Types of Industrial Robots
- Home
- Types of Industrial Robots
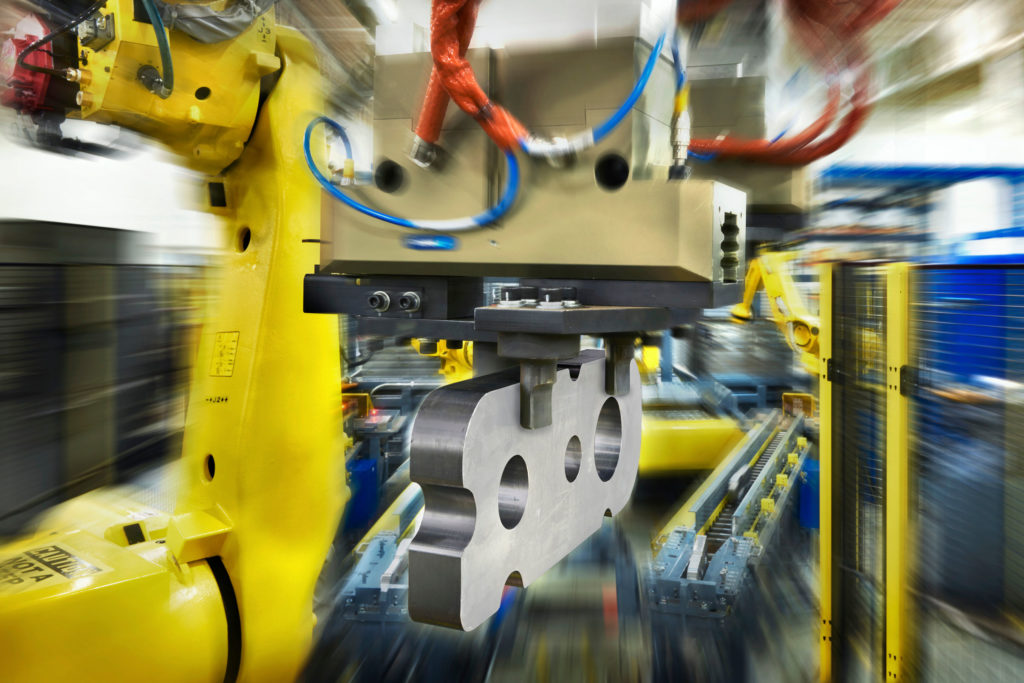
Industrial Robots are our specialty
As a multi-industry, multi-vendor production automation integrator, Midwest Engineered Systems has experience specifying and programming a variety of industrial robot types. MWES has been integrating industrial robots into automation systems for over three decades and we have extensive experience with all forms of industrial robotics from small SCARA robots to huge articulated robots designed for heavy loads.
What are the Different Industrial Robots
Industrial robots have many benefits such as improving productivity, quality, safety and flexibility. Robots provide a substantial return on investment (ROI) compared to manual labor. When it comes to industrial robots, there are five types commonly used today. Each of these has its own unique joint configuration, load capacity and application.
