been challenged by recent global events that have caused significant supply chain disruptions.
In contrast the Just-in-Case (JIC) inventory approach, which, as the name suggests, is a risk-averse inventory management approach where companies maintain large buffer inventories to minimize the risk of stockouts. This strategy is particularly useful for businesses that face unpredictable consumer demand or those that experience sudden surges in demand. As we saw during the COVID-19 pandemic many industries and businesses were unprepared for the worldwide manufacturing stoppages and global supply chain disruptions that followed.
A JIC strategy would have alleviated some of the financial headaches during that time and is still a relevant strategy today with rising shipping container costs and ongoing high interest rates. Those scenarios can hit your bottom line hard if your business is unprepared for it. By keeping larger inventories on hand, you can minimize the risk of stockouts, leading to lost sales and customer dissatisfaction.
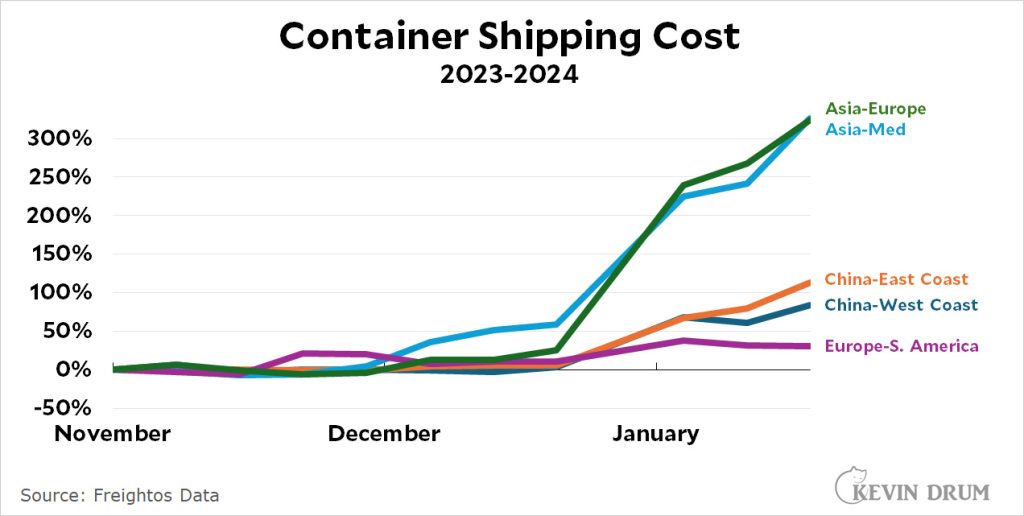
Additionally, the rising shipping container costs reportedly can increase domestic inflation rates by a noticeable amount which will cut into your business’s growth. Looking back at previous inflation rate spikes, and if history repeats itself, we could see interest rates jump again in the near future as a measure to slow the economy.
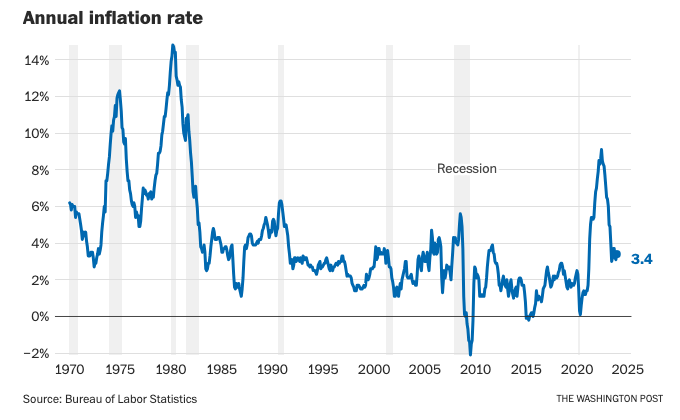
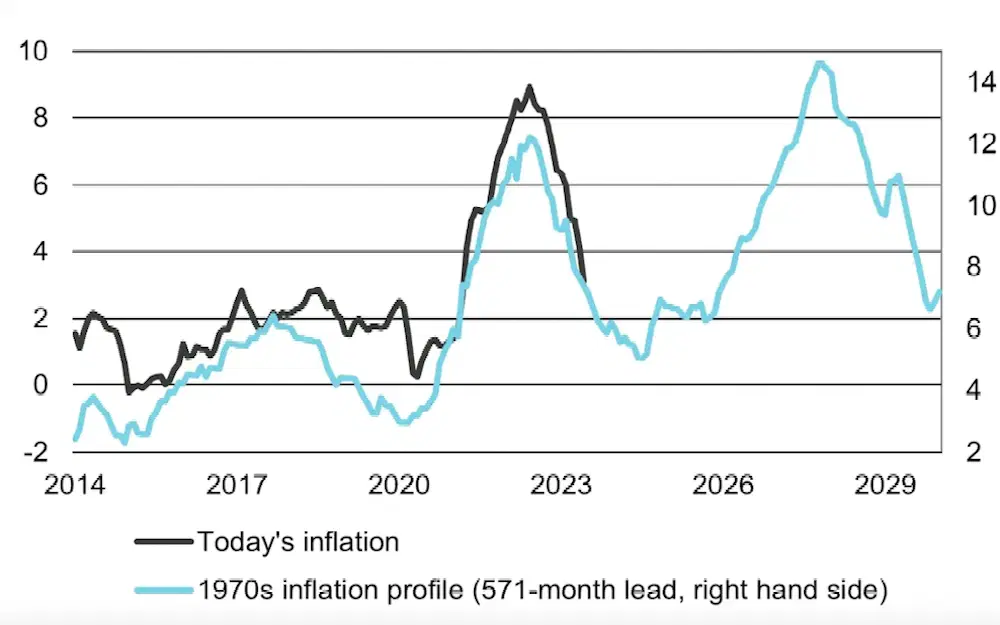
One solution that businesses are implementing to alleviate the rising costs is near-shoring their manufacturing and warehousing operations to local countries such as Mexico. Near-shoring and re-shoring eliminate the volatile costs and delays associated with shipping long-distance overseas from China and India and put more reliance on established rail or trucking networks.
