Collaborative Robots (Cobots)
- Home
- Types of Industrial Robots
- Collaborative Robots (Cobots)
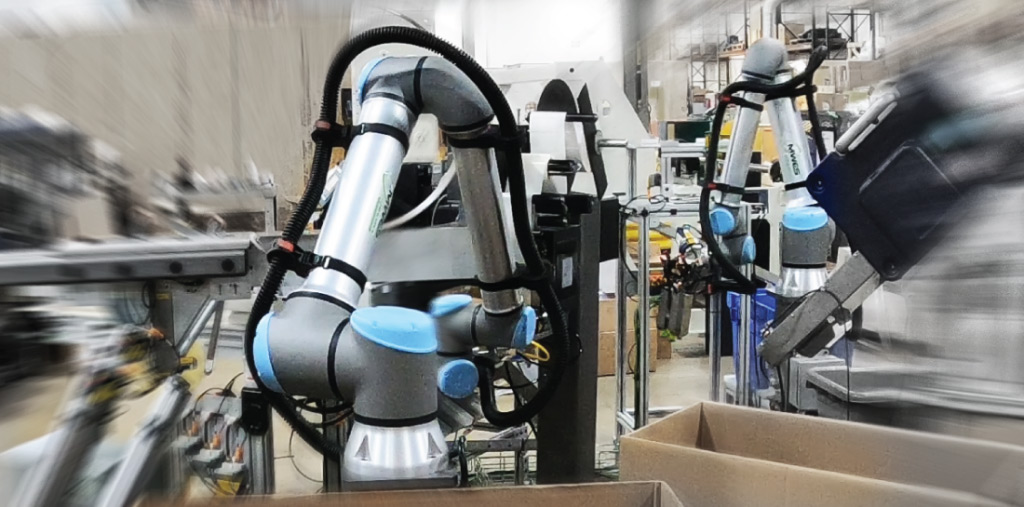
Cobots are the Robots of Choice When Working Side-by-Side with Humans
Collaborative Robots – or Cobots – are a class of industrial robots that combine a series of safety features with conventional industrial robotics. These safety features work to mitigate the more dangerous aspects of production robotics. This is a step change from conventional robotics. Normally, there are requirements to segment the industrial robot from the human workforce through a complicated installation of physical fencing or arrays of electronic sensors designed to react to any unplanned activity in the work cell.
Breaking down these barriers allows the human workforce to work within the same functional areas as robots or even work with these systems. This comparatively close-knit interaction produces certain advantages for the right production operations.
One of the first areas where collaborative robots saw use was tending other machines. Firms with CNC or molding machines found these cobots to be a great addition to their production operations. To start, the robots tended to be lower on the cost scale. Their inherent safety systems, allowed the robots to work in tighter areas. These spaces were nearly impossible for conventional robots to operate due to the greater need for safety equipment and fencing. Loading and unloading the cells could also be achieved more easily as the collaborative robots are designed to sense humans in their areas and slow down or stop until the person has left.
Packaging and palletizing operations are other areas where collaborative robots can be advantageous. These robotic systems can perform the more repetitive aspects within an integrated space while humans provide ancillary tasks like removing filled containers or transferring trays. With the cobot’s safety features, the combined operation can take up much less space than conventional automation without compromising safety.
Dispensing and testing operations have also seen interest in cobots. When the repeatability of robotics meets the safety of collaborative robots, precision processes can certainly benefit. The in-built safety systems allow for these robots to work in much smaller envelopes and make interaction easier for technicians to move through the product. Without these safety features, automated systems would require automation of infeed and outfeeds. These extra feed systems take up space and reduce flexibility.
While collaborative robotics offers a lot of promise for a variety of industries and applications, building successful implementations using the technology can be tricky. It’s best to partner with a skilled robotic systems builder to ensure the best results will be found.
As a multi-brand robot integrator, Midwest Engineered Systems has experience designing, building and programming collaborative robot implementations. Contact us today to learn if a cobot is the right solution for your application.
Building the future of manufacturing, together
World-class Automation