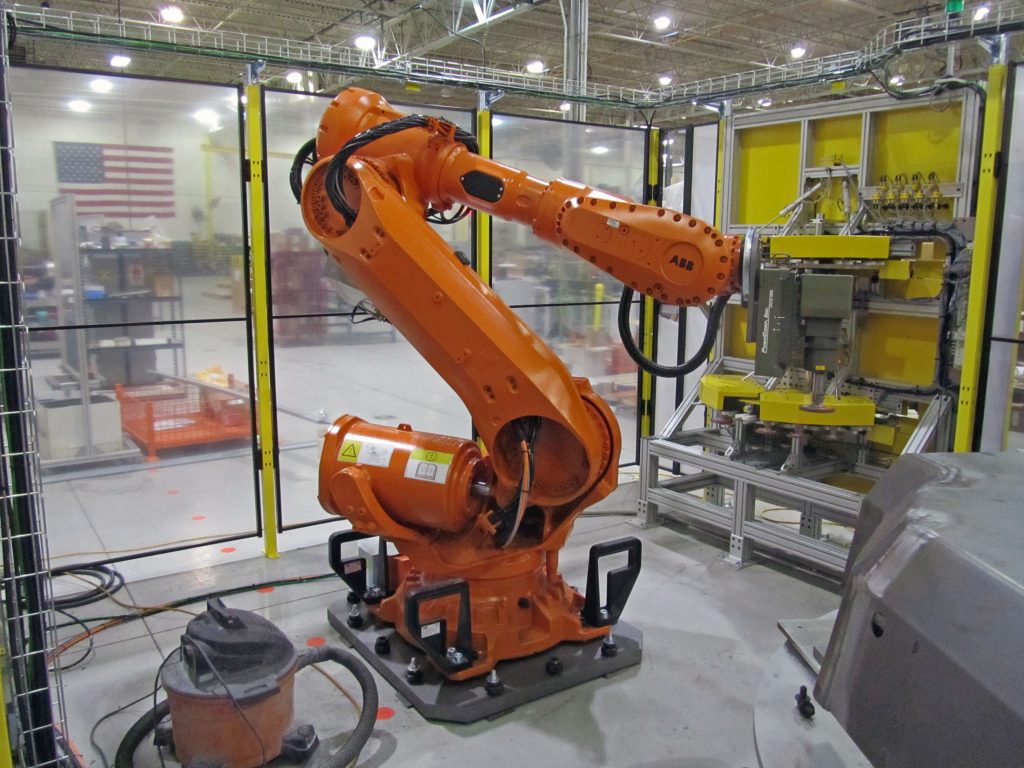
Articulated Robots
Industrial articulated robots are designed to have as few as two joint structures/axis and as many as ten joint structures. Typically, articulated robots have four to six axes and are well-known for having the most degrees of freedom, or relative range of motion, compared to any other robot type in the industrial field. Articulated robotic systems are also the most commonly used in industrial factories and warehouses around the world.
Articulated Robots are integral in many automation systems, as they can increase a company’s productivity by improving the accuracy, product quality and efficiency of its operations. Articulated robots are very affordable in the industrial markets due to their many years of serviceability and long-standing popularity which assures them an impressive return on investment.
Applications
- Automated part handling and part picking processes
- Automated insert loading
- Inspection automation
- Assembly cell automation
- Automated In-Mold Labeling (IML) and In-Mold Decorating (IMD)
- Automated packaging and palletizing
- Automated stacking and sorting
- Automated over-molding and press to press transfer
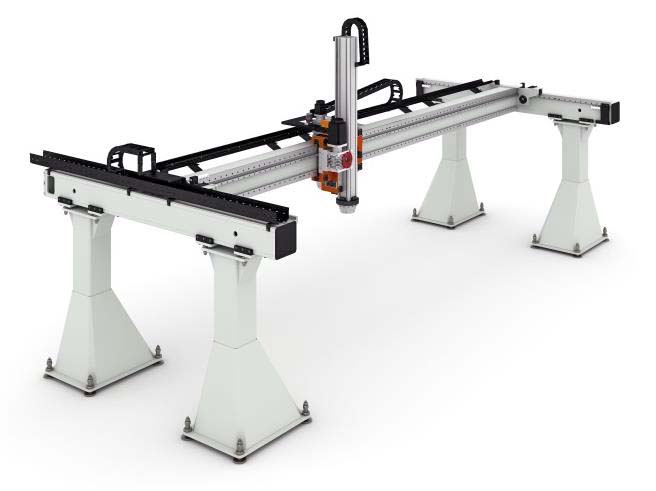
Cartesian, Rectilinear & Gantry Robots
Cartesian robots are designed with three linear joints, working off of the X-Y-Z Cartesian coordinate system. These robots may also have an end-of-arm tooling or rotary axis, that will allow for rotational movements on the robot’s outermost axis. The axes of Cartesian robots carry out movements in a coordinated manner via a motion controller they have in common. These axes are crafted from a type of linear actuator, a system that can be custom-manufactured by an end-user with drive and linear guide components, by the Original Equipment Manufacturer (OEM) or the system can be bought as a manufacturer’s pre-assembled system.