The inclusion of material handling automation into your process can have a profound impact on your bottom line whether they are domestic or across the border.
Add Robotic Automation to your Material Handling Process
Warehousing and distribution centers are undergoing a significant transformation, driven by the need to address inventory shrinkage, high labor costs and the demands of lights-out and round-the-clock operations. Robot automation has been a game-changer in this industry over the last decade. Through advanced technologies such as Artificial Intelligence (AI), machine learning and the Internet of Things (IoT) in warehouses and fulfillment centers, robots are transforming the Just-In-Case strategy from a cost-intensive approach to a more efficient and responsive system.
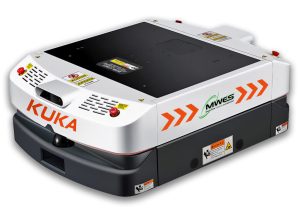
Material handling robots in warehouses can perform many tasks, from sorting and retrieving inventory to tracking stock levels and generating replenishment orders. They bring a level of precision and efficiency that manual processes cannot match. For instance, Automated Guided Vehicles (AGVs) and Autonomous Mobile Robots (AMRs) can easily navigate through warehouse aisles, transporting goods from one point to another with minimal or no human intervention.
Additionally, automated storage and retrieval systems (AS/RS) can efficiently manage inventory, and reduce manual labor, healthcare costs and the space required for pallet racking. Automated technologies can track inventory in real-time with barcode scanners and RFID tags, ensuring accurate data on stock levels. They help prevent stockouts and overstocks by providing timely information for decision-making. These technologies not only speed up the process and increase throughput but also eliminate human errors or even theft, which even a large corporation like Amazon has experienced recently.
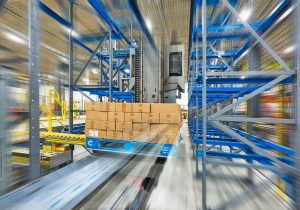
Robotic systems can work around the clock, providing a continuous flow of operations that human workers cannot sustain. This 24/7 lights-out productivity is crucial for businesses that operate on tight schedules and need to respond quickly to sudden surges in demand. Robotic automation systems can gather and analyze data by utilizing sensors and cameras. These systems can continuously monitor inventory levels, predict future demand based on historical data, and even identify patterns that might indicate upcoming trends. A data-driven approach allows businesses to make more informed decisions about inventory levels, reducing both overstock and understock situations.
The financial aspect of robotic automation cannot be overlooked. With labor, materials and shipping costs putting pressure on businesses’ bottom lines, automation is emerging as a cost-effective solution. By streamlining order fulfillment processes and reducing operational expenses, warehouses can compete more effectively in a challenging global economic landscape.
How MWES Integrates Material Handling Automation into Your Warehouse
As we move through this decade, the pace of material handling automation within the warehousing sector is accelerating, offering a glimpse into a future where efficiency and continuous operation are paramount. Integrating robotic automation into the Just-In-Case warehouse inventory strategy offers a compelling solution to the challenges of managing large inventories. It enhances the responsiveness and efficiency of the supply chain, reduces costs and ultimately leads to better customer satisfaction.
Midwest Engineered Systems has extensive experience in automating all aspects of warehouse and fulfillment operations. We have successfully integrated AGVs, AMRs, AS/RS buffer systems, palletizing and depalletizing systems, barcode scanning systems and more. If you have a warehouse or distribution facility and want to improve your throughput, contact us today.
We have the solutions to robotically automate every aspect of inventory management strategies across all industries and the benefits manifest in improved efficiency, safety and profitability.