Robot Die-Cast Machine Tending Automation
- Home
- Recent Projects
- Robot Die-Cast Machine Tending Automation
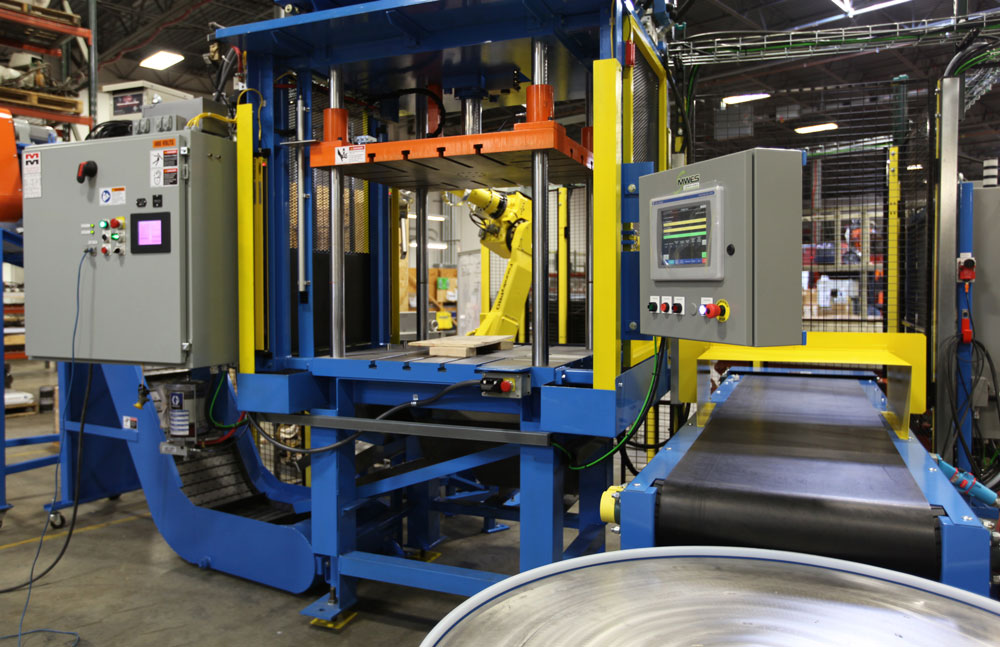
Project summary
MWES provided a manufacturer with an automated robot die-cast tending system for producing different types of hardware for consumer and industrial doors.
The Challenge
Manually tending a metal die-cast machine is hard work for a human worker and is more suited for a robot solution. MWES was contracted by a firm to produce an automated solution for tending a Frech Die Cast Machine. Additionally, the automation system would be responsible for loading the die-cast parts into a Trim Press. The final system had to achieve an 18-second part-to-part cycle time.
The Solution
After a full evaluation of the project’s challenges and goals, MWES provided our customer with a complete solution that included: a Fanuc Robot with a pneumatic gripper EOAT, a part verification stand, a motorized turntable, outfeed conveyors and a dunk quench system. Additionally, the system features several safety measures that follow ANSI/RIA R15.06-2012 to prevent accidental interaction by the operators.
The robot machine tending system starts when the die-cast machine opens and signals the robot to unload the parts. The robot then enters the die-casting machine, grips the part by the sprue and extracts the part from the die. Once the robot has removed itself from the die-casting machine, the machine is free to perform another shot. The robot moves the part to the part verification stand and verifies that the part is on the EOAT. It then moves the part to the quench booth and quenches the part for 3 seconds.
If trimming is required, the robot moves the part and loads it into the trim press. Lastly, the robot places the part on the outfeed cooling conveyor where the operator can handle it. However, if a part is rejected, the robot places the part into the scrap chute, where the part is transferred to the scrap conveyor and up to the furnace for reprocessing.
Features of the Machine Tending System
- Fanuc Robot – This includes an M710iC/50 Fanuc robotic arm with an R-30iB Mate Controller, DCS Position and Speed Check, ASCII Program Loader, Soft Float and PC Interface.
- Robot End Effector – The equipment includes a robot EOAT with a pneumatic gripper system, cable harness and robot mounting base.
- Part Verification Stand– This includes a stand and sensor array for part presence after the extraction process has been completed.
- Dunk Quench System – The equipment includes a welded stainless steel tank, heat exchanger, HP Pump, all necessary controls for the system, all necessary valves, and all necessary piping and filtering.
- Cooling Conveyor and Scrap Conveyor/Chutes – Integration of outfeed conveyors and reject chutes into the system.
- Motorized Turntable – Integration of a turntable allows parts to accumulate. This meant the die-cast and robotic part extraction process could continue if the operator were to step away for a few minutes. In addition, the Turntable part accumulator allowed for efficient use of floor space.
- Safety Features – This includes black mesh safety guarding, safety interlock door access, RAG stack light and emergency stop button. The safety solution supplied met the requirements set forth by ANSI/RIA R15.06-2012.
- Controls System – electrical enclosure, electrical panel, power transformers, over current protection, Allen-Bradley CompactLogix PLC, Allen-Bradley Panelview Plus Compact 1000 machine interface, electrical control interface for all system I/O, conveyor motor starters or drives, and safety system interface.
Impact to the Customer
The final robot die-cast tending automation system provided our customer with many benefits such as a more efficient and quicker part-to-part cycle time of 18 seconds or less with higher throughput overall. This also included higher-quality results, improved operator safety, improved error recovery, improved equipment maintainability and improved scrap recovery, by having the MWES Scrap Recover System fed scrap directed back to the furnace. This system provided this firm with a lights-out operation that improved overall equipment effectiveness (OEE) and improved floor space utilization.
Midwest Engineered Systems has a wide range of experience with integrating robotic machine tending systems. If you’re looking to improve your machine tending throughput, we have the knowledge and experience to make the project a success.
Contact us to learn about how Midwest Engineered Systems can automate even your most complex and challenging operations today!
Innovation Through Automation
Client Details
A consumer and heavy industry door hardware manufacturer based in New Hampton, IA.