Rectilinear robots share many of the similarities with cartesian robots. They consist of either a two-axis X-Y or X-Z or a three-axis X-Y-Z configuration and the workload positioning is supported on the outer axes of Y or Z. Additionally, rectilinear robots have simplified programming due to fewer motions and axes running on a well-defined rectangular work envelope.
Gantry robots are a bit different from Cartesian robots. Gantry robots always have two base X axes and a second Y axis that spans the two base axes. Cartesian robots have a single linear actuator per axis. With this configuration, gantry robots can have bigger payloads in most cases and typically greater stroke lengths than Cartesian robots.
Applications
- Packaging automation
- Palletizing and depalletizing operations
- Product placement automation
- CNC machine automation
- Cutting, sorting and scribing automation
- Consumer and industrial 3D printing equipment
- Storage and retrieval systems
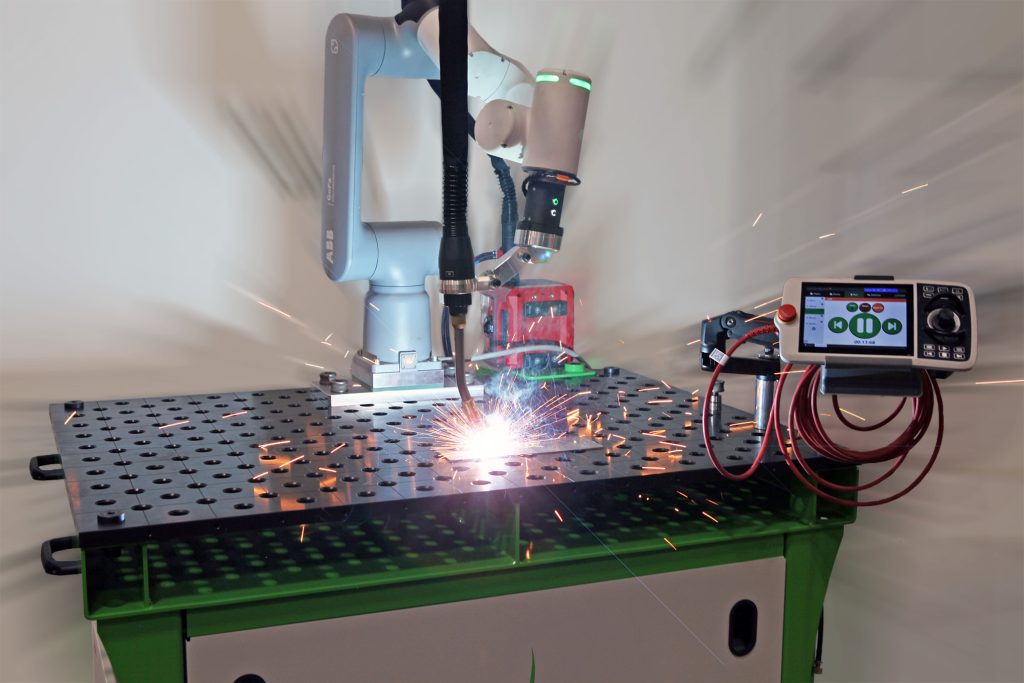
Collaborative Robots (Cobots)
Collaborative Robots – or Cobots – are a class of industrial robots that combine a series of safety features with conventional industrial robotics. These safety features work to mitigate the more dangerous aspects of production robotics. This is a step change from conventional robotics. Normally, there are requirements to segment the industrial robot from the human workforce through a complicated installation of physical fencing or arrays of electronic sensors designed to react to any unplanned activity in the work cell.
