It’s easy to believe that most collaborative robots or ‘CoBots’ are plug-and-play. Unpack the robot and after a few steps, it starts producing. Many times, this just isn’t the case.
While industrial robotics are getting easier to implement, they are still complex machines, even Cobots. There are very few simple tasks for a robot and every production situation demands a specialized operation – which also means everything needed to make it work probably isn’t included in the box. It’s no surprise to find many have purchased these entry-level robots only to find out it takes more than they thought to make it go.
With that experience in mind, we’ve put together three important truths about collaborative robots that a manufacturing engineer or manager should understand before taking the plunge on a cobot for their processes.
Cobots tend to run slower when working with humans
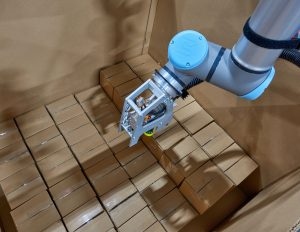
Collaborative robots deliver a safer interactive experience in two ways. The first is built-in force feedback sensing which can determine whether it comes into contact with something unplanned. The other is they travel slower than conventional industrial robots.
Typically, when a human enters the robot’s area, both of these come together to reduce dangerous robot situations. This causes a collaborative robot to generally run slower than its top speed when working with humans. If a lot of human interaction is required, it’s going to be difficult for the robot to work at its fastest speeds.
Simple tasks are relatively simple to program, complex tasks require real programming
Most robots found in the collaborative space have path teaching capability. This programming process amounts to miming the robot through the production process. It makes simple operations like picking up a part, putting it in a machine or vice versa a snap to program.
If the robot needs to add more complexity than the simplest of pick and place to its process, that complexity will need to be programmed with actual code. The firm will need to have on hand a resource that knows how to program this sort of robot. It might also be time to bring in an integrator who does this all the time to make sure it’s done well.
The robot’s price is not the total automation cost
Many times, Cobots are sold as a ‘robot in a box’ ready to be unpacked and quickly put to work. The truth is robots are like machine tools: there’s the machine price and a second – usually significant – outlay afterward for the tools and fixtures to use the machine. For robots, this comes in the form of End of end-of-arm tools (EOATs) or part grippers. Trays are also required to hold parts for the robot in as exacting of a location as possible. Then how the robot will interface with the machine tool will have to be sorted out. This is done with a bit more additional equipment including a programmable logic controller (PLC) that interfaces between other machines, conveyors and sensors.
An often-overlooked cost in bringing in robotic automation (even Cobots) is making sure the facility’s insurance will cover the installation and the system’s operation. Before insurance firms will properly cover the system, an on-site risk assessment by a qualified third party is required. These assessments look to ensure that proper safety guidelines are followed to reduce dangerous conditions from happening during the installation and operation of the robot.
All of these aspects aside, collaborative robots will continue to be a game-changer for production settings, but it’s important to develop a complete understanding of what is truly needed for automation.
For a production environment that may not have a lot of experience with industrial robotics, it may be best to partner with a trusted integrator, like Midwest Engineered Systems. We can assess a facility’s needs and develop a solution that sidesteps the common pitfalls that the cobot hype glosses over.
Contact us today if you’re considering robotic automation with collaborative robots. Trust our decades of automation experience to guide your firm to a successful cobot outcome!