Breaking down these barriers allows the human workforce to work within the same functional areas as robots or even work with these systems. This comparatively close-knit interaction produces certain advantages for the right production operations.
One of the first areas where collaborative robots saw use was tending other machines. Firms with CNC or molding machines found these cobots to be a great addition to their production operations. To start, the robots tended to be lower on the cost scale. Their inherent safety systems, allowed the robots to work in tighter areas. These spaces were nearly impossible for conventional robots to operate due to the greater need for safety equipment and fencing. Loading and unloading the cells could also be achieved more easily as the collaborative robots are designed to sense humans in their areas and slow down or stop until the person has left.
Packaging and palletizing operations are other areas where collaborative robots can be advantageous. These robotic systems can perform the more repetitive aspects within an integrated space while humans provide ancillary tasks like removing filled containers or transferring trays. With the cobot’s safety features, the combined operation can take up much less space than conventional automation without compromising safety.
Dispensing and testing operations have also seen interest in cobots. When the repeatability of robotics meets the safety of collaborative robots, precision processes can certainly benefit. The in-built safety systems allow for these robots to work in much smaller envelopes and make interaction easier for technicians to move through the product. Without these safety features, automated systems would require automation of infeed and outfeeds. These extra feed systems take up space and reduce flexibility.
While collaborative robotics offers a lot of promise for a variety of industries and applications, building successful implementations using the technology can be tricky. It’s best to partner with a skilled robotic systems builder to ensure the best results will be found.
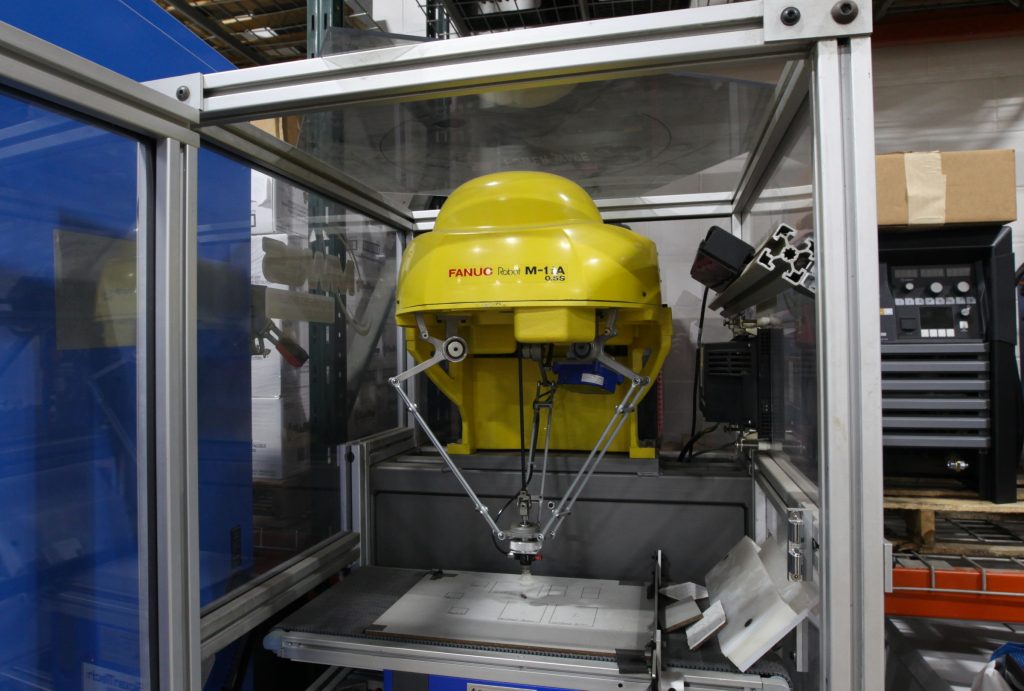
Delta Robots
Delta robots, sometimes referred to as spider or parallel robots, are robots with a base connected to jointed parallelograms. These parallelograms perform motions in a solitary end of arm tooling (EOAT), within a workspace that is dome-shaped. This type of robot is well-known in the industrial field for its ability to execute minute, precise motions.
Delta robots are primarily operated when production is required for groups of objects and these objects must be placed in either an assembly pattern or inside of a container. With the addition of capable vision technologies, delta robots can properly identify and select a range of object colors, shape options and sizes. They can also use these vision technologies to pick and place working from a programmed pattern or design.
These types of robots can work with more than 100 parts per minute, picking, placing and sorting them much faster than manual labor processes are capable of performing. Their design allows them to very efficiently perform repetitive tasks at a highly consistent rate. A chief benefit of delta robots revolves around the fact that their relatively heavy motors are attached to the robot’s frame, permitting the robot’s moving parts to be very light by comparison.
Applications
- Automated case packing operations
- High-precision assembly processes
- Medical and pharmaceutical processes
- Food processing and handling
- Packaging automation
- Soldering operations
- Adhesive dispensing and placement processes
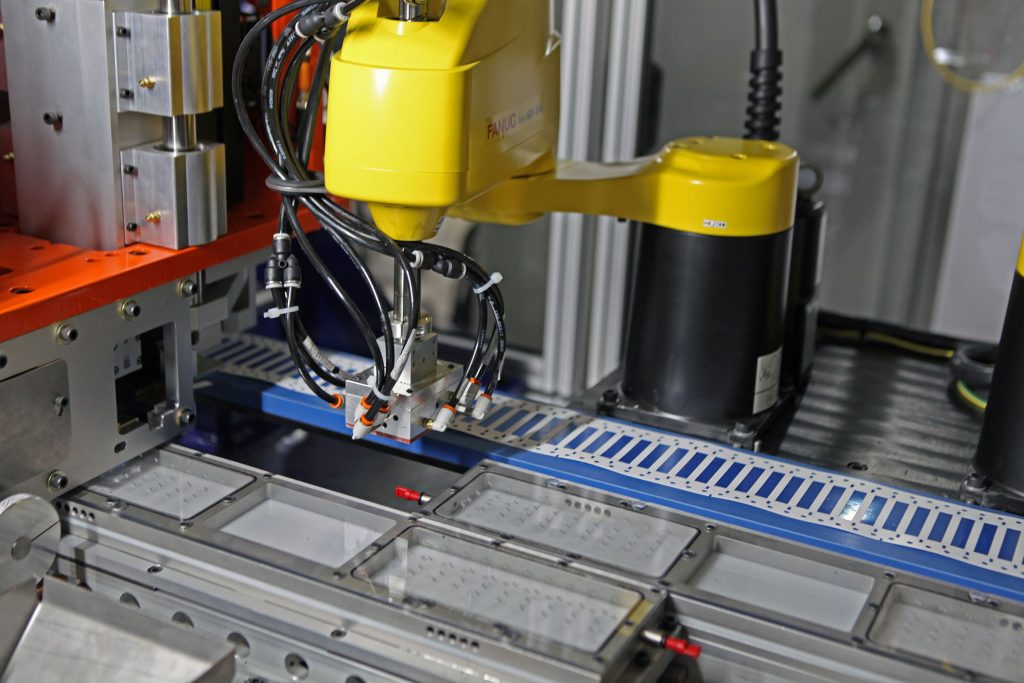
SCARA Robots
Selective Compliance Assembly/Articulated Robot Arms (SCARA) are typically used in quick assembly procedures that can be handled by small robots. One chosen plane is used for compliance and features two parallel joints. This selective compliance means that while it is rigid as far as the Z-axis is concerned, it is compliant when it comes to the X-Y axes. SCARA robots can handle many types of material handling processes due to their atypical configuration. The structure of a SCARA robot is an intersection of two robotic arms, with both arms joined together at the base. A SCARA robot’s X-Y motions are controlled using two independent motors. These motors use the processes of interpolation and inverse kinematics to control the robotic motions across these axes.
SCARA robots tend to be the fastest of all the industrial robot types in the industry. These robots have simplified calculations involving inverse kinematics, resulting in reduced computational time and cycle time compared to other robot types. They also tend to rate the highest of all industrial robotic types in terms of repeatability performance. Extremely high repeatability is a must in all applications that relate to small assemblies, as their tolerances can be as small as a few microns.
Applications
- Pick and place operations
- Small assembly operations
- Sealant application process
- Machine tool handling
- Dispensing and placement applications
End-Of-Arm-Tools (EOAT)
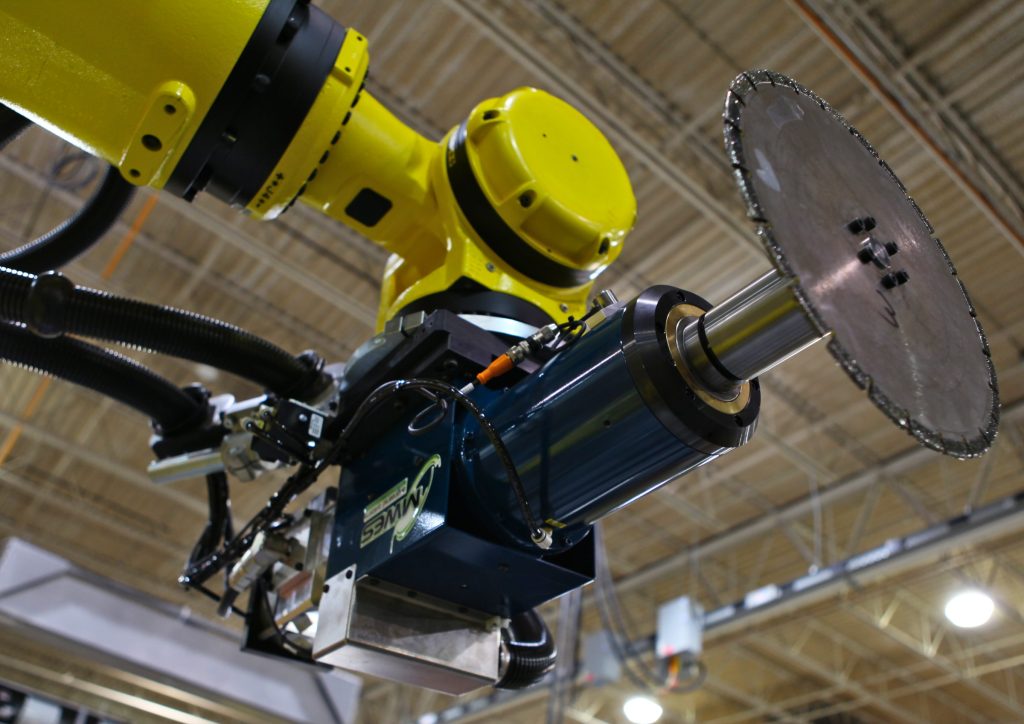
End effectors, more commonly known as End-Of-Arm-Tools (EOAT), are the hands of a robot arm and as such a critical component that directly interacts with the environment. End effectors can comprise a combination of grippers, collision sensors, force-torque sensors, vision systems and custom material processing tools. Additionally, tool changers allow the robot to quickly switch out its EOAT autonomously without operator intervention.
The options and interchangeability are endless with all the tooling currently available. Since they are simple to install and offer a lot of power in a tiny container, pneumatic EOATs have proven to be the most common solution for material handling robots. Pick-and-place tasks are excellent candidates for automation and robots’ grasping abilities have improved dramatically in recent years.
MWES is a Certified Robotic Integrator
MWES has been an A3 Certified Robot Integrator since 2013 and we pride ourselves on the expertise we bring to our customers. We have advanced expertise in all the popular robot vendors.
Contact Midwest Engineered Systems to learn how we can analyze your current production systems and develop an industrial robotic automation system that increases productivity and efficiency!
Building the future of manufacturing, together
World-class Automation